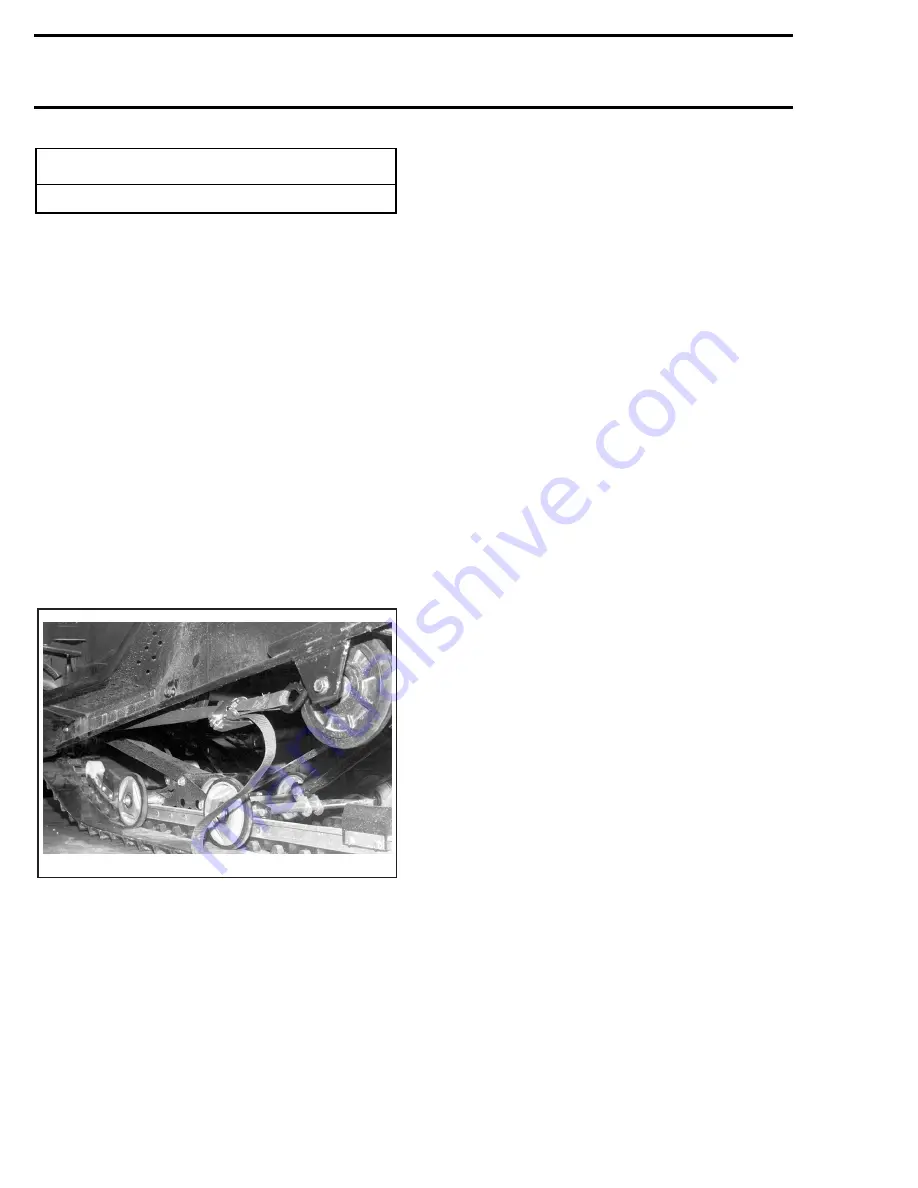
Section 07
REAR SUSPENSION
Subsection 04
(SKANDIC WT SUSPENSION)
07-04-4
Examine each shock for leaks. Extend and com-
press the piston several times over its entire
stroke then check that it moves smoothly and
with uniform resistance.
Pay attention to the following conditions that will
denote a faulty shock:
– A skip or a hang back when reversing stroke at
mid travel.
– Seizing or binding condition except at extreme
ends of stroke.
– Oil leakage.
– A gurgling noise, after completing one full com-
pression and extension stroke.
Renew if any fault is present.
INSTALLATION
Use a tie-down between front arm and spring axle
to ease installation of front arm screws.
-
CAUTION
Do not clamp directly on shock body.
A22F1FA
Содержание Formula 500 1998
Страница 1: ......
Страница 298: ...Section 07 REAR SUSPENSION Subsection 05 DRIVE AXLE 07 05 2 Skandic WT SWT WT LC A22D14S 13 6 9 3 2 5 4 FLAT RATE PARTS ...
Страница 358: ...SKANDIC WT SWT ANNEX 1 ...
Страница 359: ......
Страница 360: ......
Страница 361: ...SKANDIC WT LC ANNEX 2 ...
Страница 362: ......
Страница 363: ......
Страница 364: ...MX Z440 ANNEX 3 ...
Страница 365: ......
Страница 366: ......
Страница 367: ......
Страница 368: ......
Страница 369: ...MX Z 500 583 670 ANNEX 4 ...
Страница 370: ......
Страница 371: ......
Страница 372: ......
Страница 373: ......
Страница 374: ...FORMULA Z 583 670 ANNEX 5 ...
Страница 375: ......
Страница 376: ......
Страница 377: ......
Страница 378: ......
Страница 379: ......
Страница 380: ...FORMULA 500 DL 583 DL ANNEX 6 ...
Страница 381: ......
Страница 382: ......
Страница 383: ......
Страница 384: ......
Страница 385: ......
Страница 386: ...FORMULA 500 SUMMIT 500 583 670 ANNEX 7 ...
Страница 387: ......
Страница 388: ......
Страница 389: ......
Страница 390: ......
Страница 391: ......
Страница 392: ...GRAND TOURING 500 583 ANNEX 8 ...
Страница 393: ......
Страница 394: ......
Страница 395: ......
Страница 396: ......
Страница 397: ......
Страница 398: ......