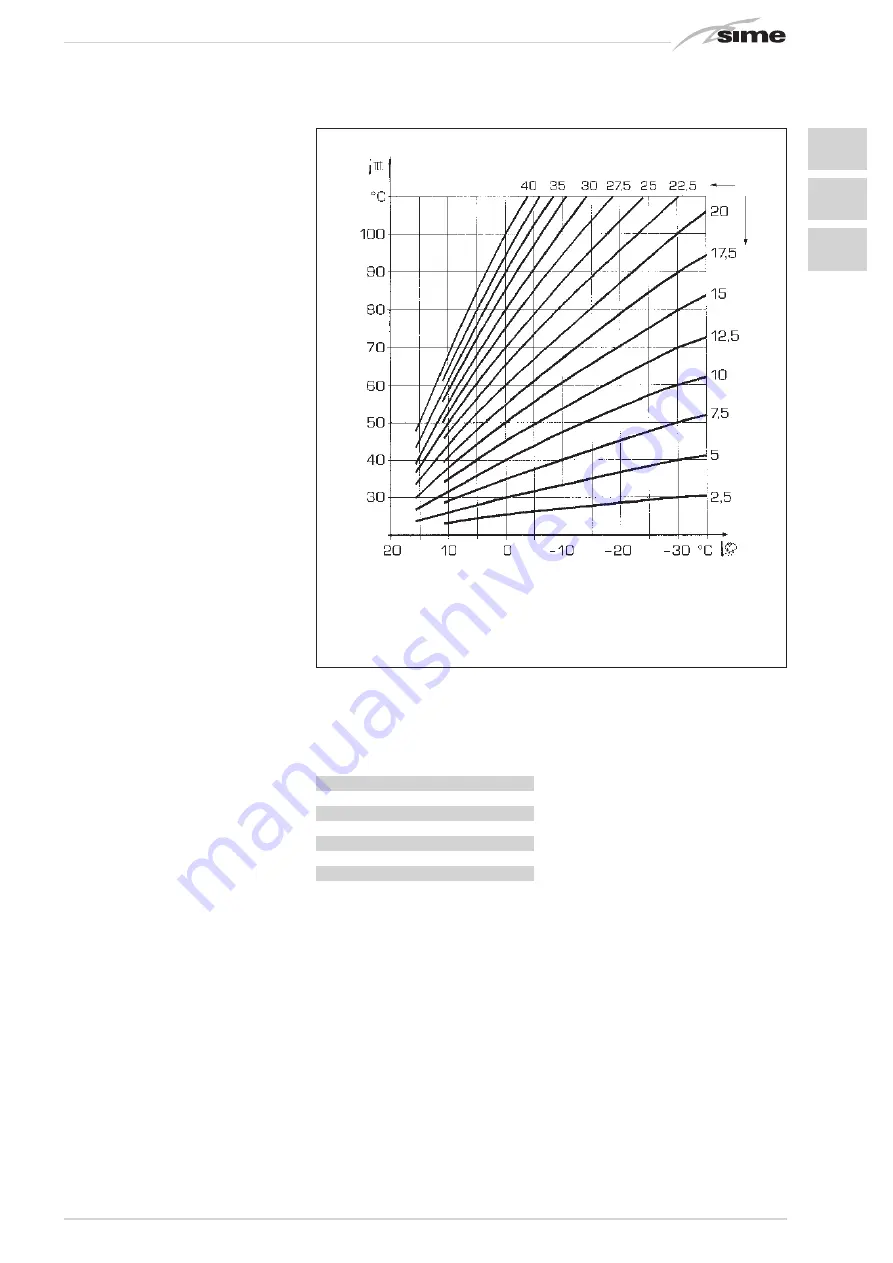
107
ES
PT
ENG
3.4
EXTERNAL SENSOR (fig. 13)
If there is an external sensor, the hea-
ting settings SET can be taken from the
climatic curves according to the external
temperature and, in any case, limited to
with the range values described in point
3.3 (parameters PAR 22 for zone 1, PAR 25
for zone 2 and PAR 28 for zone 3).
