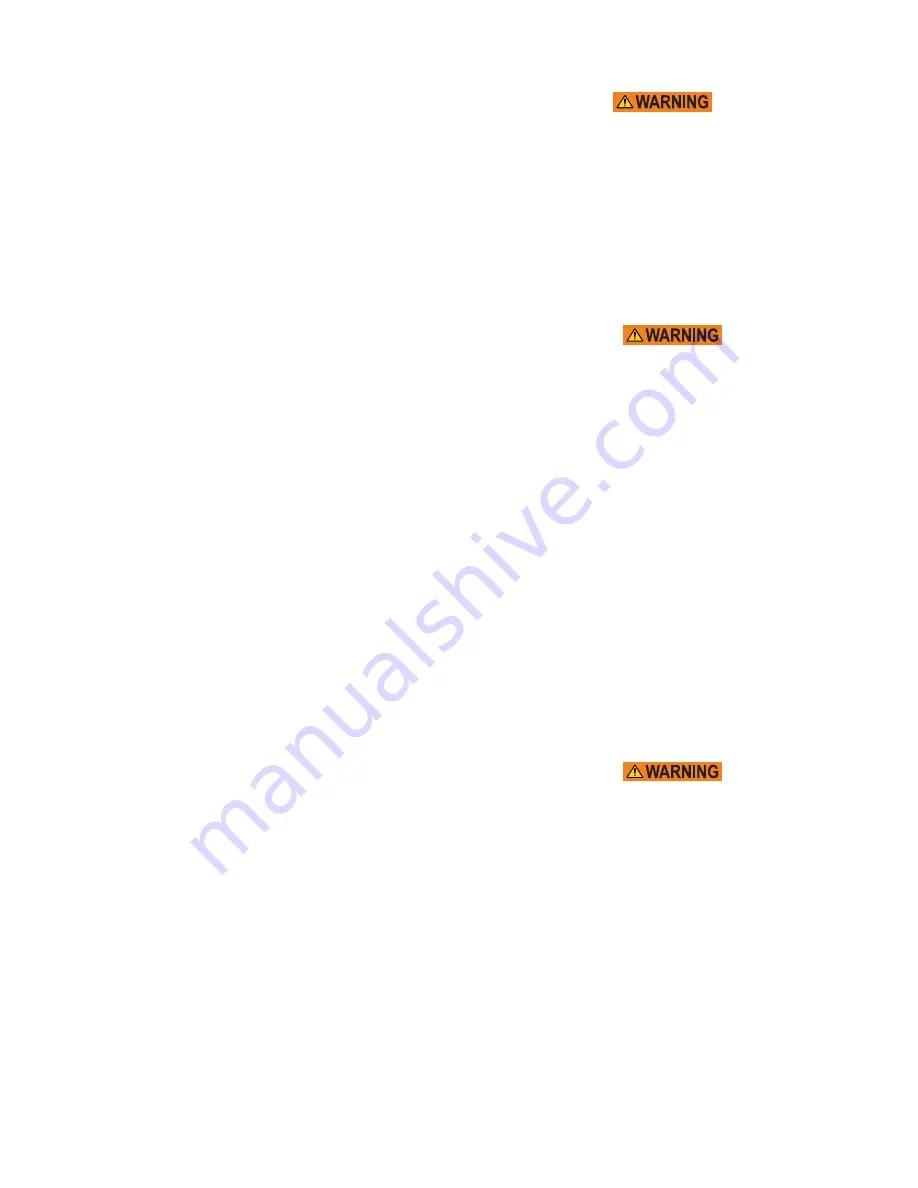
APCU Owner’s Manual
33
Adjustment and
Replacement Procedures
Aligning the Photo-Eyes:
1. The photo-eyes are part of a system which protects
the operators from moving parts which are poten-
tially dangerous. If an operator moves close to the
loading end of the machine, and breaks any of the
3 light beams, the unit will stop immediately. The
unit will not run again until the control system has
been reset.
Each eye sends a light beam to a matching reflec
-
tor. The beam is then returned to the light sensor.
