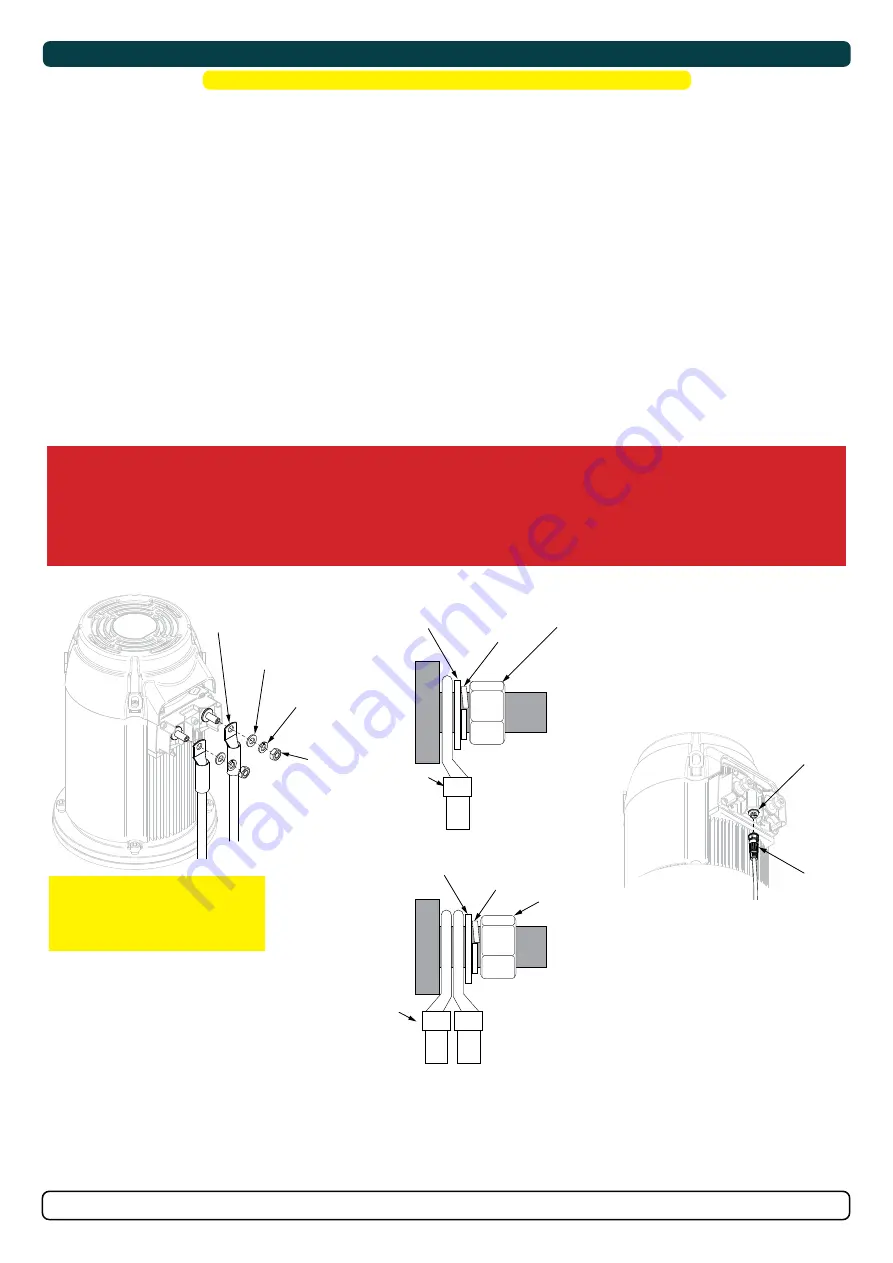
15
7241
5
2022
-
ERV130 & ERV170 & ERV210
MG_0587
Bolt tightening force (4x)
33 Nm (24 lb/ft)
Install the relevant motor and
other electronics according to
electrical instructions in the
manual
Motor to House Installation
1. Install the motor onto the motor bracket ensuring the couplings and the drive shafts have locked together. The motor must be installed with
the solenoid facing the control box.
(NB: depending on your coupling you may need to wiggle the motor into place. Ensure the couplings are
engaging correctly. Ensure the motor cable terminals are accessible for electrical installation later.)
2. Fasten the bolts holding the motor to the motor bracket with the above torque.
3. Check the drive shafts engage by rotating the propeller. It is required the propeller can rotate via hand power.
(NB: Rotating the propellers can be
hard because of the gear reduction and the motor.)
4. Apply the gear leg and propeller with anti-fouling designed for propellers. Do not apply to the propeller drive shaft, the anodes or the end of the
gear leg facing the propellers.
(NB: The motor must be covered to avoid dust from fabrication/ maintenance operation entering the motor or the solenoids. After fabrication
maintenance operations have ceased the cover must be removed before operating the thruster.)
MC_0068
!
Please refer to the graphic for special considerations relating to your model
!
MC_0143
Electrical Installation
WARNING
Check the following with the main switch is set to off :
After all electrical connections have been completed check with an ohm meter that there is no electrical connection between
1. electro-motor flange and the positive terminal on the motor
2. electro-motor flange and the battery negative terminal on the motor
If unsure contact skilled personnel.
1. Information of electrical table.
see next page
- All power cable lengths represent the total length of the combined (+) and (-) cables.
- Battery capacity is stated as minimum cold crank capacity, (CCA).
- Use slow blow rated fuses to hold stated Amp-Draw for min. 5 minutes.
- Consider the AMP hours (Ah) for your specifi c duty cycle.
2. Use appropriate sized cables and batteries with high cranking capacity to feed the thruster. The actual voltage at the motor while running the
thruster decides the motors output RPM and thrust. Use larger cables and stronger batteries for better results.
- See electrical specifi cations for advised minimum cables and batteries (CCA).
3. Install the main switch as close to the battery as possible and ensure the main positive lead can take loads without noticeable voltage drop.
- Ensure the main switch (battery isolator) can be turned off independently and manually when not on board or in emergencies.
- Ensure it is easily accessible and update instructions that this should be turned off like the boat’s other main switches.
It is advised to install a fuse in the positive lead for protection against short-circuiting.
- Ensure a slow type and appropriately sized to take the amperage draw for at least 5 minutes.
(NB: For Ignition Protected installations remember to use ignition protected fuses and switches if fi tted in areas that require this feature.
Ensure to follow your national regulations)
5. Cable lugs must have adequate electrical and mechanical isolation and fi tted with cable lug covers.
6. Fasten cables to the required torque.
!
Please refer to the graphic for special considerations relating to your model
!
MG_0523
End nut
End nut
S-Link cable
S-Link
Connector
(M10) Nut
Tighten to *max
13 Nm (9.59 lb/ft)
Spring
washer
Spring
washer
Washer
Washer
Lugs
Lug
IMPORTANT
Do NOT use washers between lugs,
this causes overheating and fire. Spring
washers must be placed in the outer
position before tightening the nut.
Lugs
End nut
Spring
washer
Washer
Multi-lug
configuration
Ensure lug faces
are back to back.
Single-lug
configuration
Ensure lug faces
are back to back.