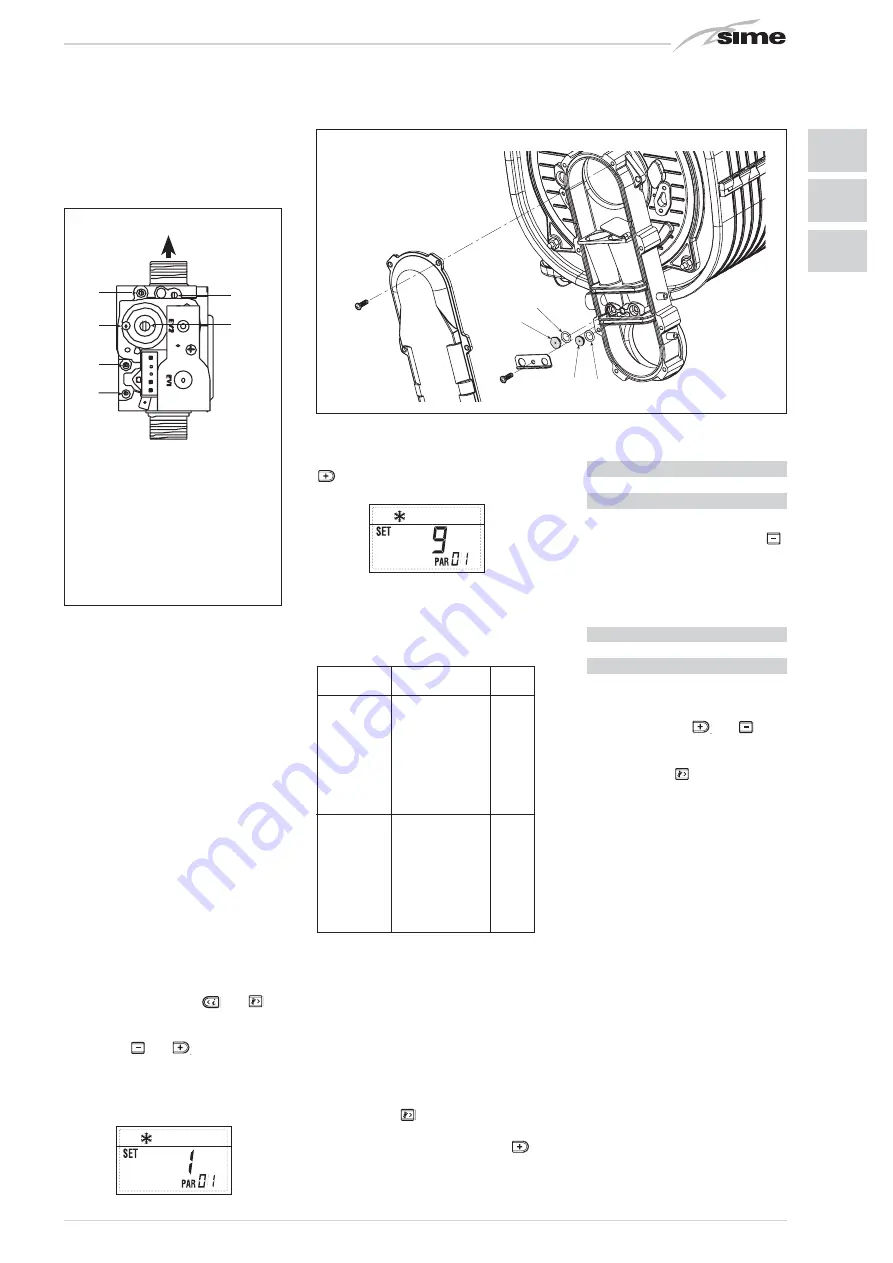
109
ES
PT
ENG
4.1
GAS VALVE (fig. 16)
The boiler is supplied as standard with a
gas valve, model SIT 848 SIGMA (fig. 16).
4.2
GAS CONVERSION (fig. 17)
This operation must be performed by
authorised personnel using original Sime
components.
To convert from natural gas to LPG or vice
versa, perform the following operations
– Close the gas cock.
– Replace the two differential nozzles (1-2)
and relative seal o-rings (3) with those
supplied in the transformation kit. The dif-
ference in the shape of the head of the
nozzles, avoid reversal during assembly.
– Apply the nameplate with the new gas
flow layout.
– Calibrate the maximum and minimum
pressures of the gas valve following the
instructions provided in paragraph 4.2.2.
4.2.1
New fuel configuration
For access to the installer's parameters,
press simultaneously keys
and
for
5 seconds (3 fig. 12).
The parameters will scroll up and down
with the keys
and
.
The display pane will show the values of the
parameter PAR 1. If the boiler is a
25
me t hane (G20) model, SET 1 will be
displayed:
To change the fuel to propane (G31), it is
necessary to set SET 9, by pressing the key
.
The standard display will automatically
return after 10 seconds.
The table below shows the SET settings to
enter when the type of gas fuel is changed.
4.2.2
Calibrating the gas valve
pressures
Measure the CO
2
values with a combustion
analyzer.
Sequence of operations:
1)
Press and hold the button down for a
few seconds
.
2)
Press the button for a few seconds
.
3)
Identify the CO
2
values at max. power by
adjusting the shutter (5 fig. 16):
4)
Press the button for a few seconds
.
5)
Identify the CO
2
values at min. power by
adjusting the OFF-SET regulation screw
(6 fig. 16):
6)
Press the buttons several times to
check the pressures
and
chan-
ge them if required.
7)
Press the button
once more to quit
the function.
4.4
DISASSEMBLING
THE SHELL (fig. 19)
To simplify maintenance operations on the
boiler, it is also possible to completely remo-
ve the shell, as shown in figure 19.
Turn the control panel to move it forward
and be able to access the internal compo-
nents of the boiler.
4.5
MAINTENANCE (fig. 20)
To guarantee functioning and efficiency of
the appliance, in respect of the legal provi-
sions in force, it must be regularly checked;
the frequency of the checks depends on
the type of appliance and the installation
and usage conditions.
In any case, it should be inspected at least
once a year by a qualified technician.
During maintenance operations, it is
important to verify that the drip-plate
Fig. 16
KEY
1
Upstream pressure intake
2
Intermediate pressure intake
3
Air signal inlet (VENT)
4
Downstream pressure intake
5
Shutter
6
OFF-SET
4
USE AND MAINTENANCE
MAX power
CO
2
(Methane)
CO
2
(Propane)
9,3 ±0,2
10,2 ±0,3
MIN power
CO
2
(Methane)
CO
2
(Propane)
8,4 ±0,2
10,0 ±0,3
1
2
3
4
5
6
1
2
3
3
Fig. 17
GAS MODELS
PAR 1
25 - 25 T
1
METHANE
30
2
(G 20)
35 - 35 T
3
25 - 25 T
9
PROPANE
30
10
(G 31)
35 - 35 T
11
Содержание MURELLE HM
Страница 1: ...MURELLE HM Fonderie SIME S p A Cod 6322745 01 2014 ES PT ENG...
Страница 2: ......
Страница 119: ......