2. When the machine is turned on, check the LED
indicator on the side of the photo-eye.
If the photo eye is properly aligned and is not
blocked, with the beam returning from the reflector,
the LED will light. If the photo-eye cannot see the
reflector, or the beam is blocked, the LED will be
out. If necessary, move the reflector until the LED
lights.
3. If the LED will not light, yet the reflector seems to
be aligned, check that the photo eye is receiving
power.
About the Proximity/Limit Switches:
1. On this machine, proximity switches are used as
limit switches. Each switch has two parts - a sen-
sor and a target. Each switch is a “normally open”
type.
2. The nominal distance between each sensor and its
target is 3/16”. If the sensor can see the target, the
LED on the side of the sensor will light. If neces-
sary, change the alignment of the target or sensor
until the LED lights.
3. If the LED will not light, yet the target seems to be
aligned, check that the proximity switch is receiving
power.
Setting End of Travel for “Tilt Down” Function:
This proximity switch is located on the mid-point of one
side of the machine base. The target for this switch is
located on the bottom back outside corner of the load
enclosure.
1. Set the unit so that the loading edge of the load
enclosure is touching the floor.
WARNING!
I
f any part of the base plate contacts the
floor, except for the front lip, you must
shim the base of the machine.
2. Position this switch so that the load enclosure stops
lowering when the front lip of the load enclosure just
contacts the floor. When the load enclosure reaches
this limit, the switch should send a signal to stop the
motor on the hydraulic power unit.
WARNING!
If the motor continues to run after the front of
the load enclosure touches the floor, the unit
may try to lift itself off of the floor. This can
damage the machine. To correct this problem,
move the target so that it activates the switch
sooner.
Setting End of Travel for “Tilt Up” Function:
This proximity switch is located on the top outside edge
of the tilt frame. It is positioned close to the discharge
end of the machine. The target for this switch is located
on the top back outside edge of the load enclosure.
1. Set this switch so that the tilt function of the load
enclosure stops just as the frame of the load enclo-
sure hits the stop pads, or just a moment before.
When the load enclosure reaches this limit, the
switch should send a signal to stop the motor on
the hydraulic power unit. A clearance of 1/8” from
the pads is acceptable.
WARNING!
If the frame of the load enclosure is allowed to
hit the stop pads with too much force, it will
have an erratic motion. It may even bounce off
of the pads and begin the “Tilt Down” part of
the cycle by itself.
Setting End of Travel for “Dump Up” Function
This proximity switch is located on top of the back up-
right tube of the base frame. The target for this switch
is located on the top back side of the tilt frame.
1. Position this switch so that the load enclosure
stops dumping at the desired angle. When the
load enclosure reaches this limit, the switch
should send a signal to stop the motor on the
hydraulic power unit.
Содержание APCU Series
Страница 11: ...APCU Owner s Manual 11 Fig 3 Label Diagrams and Positions...
Страница 12: ...12 APCU Owner s Manual Fig 3A Label Diagrams and Positions...
Страница 13: ...APCU Owner s Manual 13 Fig 3B Label Diagrams and Positions...
Страница 14: ...14 APCU Owner s Manual Fig 3C Label Diagrams and Positions...
Страница 15: ...APCU Owner s Manual 15 Fig 3D Label Diagrams and Positions...
Страница 16: ...16 APCU Owner s Manual Fig 3E Label Diagrams and Positions...
Страница 17: ...APCU Owner s Manual 17 Fig 3F Label Diagrams and Positions...
Страница 18: ...18 APCU Owner s Manual Fig 3G Label Diagrams and Positions NOTICE label p n 2998591T...
Страница 37: ...APCU Owner s Manual 37 Figure 7 Hydraulic Schematic...
Страница 38: ...38 APCU Owner s Manual Figure 8 Wiring Diagram...
Страница 40: ...40 APCU Owner s Manual Figure 9 DC Power Supply Kit...
Страница 43: ...APCU Owner s Manual 43 Figure 10B Hydraulic Power Unit...
Страница 44: ...44 APCU Owner s Manual Figure 10C Hydraulic Power Unit...