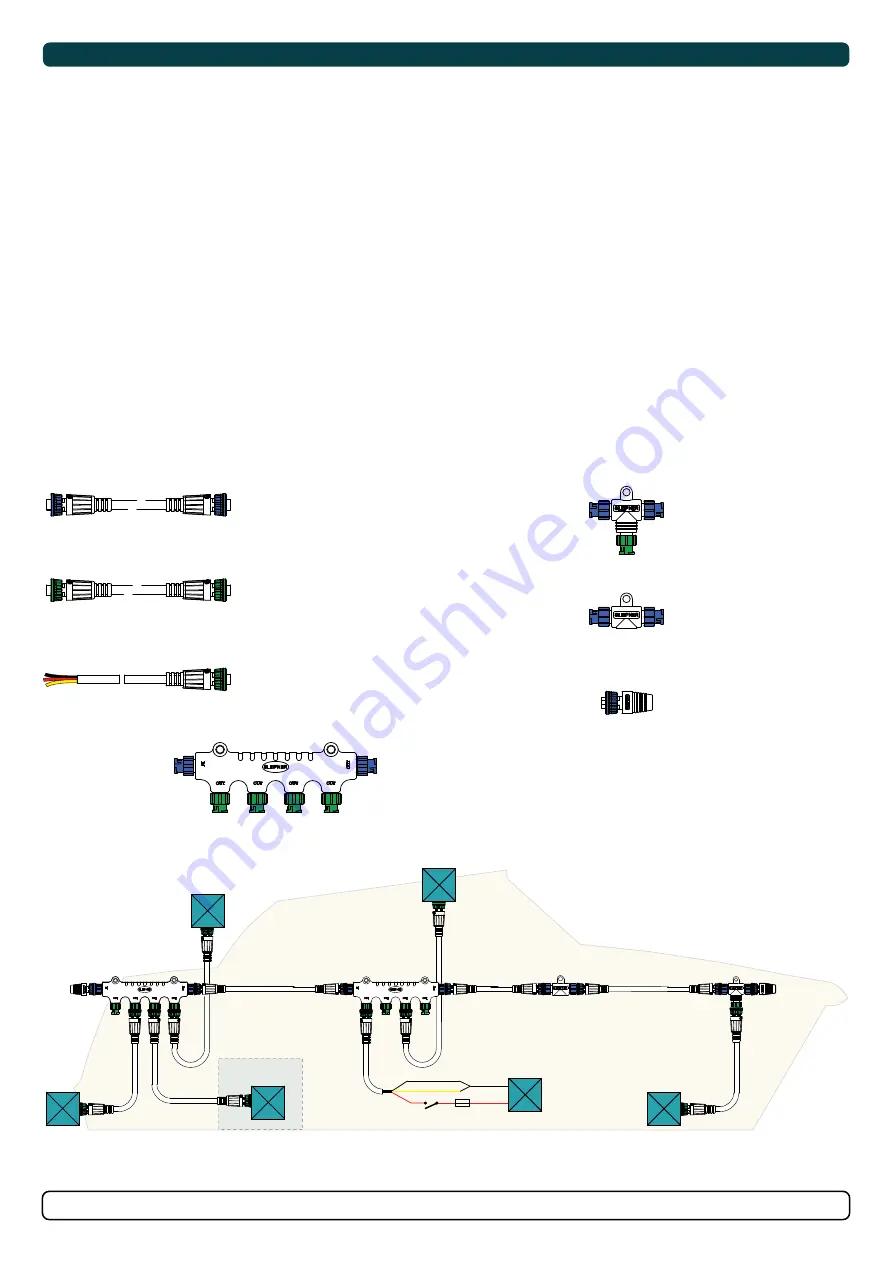
21
2713
20
2022
-
SEP 210
MG_0062
Technical Wiring Diagram
A1
A2
D2
NTC
Thruster motor
D1
1
2
3
4
5
6
7
8
To PPC
B+
To PPC
M-
Multi cable to PPC
grey
blue
white
red
pink
(Opt.)
8-Way connector
C
C
red or
red-brown
MC_0120
S-Link System Description
S-Link is a CAN-based control system used for communication between Sleipner products installed on a vessel. The system uses BACKBONE Cables
as a common power and communication bus with separate SPUR Cables to each connected unit. Units with low power consumption are powered
directly from the S-Link bus therefore one power cable must be connected to the BACKBONE Cable through a T-Connector.
Main advantages of S-Link system:
- Compact and waterproof plugs.
- BACKBONE and SPUR Cables have different colour coding and keying to ensure correct and easy installation. BACKBONE Cables have blue
connectors and SPUR Cables have green connectors.
- Different cable lengths and BACKBONE Extenders makes the system scalable and flexible to install.
Installation of S-Link cables:
Select appropriate cables to keep the length of BACKBONE- and SPUR Cables to a minimum. In case of planned installation with total BACKBONE
Cable length exceeding 100 meters please consult your local distributor. The S-Link cables should be installed to ensure sharp bend radius’s is
avoided. Locking mechanism on connectors must be fully closed. To ensure long lifetime, cables, T-Connectors and Extenders should not be
located so that they are permanently immersed in water or other fluids. It is also recommended to install cables such that water and condensation do
not run along the cables and into the connectors.
The POWER Cable should ideally be connected around the middle of the BACKBONE Cable to ensure an equal voltage drop at each end of the
BACKBONE Cable. The yellow and black wire in the POWER Cable shall be connected to GND and the red wire connected to +12VDC or +24VDC.
To reduce the risk of interference, avoid routing the S-Link cables close to equipment such as radio transmitters, antennas or high voltage cables. The
backbone must be terminated at each end with the END Terminator.
SPUR cables can be left unterminated to prepare for the installation of future additional equipment. In such cases, ensure to protect open connectors
from water and moisture to avoid corrosion in the connectors.
MG_0159
BACKBONE Cable
Forms the communication and power bus throughout
a vessel. Available in different standard lengths.
*Blue ends
*Blue ends
*Blue ends
*Blue ends
*Blue ends
*Blue ends
*Blue ends
*Blue ends
*Blue ends
*Green ends
*Green ends
*Green ends
*Green ends
*Green ends
SPUR Cable
Used to connect S-Link compliant products to the
backbone cable. One SPUR Cable must be used for
each connected component, with no exceptions.
Recommended to be as short as practically possible.
Available in different standard lengths.
POWER Cable
Required in all installations for connection of BACKBONE
Cable to a power supply. It shall not be more than one
POWER Cable in an installation.
4-Port T-Connector
The 4-PORT T-connector allows multiple SPUR Cables to be
connected. The 4-PORT T-connector comes with two sealing
caps to protect unused ports.
T-Connector
Used for connection of SPUR
or POWER Cable to the
BACKBONE Cable. One
T-Connector for each
connected cable.
BACKBONE Extender
Connects two BACKBONE
Cables to extend the length.
END Terminator
Must be one at each end of
the BACKBONE bus.
12/24V
GND
Switch
Optional
Fuse
2A
S-Link installation example
Spur
Power
T-Connector
End
Terminator
End
Terminator
Backbone Extender
Bow Thruster
Control Panel
Spur
Control Panel
Backbone
Backbone
Backbone
Spur
Spur
*For DC system
Spur
4 Port T-Connector
4 Port T-Connector
Stern Thruster
Automatic
Main switch
S-Link
Power Supply
Yellow
Red
Black
Содержание Pro DC SEP210
Страница 26: ...26 2713 20 2022 SEP 210 MC_0037 Notes...
Страница 27: ...27 2713 20 2022 SEP 210 MC_0037 Notes...