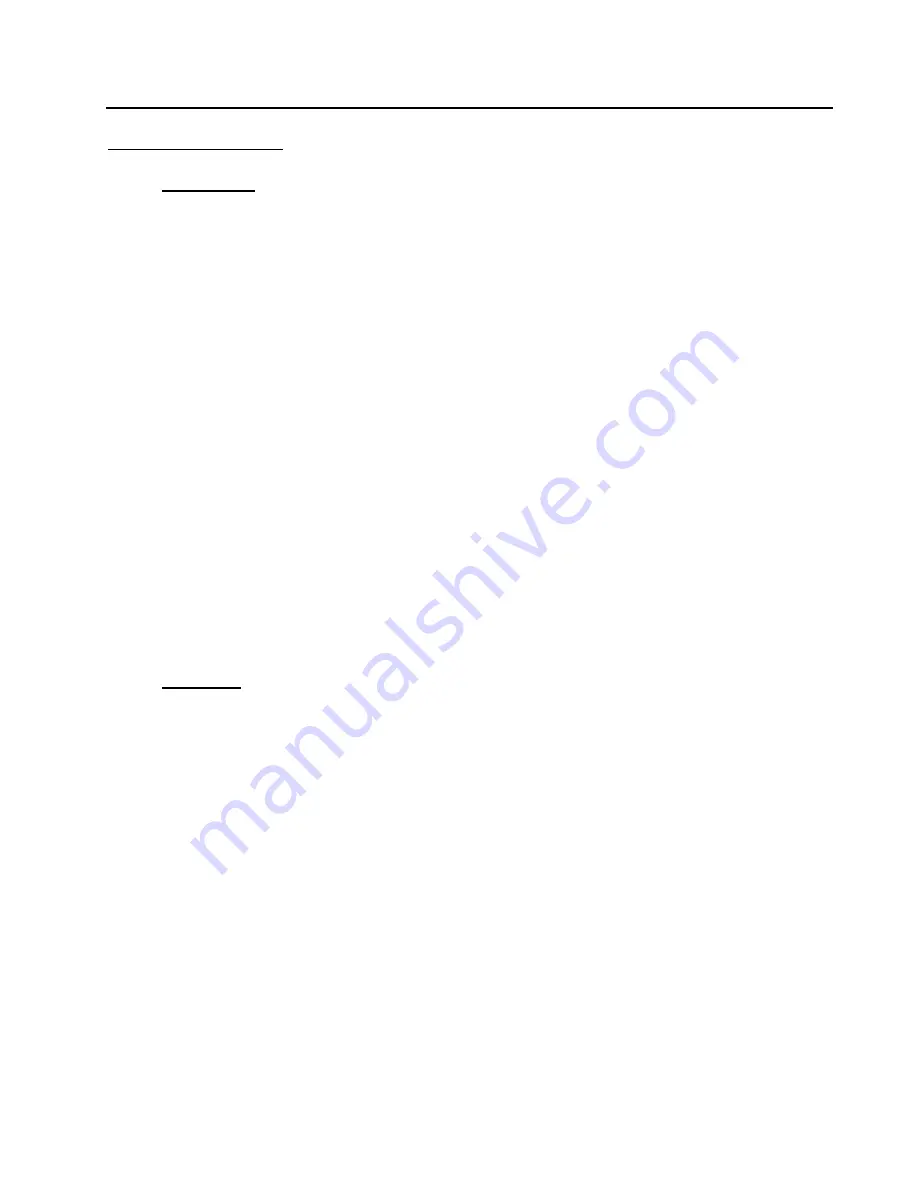
Smart Power Systems
®
A. C. MODULAR GENERATOR SYSTEM
Page 42 of 52
Hydraulic Problems:
1.
Cavitation:
Cavitation is caused by trying to pump more fluid than is available at the
pump
inlet due to system restrictions. Pump cavitation sounds like “marbles”
passing through the pump. Conditions frequently associated with cavitation are the
following:
a. Too many restrictive fittings such as elbows and reducers on the pump inlet
hose.
b. Tight bends or kinks in pump inlet hose and/or tubing.
c. Insufficient tray height above the pump, resulting in low head pressures.
d. Under sized pump inlet h
ose (minimum pump inlet hose size is 1”).
e. Excessive long inlet hose (may be corrected by using larger hose).
f. Cold hydraulic fluid.
g. Incorrect oil weight for climate
Finding the cause and correcting it should stop cavitation.
Install a 0-25 psig gauge in line between inlet hose fitting and pump inlet port.
Engage PTO. Operate genset with no load for twenty minutes to purge air out of
the system. Observe the pressure reading. The pressure should always be
positive. If the pressure is not positive, system repair/rework is required.
2.
Aeration:
Aeration results from air being drawn into the system
through leak paths or a
low fluid condition. Aeration makes a “growling” sound and produces visible
bubbles in the fluid stream and/or reservoir. Conditions frequently associated with
aeration are the following:
a. Air leaks in the pump inlet flow path.
b. Low fluid level allowing air to be drawn into the system.
Verify there are no air bubbles in the fluid by viewing inside the reservoir. If there
are air bubbles, check fluid level, tighten all fittings, and look for cracked fittings or
hose leaks on the pump inlet line. Replace any suspect parts and adjust fluid level.
After correcting any problems, again operate the generator twenty minutes to purge
air out of the hydraulic fluid. Note that any bubbles seen in the reservoir indicate
leakage in the pump inlet line.