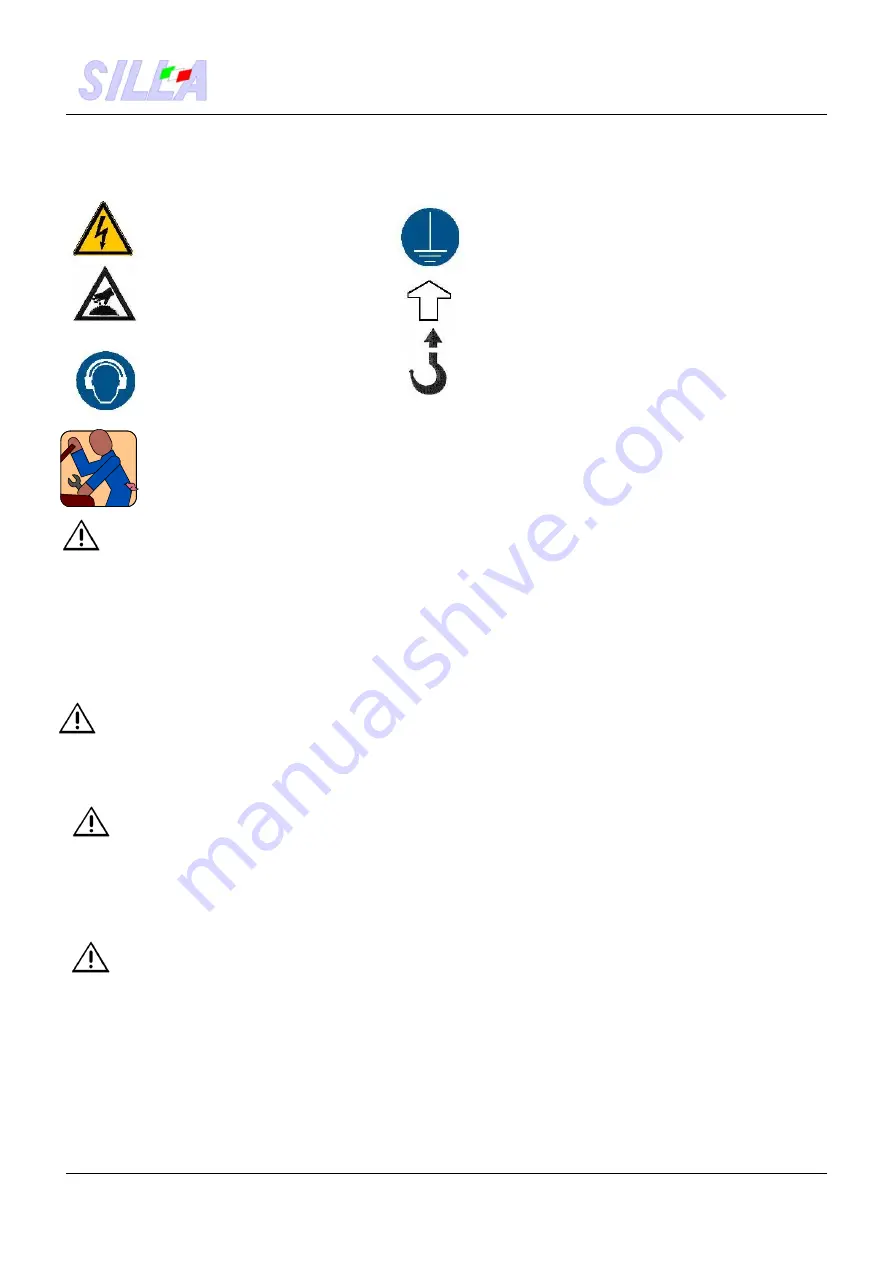
CONCRETE MIXER MOD.: PO 500
GB
Operating maintenance, spare parts manual Rèv. 3 del 12/10/18
Pagina 22 di 40
Never approach the moving and operating areas with your hands, arms or other parts of your body. Remove rubble with an
appropriate device (brush, wooden piece, etc.):
never use your hands!
Regular maintenance of the mechanical and electrical elements ensures a long machine life, best performances and a high
safety factor. Periodically check proper grounding, according to the standards in force. Before starting the machine, check
the inside and outside of the machine for possible tools or foreign matters and remove them.
Safety signs:
Caution electrocution hazard
Ground connection point
(on components of the electric system)
Caution moving parts
Direction of motor rotation
(next to the drum)
Wear ear protection
Anchorage / hoisting point
(ear muffs or plugs)
(On the machine there are instructions about residual hazards, follow these instructions.)
8.
MAINTENANCE
The machine does not require any particular maintenance work.
The technical solutions and the components installed on the machine reduce the maintenance works at the
minimum. However, we recommend to carry out a series of operations, which aim at ensuring safety, liability
and efficiency of the machine for a long period of time.
Before performing maintenance work, switch off and disconnect the machine from the power supply
(main switch). During maintenance work, place a special sign on the electric panel and on the machine to
highlight this status. Never make any modifications to the machine.
Use the protective equipment during maintenance work: work gloves, safety shoes, masks, and goggles.
For a right use and maintenance of the diesel engine, please follow the directions of the attached manual, by the
engine manufacturer.
8.1
Preventive (routine) maintenances
To be carried out every day at the end of the work:
Clean the work areas, the drum and the operating mechanisms. Blow away the dust on the machine and on the motor
protection grating with compressed air. Remove any deposits from the work and support surfaces.
Check the supply cable and make sure that it is undamaged.
Periodically check the hydraulic oil level, the belts and replace them, if necessary.
Oil is a special waste and must be disposed of according to the laws in force.
Clean the ground and remove any rubble.
To be carried out weekly:
Check locking of the mechanical components. Check protections and ensure their good operation, replace if necessary.
Check the oil level of the reducer of the scraper shovel , if necessary fill up with SAE 150 oil.
Periodically lubricate the rotation joint of the bucket, gear and pinion and arm support.
Lubricate the overturning system with rack piston with a viscous grease.
Caution !!! Before oiling or lubricating the concrete mixer, disconnect the machine.
Check the driving belts.
To be carried out every month:
Check locking of the mechanical components. Grease and oil all the joints exposed to seizure and grease the special
lubricators placed on the machine. Replace after the first 200 hours and then every 500 hours the hydraulic oil in the
tank/unit, use oil type Agip OSO 68. For replacement put a container (with a capacity of minimum 15 litres) under the tank.
Switch off the machine, as soon as the oil is cold, remove the cap and let the oil flow down into the container. Reposition the
cap and fill with the new oil. When changing the oil, change the filter, too.
Oil is a special waste and must be disposed of according to the laws in force.
Check the electric safety devices.
Check operation and locking of the mechanical safety devices.
8.2
Corrective maintenance
Other corrective maintenance work (special/repairs) must be done by the authorised technical personnel. In case of corrective
maintenance work like replacement of components, repair, etc. stop the machine and disconnect it from the power supply.