The climatic curve to be set can be selected
from a value of 3 and 40 (at step 1).
Increasing the steepness of the curves of
fig. 13 will increase the output temperatu-
re as the external temperature decreases.
3.5
CARD FUNCTIONING
The electronic card has the following fun-
ctions:
– Antifreeze protection of the heating and
sanitary water circuits (ICE).
– Ignition and flame detection system.
– Control panel setting for the power and
the gas for boiler functioning.
– Anti-block for the pump which is fed for
a few seconds after 24 hours of inactivi-
ty.
– Antifreeze protection for boilers with an
accumulation boiling unit.
– Chimney sweep function which can be
activated from the control panel.
– Temperature which can be shifted with
the external sensor connected.
It can be set from the control panel and
is active on the heating systems of both
circuit 1, circuit 2 and circuit 3.
– Management of 3 independent heating
circuit systems.
– Automatic regulation of the ignition
power and maximum heating.
Adjustments are managed automati-
cally by the electronic card to guaran-
tee maximum flexibility in use of the
system.
– Interface with the following electronic
systems: remote control SIME HOME
code 8092280/81, thermal regulator
RVS, connected to a management card
of a mixed zone ZONA MIX code 8092234,
card solar INSOL code 8092235 and to
board RS-485 for managing up to 8 boi-
lers in cascade or implement a commu-
nication type Modbus (slave RTU-RS485,
Reference Guide PI-MBUS-300 Rev. J)
cod. 8092243.
NOTE: If using CR 53 or RVS set para-
meter 10 to 2 or 3 (PAR 10 = 2 or 3).
3.6
TEMPERATURE
DETECTION SENSOR
Table 4
shows the resistance values of the
heating, DHW and exhaust fumes thermi-
stors
.
If the C.H. flow sensor (SM), C.H. return
sensor (SR) and the exhaust fumes sen-
sor (SF) is faulty or open circuit, the boi-
ler will not function on either heating or
DHW. If the D.H.W. sensor (SS) is faulty or
open circuit, the boiler will work without
modulation to the D.H.W. temperature.
3.7
ELECTRONIC IGNITION
Ignition and flame detection is controlled
by a single electrode on the burner which
guarantees reaction in the case of acci-
dental extinction or lack of gas within one
second.
3.7.1
Functioning cycle
Burner ignition occurs within max. 10
seconds after the opening of the gas valve.
Ignition failure with consequent activation
of block can be due to:
–
Lack of gas
The ignition electrode persists in
discharging for max. 10 seconds. If the
burner does not ignite, the anomaly is
signalled.
This can happen the first time the boiler
is switched on after a long period of
inactivity due to the presence of air in
the gas pipes
It can be caused by a closed gas tap or
by a broken valve coil (the interruption
does not allow for opening).
–
The electrode does not discharge.
In the boiler, only the opening of the gas
to the burner can be detected. After 10
seconds the anomaly is signalled. It can
be caused by an interruption in the elec-
trode wire or if it is incorrectly anchored
to the connection points. Or the electro-
de may be earthed or strongly worn: it
must be replaced.
Or the electronic card may be defective.
–
No flame detected
After start-up the electrode continues to
discharge even when the burner is on.
After 10 seconds, the discharge stops,
the burner is switched off and a fault is
generated.
This fault is sometimes caused by the
shorting of the electrode cable or by its
improper fixing to the connection points.
The electrode is connected to the earth
or badly worn and must be replaced.
TABLE 4 (SM - SR - SF - SS sensors)
Temperature (°C)
Resistance (Ω)
20
12.090
30
8.313
40
5.828
50
4.161
60
3.021
70
2.229
80
1.669
Fig. 13
ATTENTION: curves are calculated at an ambient temperature of
20°C. The user can act on the boiler controls to change the envi-
ronment set for which the bend has been calculated by ±5°C.