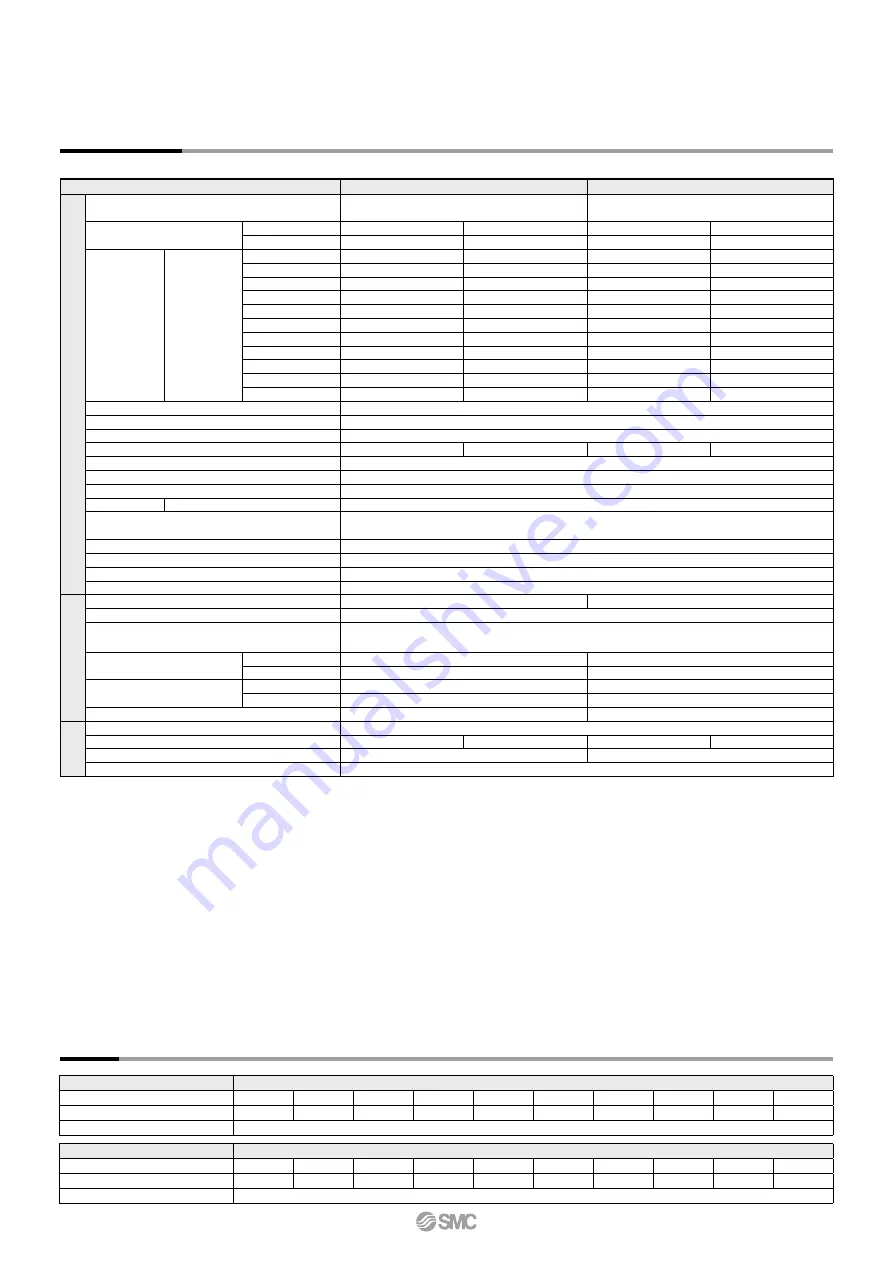
Specifications
11-LEJS40, 63 AC Servo Motor
Weight
Model
11-LEJS40S
2
6
11-LEJS63S
3
7
Actuator specifications
Stroke [mm]
Note 1)
200, 300, 400, 500, 600, 700, 800
900, 1000, 1200
300, 400, 500, 600, 700, 800, 900
1000, 1200, 1500
Work load [kg]
Note 2)
Horizontal
30
55
45
85
Vertical
5
10
10
20
Speed
Note 3)
[mm/s]
Stroke range
Up to 500
1200
600
1200
600
501 to 600
1050
520
1200
600
601 to 700
780
390
1200
600
701 to 800
600
300
930
460
801 to 900
480
240
740
370
901 to 1000
390
190
600
300
1001 to 1100
320
160
500
250
1101 to 1200
270
130
420
210
1201 to 1300
—
—
360
180
1301 to 1400
—
—
310
150
1401 to 1500
—
—
270
130
Max. acceleration/deceleration [mm/s
2
]
20,000 (Refer to page 15 for limit according to work load and duty ratio.)
