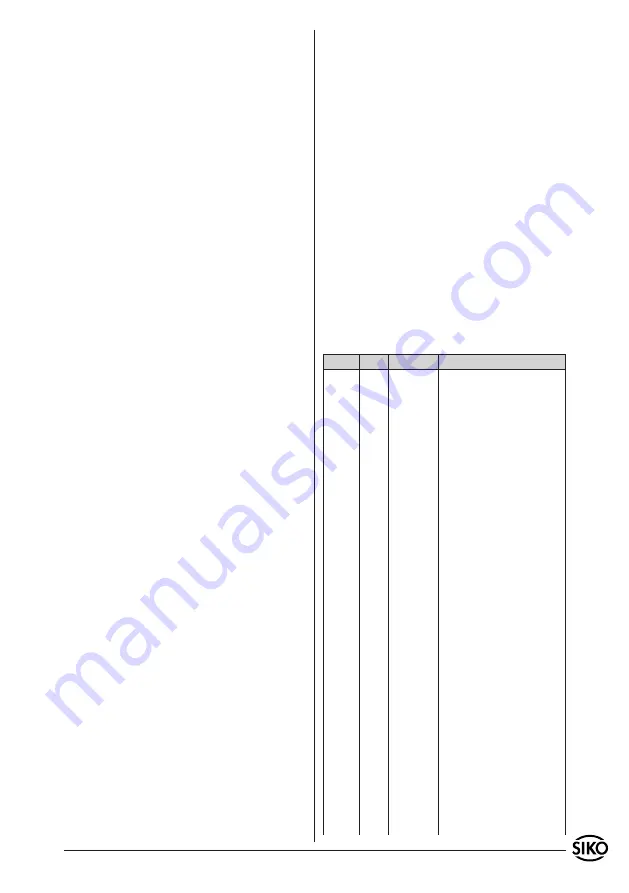
MBA1000
Datum 26.08.2008
Art.Nr. 79828
Änd. Stand 318/08
11
5.3 Sensor's SSI-interface
MSA1000's SSI-interface allows a synchronuous out-
put of the position value. Its data format comprises
a width of 24 bit which are either issued as Gray or
binary codes (see chapter 7) and right-aligned. All
following bits (25, 26...) are issued as "0".
Data signals correspond to RS422. Cycle inputs are
opto-decoupled and also correspond to RS422. Ty-
pical SSI monoflop time is . 20...25µs which gives
a min. cycle rate of 62,5kHz.
Please note that the possible max. cycle rate and
data integrity mainly depend on the length of the
connection line. The following standard values can
be given:
line length 2m
max. cycle rate:
1 MHz
line length 10m
max. cycle rate:
800 kHz
line length 100m
max. cycle rate:
250 kHz
line length 200m
max. cycle rate:
125 kHz
5.4 Sensor in bus operation
Two different protocols are implemented in the
MSA1000 firmware.
The differentiation between the "service mode"
and the "SIKONETZ3" protocol is effected via the
wiring of the configuration input on "pin L" of the
connector.
After switching on, the RS485 interface is set to
"service mode" as long as the configuration input
"pin L" is not wired. The device address required
for subsequent bus operation (SIKONETZ 3) can
only be changed in this mode (default address
01). After switching on the sensor, the program-
ming tool "demo1000.exe" must be started and
the displayed sensor paraqmeters be checked. The
software version should be 1.01 or better. Using
function key "F5", the sensor address (01...31)
can be entered and shown in the window that
is dis-played. The address is then automatically
stored in the sensor and is retained after swit-
ching off the power supply.
The configuration input "pin L" must be put to
GND whenever the sensor is used during bus ope-
ration. The input is queried during startup, and in
this case the RS485 protocol is set to SIKONETZ3.
6. Trouble shooting
Below there are some typical errors which may oc-
cur during installation and operation:
Sensor not or incorrectly connected (for pin
connection see chapter 4).
Tolerance for the gap between magnetic sensor and
magnetic strip not observed over the total travel
•
•
distance. Sensor touches strip (see chapter 7).
Cable squeezed / interrupted / cut by sharp
edges.
Sensor’s active side not mounted towards the
magnetic strip (see fig. 8).
Sensor and magnetic strip have been incorrectly
aligned (see chapter 1).
Magnetic fields near the measuring surface distort
the measuring values. If required, pro-vide for
adequate screening.
Wrong measuring values due to EMC interferences
(see chapter 4).
7. List of commands / service mode
Parameters: 19200 Baud, no parity, 8 bit, 1 stop
bit, no handshake
Data code: ASCII / Hexadecimal
Value range: 2/3 Byte: 0...65535 / 0...± 2
23
All replies which are confirmed by ">" end with
"CR" (Dez 13)."
Com.
Length Reply
Description
Ax
Send unit type/software version
2/9 "xxxxxxx>" x=0: hardware version
2/10 "xxxxxxxx>" x=1: software version
B
1/10 "±xxxxxxx>" Send absolute value (without cor-
rection values)
Ey
2/10 "±xxxxxxx>" Issue a 3-byte value
y=address (0...4)
y=1:position value
y=2:zero position value
y=3:calibration value
y=4:offset value
±xxxxxxx=dec. value
Fy±xxxxxx
9/2 ">"
Enter 3-Byte value
y=address (2...4)
y=2:zero position value (default=0)
y=3:calibration value (default=0)
y=4:offset value (default=0)
±xxxxxxx=dec. value
K
1/0 ""
Software reset
L
1/2 ">"
zero position value (calibration)
Nx
2/2 ">"
enter SSI output code
x=0: Gray code (default)
x=1: binary code
Qxx
3/2 ">"
enter device address (for SIKO-
NETZ 3 protocol)
xx= 01...31
R
1/4 "xx>"
output device address
xx= address
Sxxxxx
6/2 ">"
restore default programming
x= 11100 (s_befehl)
zero point/calibration/offset va-
lue =0
count. direct.= positive
output code= Gray
device address = 01
Tx
2/2 ">"
enter counting direction
x=0: positive count. direction (default)
x=1: negative count. dirction
•
•
•
•
•