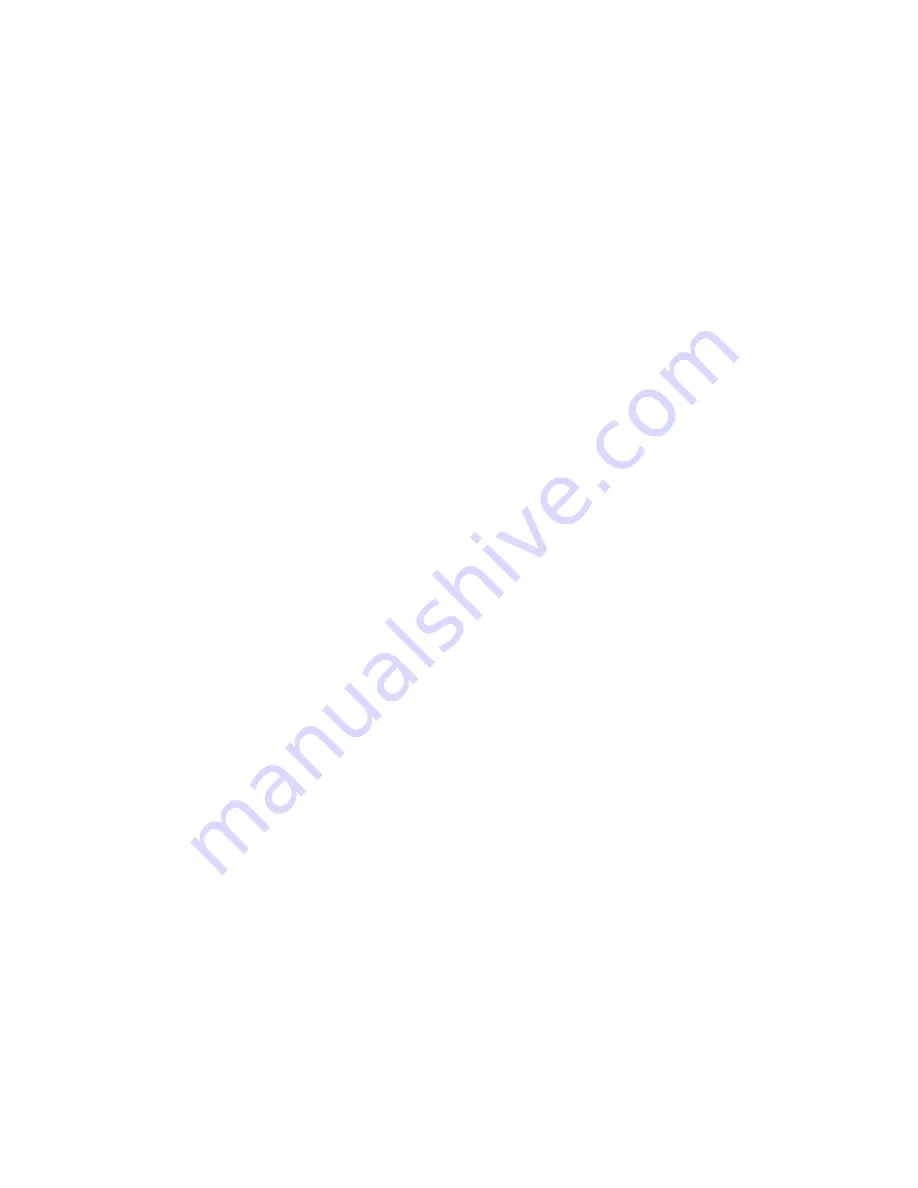
[17]
B. Start Amperage :
This allows you to set the initial start current from 5A DC and 10A AC. In 4T
mode when trigger is pressed and held you will remain at start amps, when you let go machine will then
go to main set amps. Do not set the start amperage too low for tungsten size otherwise you may
experience sluggish / non arc starting. I.E A 3.2mm tungsten is for high range 160+ amps welding, so
you would not need to set start amps at 5. The thicker the tungsten used the higher the start amperage
has to be. We recommend to achieve faster arc starting:-1.0mm Tungsten - 5 Amps minimum1.6mm
Tungsten - 15-20 Amps minimum2.4mm Tungsten - 40 Amps minimum3.2mm Tungsten - 60 Amps
minimum Note:
C. Up-Slope :
Adjustable from 0 - 25 seconds, This allows you to gradually increase the amperage
from start amps to main amps when using torch trigger operation.
D. Welding Amps : Main current control :
This adjusts the main welding current and is shown in
L.E.D when welding is in process. Welding range AC is 5A to 300AWelding range DC is 3A to 300A
E. Pulse Time ON (%) : Pulse width
When pulse welding you have the main (peak) amperage and
base (background)amperage set. By adjusting the width you determine which will be more prominent,
the pulse or the base. This is adjustable from 5-95%. At a low % the base current will be on long so you
will reduce heat input. At a high % the pulse current will be more prominent so you will get increased
heat input..
F. Pulse Amps (%) :
This sets the base amperage as a % of main amps set. I.E if mains amperage is
120A and you set to 50%, base amps will be 60A.
G. Pulse Frequency (Hz) Adjustment :
This can be adjusted as follows: DC Mode 0.1 to 500HzAC
Advanced Squarewave 0.1 - 250HzAC Soft Square, Triangular and Sinewave 0.1 - 10HzAdvanced AC
Pulse 0.1 - 10Hz
H. AC Balance
This sets the % of electrode positive used during AC welding to provide a cleaning
action as alloys have a oxide layer that has a higher melting temperature than the base metal and this
needs to be lifted off. So you can control the amount of cleaning or penetration. Too much cleaning will
cause the tungsten to wobble and split, Too little cleaning can result in a dirty dull weld. So as you
increase the % the more cleaning will happen however less penetration will be achieved. For most
situations a setting of 30 - 40% will give you a good clean weld finish, If you go above 50% you will find
the tungsten will overheat and the end can fall of into weld pool. If you find you are getting tungsten
wobble using 30-40% balance then you may need to go up a tungsten size.
I. AC Frequency
Transformer based welders are normally fixed at 60Hz, due to the advanced inverter
technology you can adjust from 20 - 250Hz.The higher the AC frequency the narrower the arc
becomes allowing you to have a more precise weld bead and penetration. This can also quicken up
travel speed and ideal for production welding. You will hear the pitch of the weld noise get higher, this
is normal. Welding at lower frequency will give reduced control of arc and a wider weld pool.
J. Down-Slope
Adjustable from 0 - 25 seconds, This allows you to gradually decrease the amperage
from main amps to end/final amps when using torch trigger operation.
Содержание SI-TIG-300
Страница 31: ... 28 9 TIG WELDING TORCH DETAILS ...
Страница 32: ... 29 ...
Страница 33: ... 30 10 ARGON FLOWMETER REGULATOR DETAILS ...
Страница 34: ... 31 ...