Positioning repeatability [mm]
Note 4)
±
0.02
Lost motion [mm]
Note 5)
0.1 or less
Lead [mm]
16
8
20
10
Impact/Vibration resistance [m/s
2
]
Note 6)
50/20
Actuation type
Ball screw
Guide type
Linear guide
Grease
Ball screw/Linear guide portion
Low particle generation grease
Cleanliness class
Note 7)
ISO Class 4 (ISO14644-1)
Class 10 (Federal Standard 209D)
Allowable external force [N]
20
Operating temperature range [
°
C]
5 to 40
Operating humidity range [%RH]
90 or less (No condensation)
Regeneration option
May be required depending on speed and work load. (Refer to page 56.)
Electric specifications
Motor output [W]/Size [mm]
100/
40
200/
60
Motor type
AC servo motor (100/200 VAC)
Encoder
Motor type S2, S3: Incremental 17-bit encoder (Resolution: 131072 p/rev)
Motor type S6, S7: Absolute 18-bit encoder (Resolution: 262144 p/rev)
Power consumption [W]
Note 8)
Horizontal
65
80
Vertical
165
235
Standby power consumption
when operating [W]
Note 9)
Horizontal
2
2
Vertical
10
12
Max. instantaneous power consumption [W]
Note 10)
445
725
Loc
k unit
specifications
Type
Note 11)
Non-magnetizing lock
Holding force [N]
101
203
330
660
Power consumption [W] at 20
°
C
Note 12)
6.3
7.9
Rated voltage [V]
24 VDC
0
−10%
Model
11-LEJS40
Stroke [mm]
200
300
400
500
600
700
800
900
1000
1200
Product weight [kg]
5.6
6.4
7.1
7.9
8.7
9.4
10.2
11.0
11.7
13.3
Additional weight with lock [kg]
0.2 (Incremental encoder)/0.3 (Absolute encoder)
Model
11-LEJS63
Stroke [mm]
300
400
500
600
700
800
900
1000
1200
1500
Product weight [kg]
11.4
12.7
13.9
15.2
16.4
17.7
18.9
20.1
22.6
26.4
Additional weight with lock [kg]
0.4 (Incremental encoder)/0.7 (Absolute encoder)
31
Series
11-LEJS
Note 1) Consult with SMC for non-standard strokes as they are produced as
special orders.
Note 2) Refer to “Speed–Work Load Graph (Guide)” on page 12 for details.
Note 3) The allowable speed changes according to the stroke.
Note 4) Conforming to JIS B 6191-1999
Note 5) A reference value for correcting an error in reciprocal operation.
Note 6) Impact resistance: No malfunction occurred when the actuator was
tested with a drop tester in both an axial direction
and a perpendicular direction to the lead screw.
(Test was performed with the actuator in the ini-
tial state.)
Vibration resistance: No malfunction occurred in a test ranging be-
tween 45 to 2000 Hz. Test was performed in both
an axial direction and a perpendicular direction
to the lead screw. (Test was performed with the
actuator in the initial state.)
Note 7) The amount of particle generation changes according to the operat-
ing conditions and suction flow rate. Refer to the particle generation
characteristics for details.
Note 8) The power consumption (including the driver) is for when the actua-
tor is operating.
Note 9) The standby power consumption when operating (including the driv-
er) is for when the actuator is stopped in the set position during the
operation.
Note 10) The maximum instantaneous power consumption (including the
driver) is for when the actuator is operating. This value can be used
for the selection of the power supply.
Note 11) Only when motor option “With lock” is selected.
Note 12) For an actuator with lock, add the power consumption for the lock.
Note 13) Sensor magnet position is located in the table center.
For detailed dimensions, refer to “Auto Switch Mounting Position”
on page 43.
Note 14) Do not allow collisions at either end of the table traveling distance.
Additionally, when running the positioning operation, do not set
within 2 mm of both ends.
Note 15) For “Manufacture of Intermediate Strokes”, please contact SMC.
(LEJS40/Manufacturable stroke range: 200 to 1200 mm, LEJS63/
Manufacturable stroke range: 300 to 1500 mm)
A