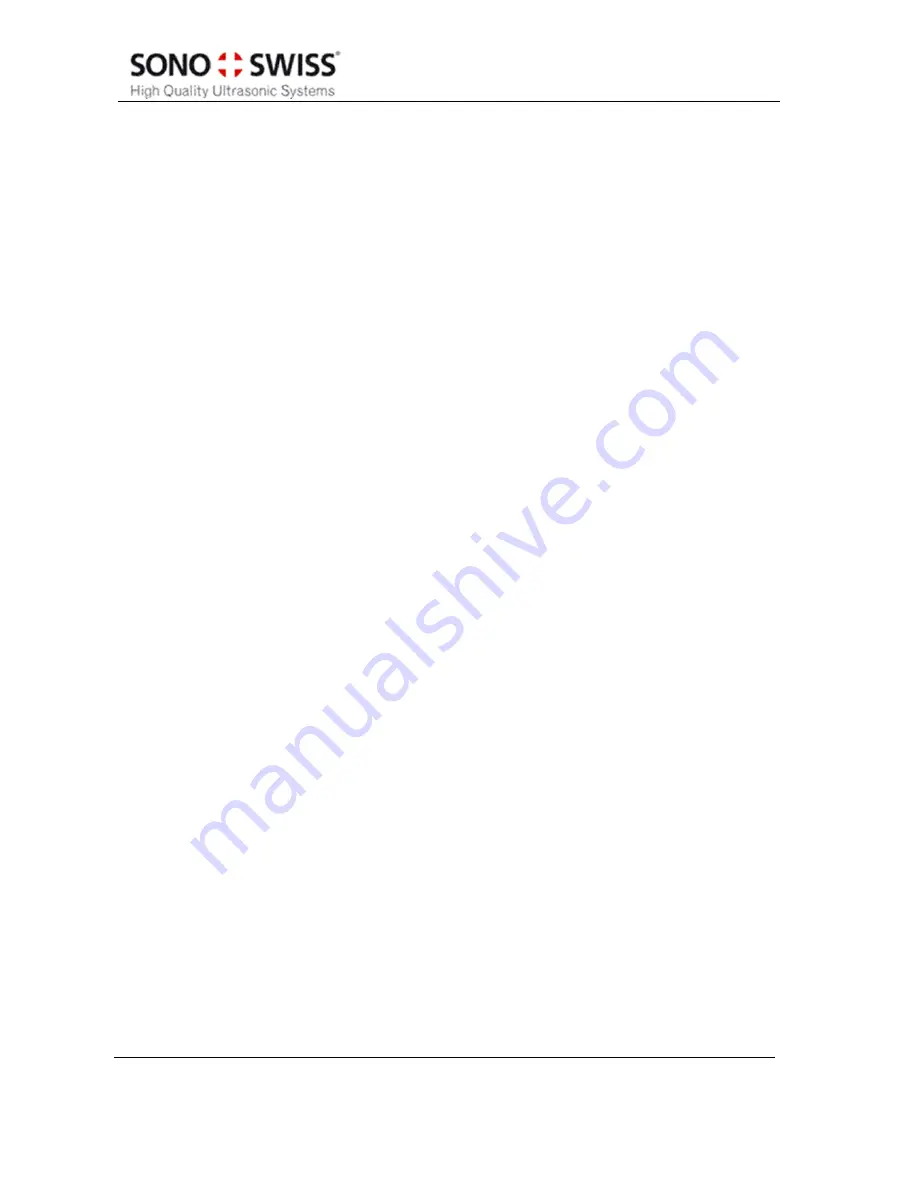
Product description
© Sonoswiss AG
© Sonoswiss AG
BA_Modulrange_SW60/100/200_Sonoswiss_E_06.2012
6
4.2
CE conformity
The present ultrasonic cleaning unit complies with the CE marking criteria with regard to the
EMC directive 2004/108/EG, and to the low voltage directive 2006/95/EG.
The declaration of conformity is available from the manufacturer.
4.3
RFI Statement (European Union)
This is a Class A product.
Please note:
This equipment has been approved for business purposes with regard to electromagnetic
interference.
In a domestic environment this product may cause radio interference in which case the user
may be required to take adequate measures. For this please contact your supplier or the
manufacturer of the unit.
4.4
Delivered equipment
•
Ultrasonic cleaning unit
•
Rinsing tank with heating (optional)
•
Hot Air Dryer (optional)
•
Operating Instructions
4.5
Optional accessories
•
Stainless-steel basket (suitable for small-size items only to a limited degree)
•
Mesh (for heavy pieces)
•
Removable stainless-steel cover
•
Hinged noice-protection cover, (not upgradeable)
•
Oscillation
•
Filtration-system
•
Oil separator