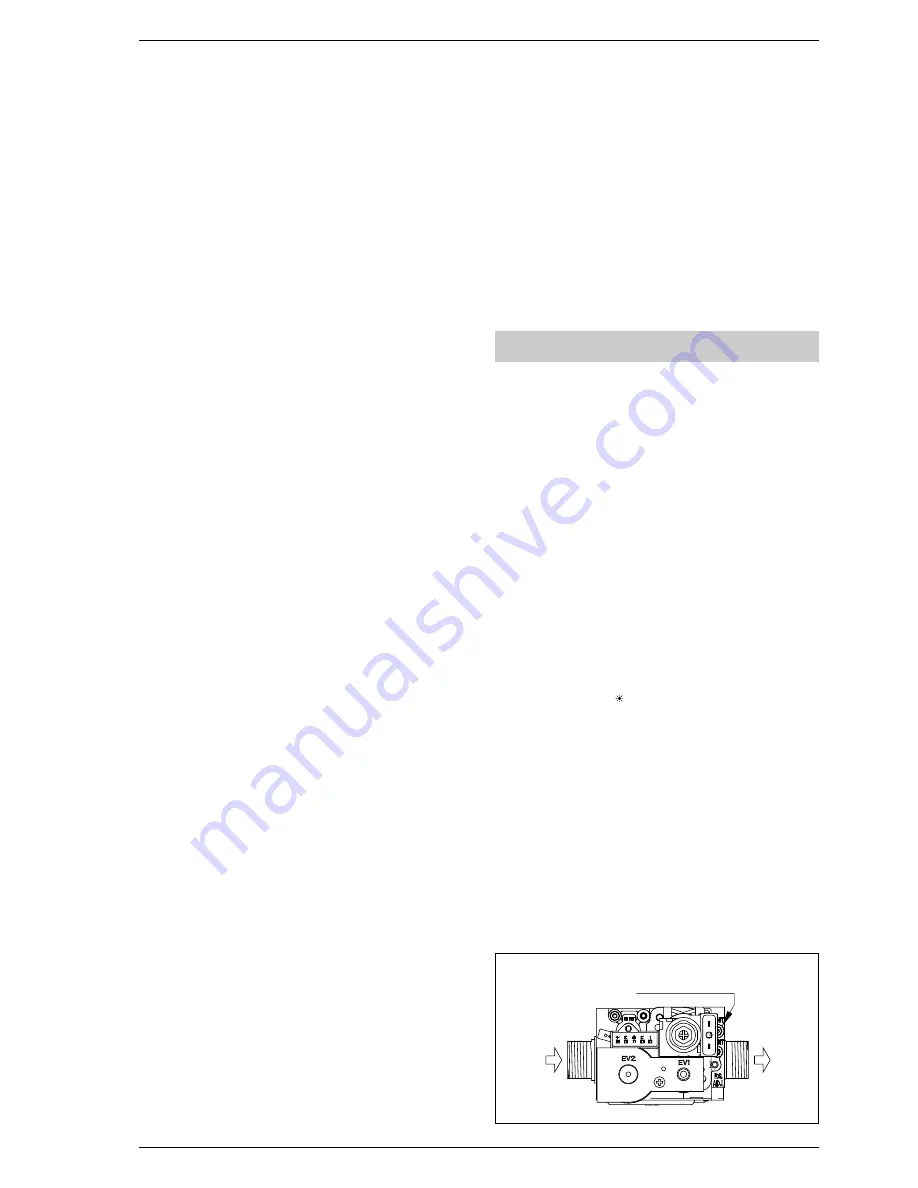
SIME SUPPORT THE BENCHMARK INITIATIVE
All relevant sections of the logbook must be filled in at the
time of installation and thereafter service information on the
back page of the logbook. Commissioning of the boiler is not
complete until the logbook is filled in.
Before commissioning the appliance, the whole gas installa-
tion including the meter MUST be purged and tested for gas
soundness in accordance with BS6891.
