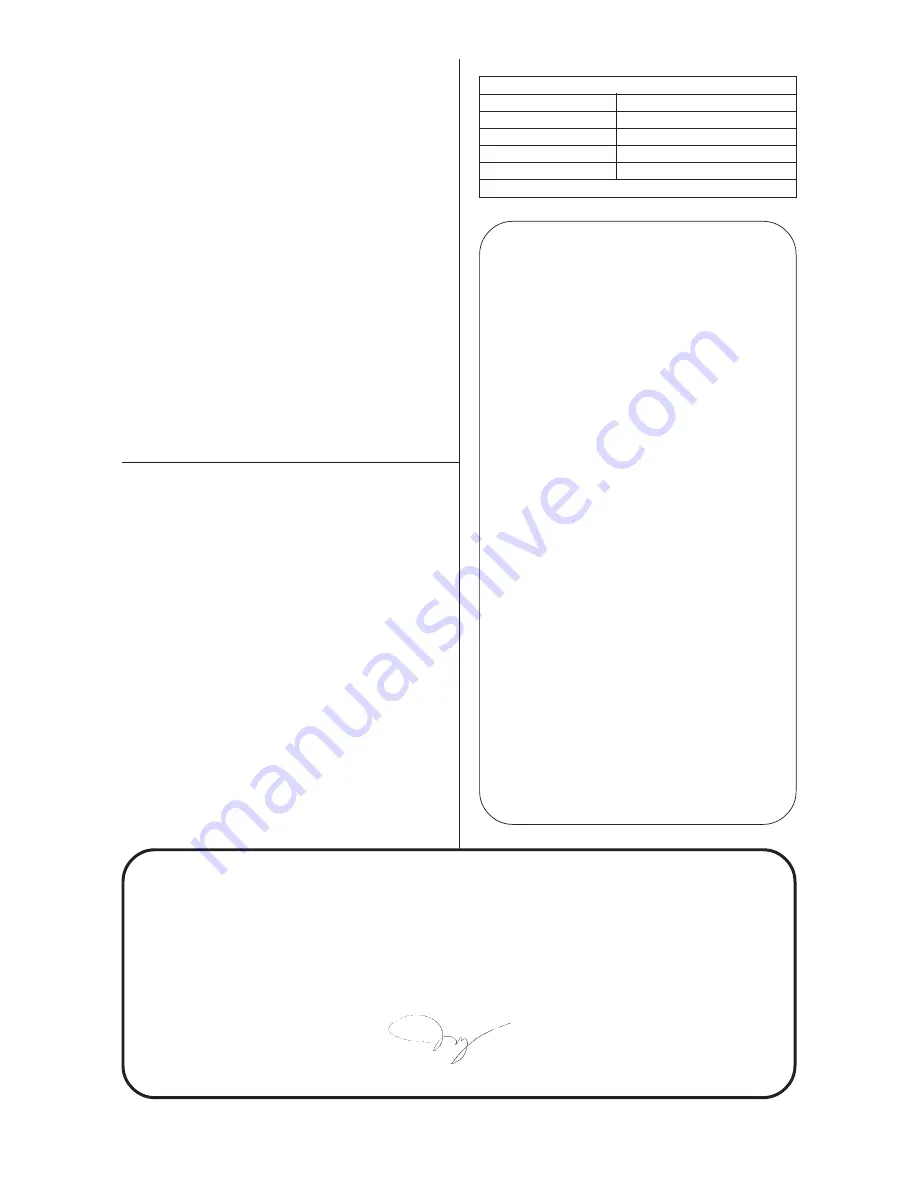
Page No 3
Declaration of Conformity
Sioux Tools Inc.
250 Snap-on Drive, P.O. Box 1596, Murphy, NC 28906, U.S.A.
declare under our sole responsibility that the product
Model 5350A/5350AP 1/2" Air Impact Wrenches, Serial Number
to which this declaration relates is in conformity with the following standard(s) or other normative document(s)
EN792 (Draft), EN292 Parts 1 & 2, ISO 8662 Parts 1 & 7, Pneurop PN8NTC1
following the provisions of
89/392/EEC as amended by 91/368/EEC & 93/44/EEC Directives
Mark Pezzoni (President, Power Tool Group)
_ _ _ _ _ _ _ _ _ _ _ _ _ _ _
_ _ _ _ _ _ _ _ _ _ _ _ _ _ _
_ _ _ _ _ _ _ _ _ _ _ _ _ _ _
Name and signature or equivalent marking of authorized person
Printed in Taiwan
Dismantling & Assembly Instructions
Disconnect tool from air supply.
Remove spring pin (8) by using a hammer with a small pin and pull
out trigger (10). Use a wrench to loosen air inlet bushing (7).
Remove valve spring (5), throttle valve (4), valve seat (3), and loosen
screw (2). Loosen cap screws (15) by using a screw driver.
Remove hammer case (37), cylinder (21), reverse bushing (18),
gasket (19). Loosen screw (12) and remove reverse switch (11).
Loosen retainer ring (22) with a vise and dismantle front end plate
(25), remove rotor (23) and rotor blades (24).
Remove hammer cage (30) from hammer case (37), remove
gasket (29), pull out hammer pins (32), turn around anvil (33 or 46)
and remove hammer dogs (31).
Reassembly
Clean and examine all parts for wear and replace any parts with
parts obtained from manufacturer or authorized distributor. All parts
must be dry. Check that all bearings run smoothly and reassemble
all tool parts in reverse order. Pump grease by using a mini grease
gun into the grease fitting. Connect tool to a suitable air
supply (90 psi preferred) and run tool slowly for 5 seconds to allow
the grease to circulate.
Notes
Soak rusted nuts in penetrating oil and break rust seal before
removing with impact wrench. If nut does not start to move in three to
five seconds use a larger size impact wrench. Do not use impact
wrench beyond rated capacity as this will drastically reduce tool life.
NOTE: Actual torque on a fastener is directly related to joint
hardness, tool speed, condition of socket and the time the tool is
allowed to impact.
Use the simplest possible tool-to-socket hook up. Every connection
absorbs energy and reduces power.
Forward/reverse operation is controlled by reverse switch (17)
located on back of housing (1). Turn reverse switch (17) to far right.
The tool is now in reverse mode. Turn switch left and tool is now in
forward mode. Ensure that the reverse switch is in the proper posi-
tion before starting tool.
The air regulator controls the speed of the tool and is located on the
back of housing (1). It is a 3-position regulator with “3” being the
highest setting and “1” the lowest setting.
The tool incorporates an air inlet bushing (7). Check periodically to
see if this is becoming blocked as blockage will reduce the speed
and power of the tool. To clean the air inlet bushing it is necessary to
remove the air inlet bushing (7) from motor housing (1).
For best results:
1) Always use the correct size impact type socket.
2) Use extra deep sockets in place of extension bars where
possible.
3) Do not use oversized, worn or cracked sockets.
4) Hold the wrench so the socket fits squarely on the fastener. Hold
the wrench firmly, but not too tightly, pressing forward slightly.
Operation Specification
Air Consumption
Max. Torque
Working Torque
Air Inlet Thread
Overall Length
3.92 cfm (28 scfm)
520 ft.lbs. (705 Nm)
100-450 ft.lbs. (135-610 Nm)
1/4-18NPT
6.69" (170 mm)
at 90 PSIG/6.2 bar
CE
Содержание 5350A
Страница 20: ...Page No 20...