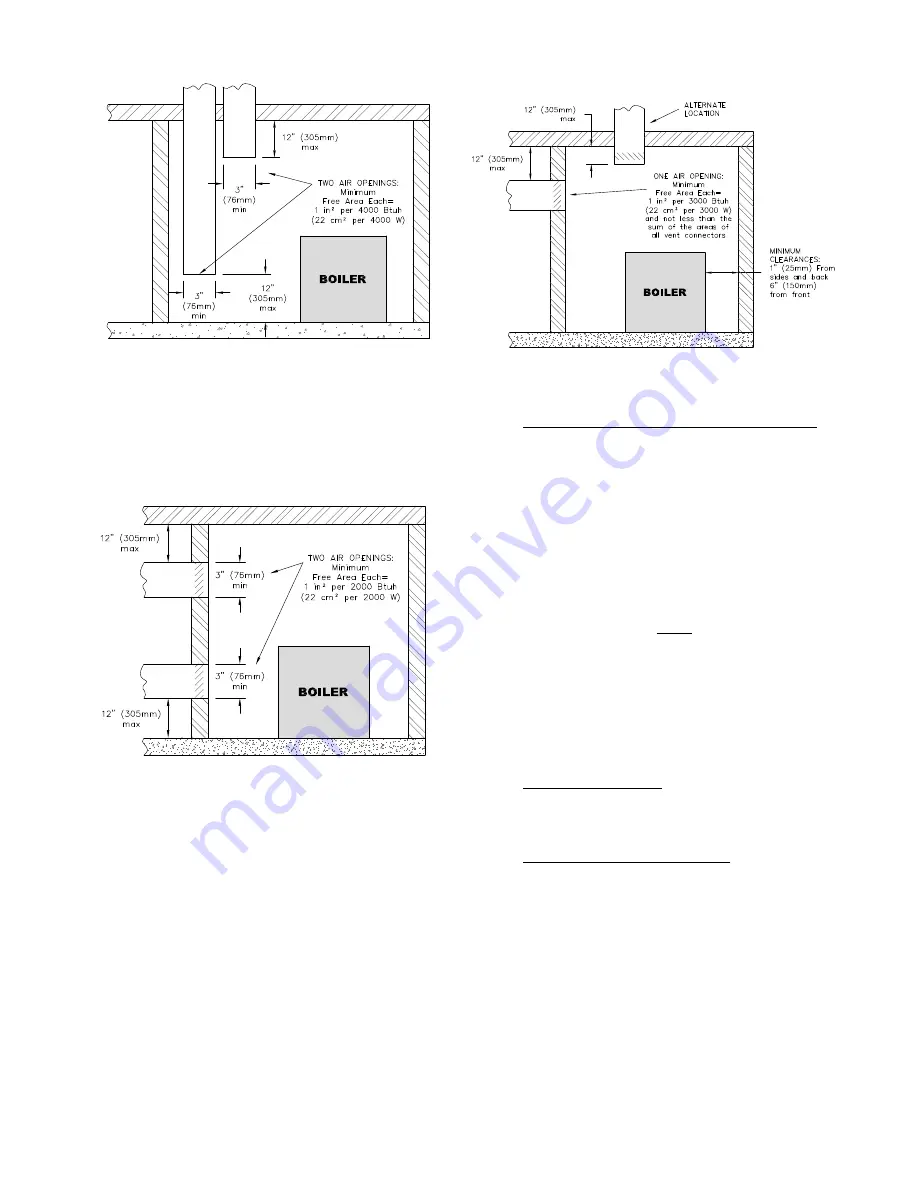
5
ii. Where communicating with the outdoors
through horizontal ducts, each opening shall
have a minimum free area of 1 in
2
per 2000
Btu/hr (22 cm
2
per 2000 W) of total rated
input for all appliances in the space. See
Figure 1.5.
b.
One Permanent Opening Method:
Provide
one permanent opening beginning within 12
inches (305 mm) of the top of the space. The
opening shall communicate directly with the
outdoors, communicate through a vertical or
horizontal duct, or communicate with a space
that freely communicates with the outdoors. The
opening shall have a minimum free area of 1 in
2
per 3000 Btu/hr of total rated input for all
appliances in the space and not less than the
sum of the cross-sectional areas of all vent
connectors in the space. The gas-fired equipment
shall have clearances of at least 1 inch (25 mm)
from the sides and back and 6 inches (150 mm)
from the front of the appliance. See Figure 1.6
for this arrangement.
5. Combination Indoor and Outdoor Combustion Air:
If the required volume of indoor air exceeds the
available indoor air volume, outdoor air openings or
ducts may be used to supplement the available
indoor air provided:
a. The size and location of the indoor openings
comply with Subsection 3.
b. The outdoor openings are to be located in
accordance with Subsection 4.
c. The size of the outdoor openings are to be sized
as follows:
where:
A
req
= minimum area of outdoor openings.
A
full
= full size of outdoor openings calculated
in accordance with Subsection 4.
V
avail
= available indoor air volume
V
req
= required indoor air volume
6. Engineered Installations: Engineered combustion air
installations shall provide an adequate supply of
combustion, ventilation, and dilution air and shall be
approved by the authority having jurisdiction.
7. Mechanical Combustion Air Supply:
a. In installations where all combustion air is
provided by a mechanical air supply system, the
combustion air shall be supplied from the
outdoors at the minimum rate of 0.35 ft
3
/min per
1000 Btu/hr (0.034 m
3
/min per 1000 W) of the
total rated input of all appliances in the space.
b. In installations where exhaust fans are installed,
additional air shall be provided to replace the
exhaust air.
INSTALLATION AND OPERATING INSTRUCTIONS
Figure 1.4:
Air Openings – All Air from Outdoors
through Vertical Ducts
Figure 1.5:
Air Openings – All Air from Outdoors
through Horizontal Ducts
Figure 1.6:
Air Openings – All Air from Outdoors
through One Opening
V
avail
1 –
V
req
A
req
=
A
full
x
Содержание GBX 105
Страница 18: ...18 Figure 6 4 Intermittent Ignition System Operating Sequence INSTALLATION AND OPERATING INSTRUCTIONS...
Страница 22: ...22 INSTALLATION AND OPERATING INSTRUCTIONS Figure 7 4 Operating Instructions...
Страница 29: ...29 Figure 8 1 Intermittent Ignition System Troubleshooting Sequence INSTALLATION AND OPERATING INSTRUCTIONS...
Страница 40: ...WESTCAST INC 260 NORTH ELM STREET WESTFIELD MA 01085 TEL 413 562 9631 FAX 413 562 3799 www smithboiler com...