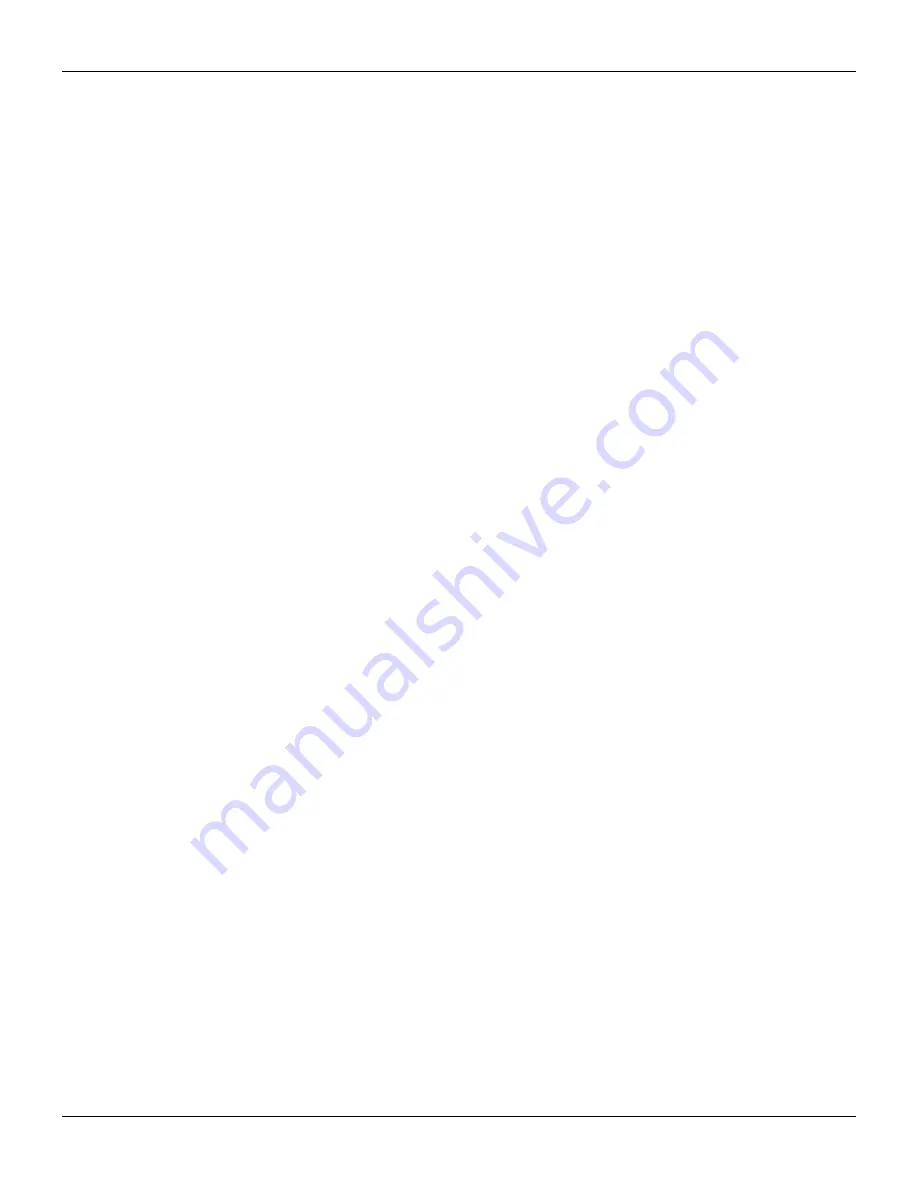
Operation
2.3
Power Supply Isolation
The sensor power supply is isolated from the main circuit by this module.
Display Controller
It receives the data from the CPU and actives the LCD segments. Also it actives the back plane
and the control signals for each segment.
Local Adjustment
Two switches that are magnetically activated. The magnetic tool without mechanical or electrical contact
can activate them.
FUNCTIONAL DESCRIPTION - SOFTWARE
Factory Characterization
Calculates the actual pressure from the capacitances and temperature readings obtained from the
sensor using the factory characterization data stored in the sensor EEPROM.
Digital Filter
The digital filter is a low pass filter with an adjustable time constant. It is used to smooth noisy signals.
The Damping value is the time required for the output reaching 63.2% for a step input of 100%.
Customer Characterization
The characterization TRIM points P1-P5 can be used to complement the transmitter's original
characterization.
Pressure Trim
Here the values obtained by Zero Pressure TRIM and Upper Pressure TRIM corrects the transmitter for
long term drift or the shift in zero or upper pressure reading due to installation or over pressure.
Ranging
Used to set the pressure values corresponding to the output 4 and 20 mA. In transmitter mode the
LOWER-VALUE is the point corresponding to 4 mA, and UPPER-VALUE is the point corresponding to
20 mA. In PID mode the LOWER-VALUE corresponds to MV = 0% and UPPER-VALUE corresponds
to MV = 100%.
Function
Depending on the application, the transmitter output or controller PV may have the following
characteristics according to the applied pressure:
Linear
(for pressure, differential pressure and level
measurement);
Square-root
(for flow measurement with differential pressure producers) and
Square-root
of the Third and Fifth power
(for flow measurements in open channels). The function is selected with
FUNCTION.
Customer Linearization
This block relates the output (4-20 mA or Process Variable) to the input (applied pressure) according to
a look-up table from 2 to 16 points. The output is calculated by the interpolation of these points. The
points are given in the function "TABLE POINTS" in percent of the range (X
i
) and in percent of the output
(Y
i
). It may be used to linearize, e.g., a level measurement to volume or mass. In flow measurement it
can be used to correct for varying Reynolds number.
Setpoint
Is the desired value in the process variable when the controller is activated. The operator in the
\CONTR\INDIC option adjusts it.
PID
First the error is calculated as SP-PV or PV-SP depending on which action (direct or reverse) it is
configured. Then the manipulated variable MV is calculated according to the type of PID algorythm.
Auto/Manual
The Auto/Manual mode is configured in CONTR/INDIC. With the PID in Manual, the MV can be adjusted
by the user in the range LOW LIMIT to HIGH LIMIT (adjustable by the user) in the CONTR/LIM-SEG
option. The POWER-ON option is used here to determine in which mode the controller should be upon
powering it on.
Limits
This block makes sure that the MV does not go beyond its minimum and maximum limits as established
by the HIGH-LIMIT and LOW-LIMIT. It also makes sure that the Rate-of-Change does not exceed the
value set in OUT-CHG/S.
Содержание ld301
Страница 14: ...LD301 Operation and Maintenance Instruction Manual 1 8...
Страница 18: ...LD301 manual de Instru es Opera o e manuten o 2 4 Fig 2 3 LD301 Software Block Diagram...
Страница 50: ...LD301 Operation and Maintenance Instruction Manual 4 16...
Страница 55: ...Maintenance Procedure 5 5 Fig 5 1 Exploded View...
Страница 62: ...LD301 Operation and Maintenance Instruction Manual 5 12...
Страница 70: ...APPENDIX A...