IMPORTANT: open all doors and windows, extinguish naked
lights, and DO NOT SMOKE whilst purging the gas line.
Before commencing the commissioning procedure, ensure
that the gas service cock is turned on, the electricity sup-
ply is isolated, and that the D.H.W. and C.H. isolation valves
are in the closed position.
4.1
FILLING THE WATER SYSTEM
– Open the C.H. flow and C.H. return valves (19 - 18 fig. 2).
– Loosen the automatic air vent cap (9 fig. 2).
– Open all radiator valves and system air vents. Fill the sys-
tem with water using one of the approved methods
described in section 2.9 to about 0.5 bar greater than
the system design pressure. Close all air vents. Do not
forget the one near the pump!
– Check the system for water soundness.
– Completely drain the appliance and heating system, thorough-
ly flush the system, and refill the system design pressure.
– Open the D.H.W. inlet valve, open any hot tap, clear of air
bubbles. Close hot tap.
4.2
COMMISSIONING THE BOILER
– Remove the screw and connect a pressure gauge to the
burner pressure test point on the gas valve (fig. 18).
– Ensure that the rotary switch on the facia panel is set to the
SUMMER position “
” (D.H.W. Only), turn the D.H.W. ther-
mostat to maximum (fully clockwise), and turn on the electri-
cal supply. Fully open any D.H.W. tap and the burner will light.
– Allow the boiler to run for at least 5 minutes and check
that the burner pressure is as stated in section 1.3. The
D.H.W. burner pressure is factory set and should not
require adjusting. If the burner pressure is low, check that
the appliance has not begun to modulate (this will occur if
the D.H.W. flow rate is low. If modulation is suspected, open
all D.H.W. taps to maximise flow and recheck burner pres-
sure). Check also the inlet pressure with the burner alight;
this should be 20 mbar (8 in.wg) +/- 2.5 mbar (1 in.wg) for
natural gas and 30 - 37 mbar (12 - 15 in.wg) +/- 2.5 mbar
(1 in.wg) for LPG. If it is necessary to adjust the D.H.W.
burner pressure the method is described in section 8.6.
14
to a drain. The discharge pipe should be a minimum of 15
mm copper, and should avoid sharp corners or upward
pipe runs where water may be retained.
3.10
WIRING INSTRUCTIONS
(Refer to sections 2.6 - 2.7 and fig. 17)
– Disconnect the electric power supply before performing
any work
.
– Remove the three screws (9) locking the control panel in place
and pull the panel forward until it can be tilted downward.
– To access the components of the electrical panel,
unscrew the four screws holding the protective guard in
place (6).
– To gain access to connector
“TA”
, remove the control
panel cover (7) and connect the room stat to the termi-
nals 10-11 after having removed the jumper.
The thermostat or timer-thermostat, recommended for
better room temperature control, must be class II as
specified by standard EN 60730.1 (clean contact).
– Carry out electrical system checks through a suitable test
meter: earth continuity, polarity, resistance to earth and
short circuit.
– Re-secure control box.
3.11
TIME-CLOCKINSTRUCTIONS
Setting the time
Turn the programming dial in clockwise direction to set the
read off the 24-hour dial opposite the marking.
Program setting
Press inwards the segments on the program disk corre-
sponding to the selected switching periods.
Function 1:
segment set outwards (C.H. “ON”)
Function 2:
segment set inwards (C.H. “OFF”)
Manual override
0 = “OFF” permanently
= automatic programmed operation
1 = “ON” permanently
4
COMMISSIONING AND TESTING
Programming characteristics
Cycle
Number of actions
Program time
Min. interval between
per cycle
per segment
two actions
24 hour
96
15 min.
15 min.
BURNER PRESSURE
TEST POINT
Fig. 18
Содержание Murelle 25 BF
Страница 24: ...Format C installation and servicing instructions...
Страница 53: ...26...