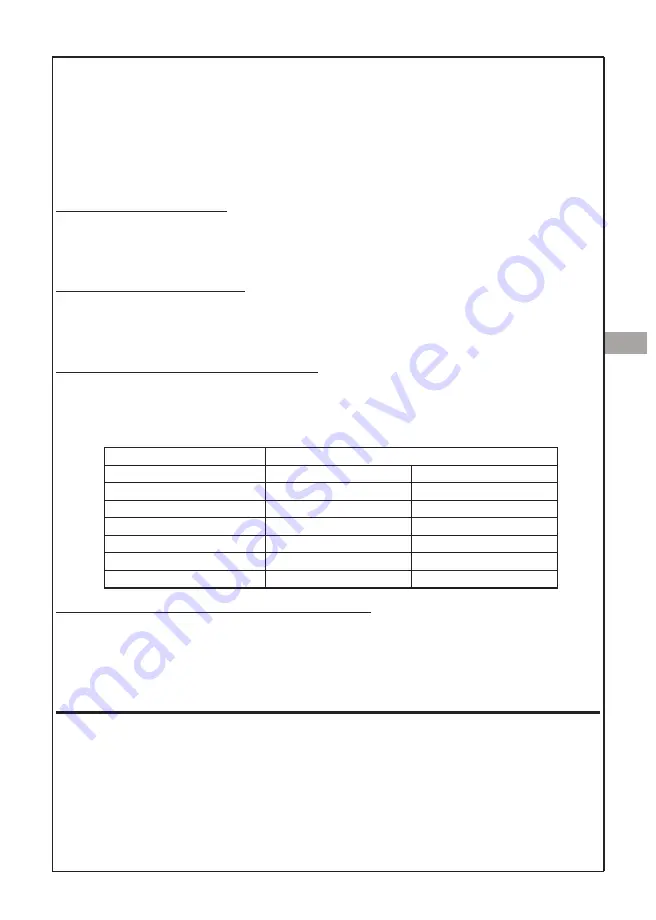
arc tends to spatter and the appearance of the seam is less attractive than that of coated stick
welding. DC current is generally used with the electrode at the positive connection (reverse
polarity), although there are some basic electrodes for AC currents. The basic coatings are
sensitive to humidity and therefore should be stored in a dry place inside sealed boxes. You
are reminded that steels with carbon content of over 0.6 must be welded with special elec-
trodes.
Acid coatings. These coatings provide high degree welding and can be used with AC or DC
with a clamp-electrode on at the negative terminal (direct polarity). The molten pool is highly
liquid and so the electrodes are basically suited to flat welding.
THE CHOICE OF ELECTRODE
The choice of the diameter of the electrode depends on the thickness of the material, on the type of
joint, and on the position of the weld. When “positive” welds are made the pool tends to lower due to
gravity, and therefore use of a small diameter electrode is recommended for repeated welds. Large di-
ameter electrodes need high welding currents which provide adequate thermal energy.
CHOICE OF WELDING CURRENT
The stability and continuity of the weld mean that work can be carried out with low value currents in
difficult conditions.
The following table shows the minimum and maximum current which can be used for carbon steel
welding.
ELECTRODE DIAMETER WELDING CURRENT
The stability and continuity of the weld mean that work can be carried out whith low value currents in
difficult conditions.
The following table shows the minimum and the maximum current which can be used for carbon steel
welding.
WELDING SCHEME WITH COATED ELECTRODE(Fig. 2)
1 - Connect the earth cable to the negative terminal on the welding machine (-).
2 - Connect the electrode-carrier cable to the positive terminal (+).
3 - Insert the electrode into the electrode-carrier clamp.
4 - Connect the machine to the electrical supply.
5 - Place potentiometer nº 2 in a suitable position in order to begin welding.
TIG WELDING PROCEDURE
Gas Tungsten Arc Welding (GTAW) is the name of the welding procedure in which the arc is main-
tained during work through an infusible metallic electrode (usually tungsten)). The area of the arc
(electrode and molten pool) is protected against atmospheric contamination through the use of an inert
gas such as argon or helium which flows continually through the appropriate conducts in connection
with the torch. For purposes of simplification and uniformity all references to this procedure in this
manual use the term TIG (Tungsten Inert Gas).
This procedure may be used in clean and precise welds on all types of metal, respecting their physi-
cal-chemical composition. Due to this characteristic, TIG welding is the only apt method for joining cer-
tain metals.
ELECTRODE DIAMETER
WELDING CURRENT
mm
Minimum
Maximum
1,6
25 A
50 A
2
40 A
70 A
2,5
60 A
110 A
3,25
100 A
140 A
4
140 A
180 A
5
180 A
200 A
SOLTER
SOLDADURA S.L.
INVERTER
4
EN
Содержание COTT-135
Страница 2: ......
Страница 11: ...SOLTER SOLDADURA S L INVERTER 9 ES...
Страница 46: ...SOLTER SOLDADURA S L INVERTER A3 Figuras Fig 1 Fig 2 Fig 3 Fig 6 Fig 4 Fig 5...
Страница 47: ...SOLTER SOLDADURA S L INVERTER A4...