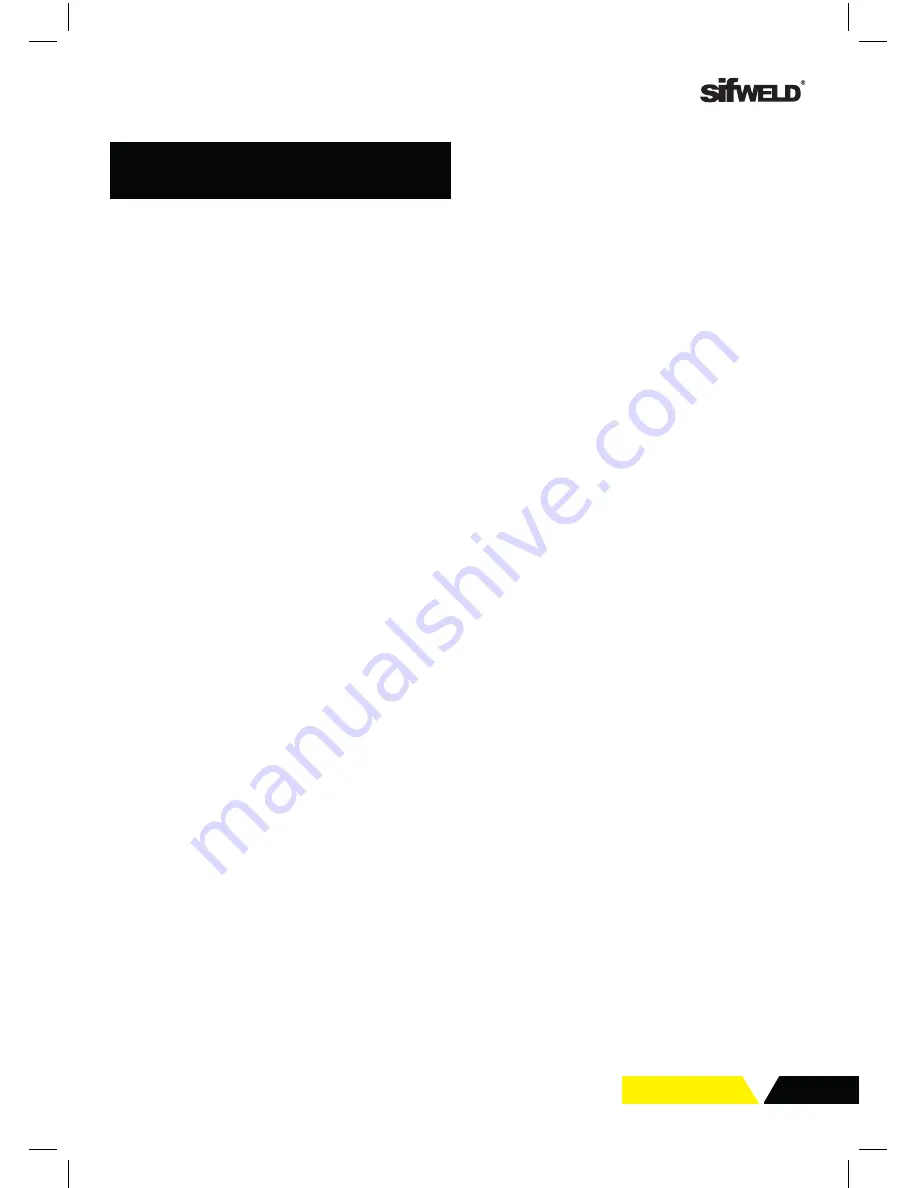
Safety Guidelines
These general safety guides cover both arc welding machines and plasma cutting machines unless
otherwise noted. The equipment must only be used for the purpose it was designed for. Using it in any
other way could result in damage or injury and in breach of the safety rules. Only suitably trained and
competent persons should use the equipment. Operators should respect the safety of other persons.
Prevention against electric shock
The equipment should be installed by a qualified person and in accordance with current standards in
operation. It is the user’s responsibility to ensure that the equipment is connected to a suitable power
supply. Consult with your utility supplier if required. If earth grounding of the work piece is required,
ground it directly with a separate cable. Do not use the equipment with the covers removed. Do not
touch live electrical parts or parts which are electrically charged. Turn off all equipment when not in use.
Cables (both primary supply and welding) should be regularly checked for damage and overheating.
Do not use worn, damaged, under sized or poorly jointed cables. Ensure that you wear the correct
protective clothing, gloves, head and eye protection. Insulate yourself from work and ground using
dry insulating mats or covers big enough to prevent any physical contact with the work ground. Never
touch the electrode if you are in contact with the work ground, or another electrode from a different
machine.
Do not wrap cables over your body. Ensure that you take additional safety precautions when you are
welding in electrically hazardous conditions such as damp environments, wearing wet clothing, and
metal structures. Try to avoid welding in cramped or restricted positions. Ensure that the equipment
is well maintained. Repair or replace damaged or defective parts immediately. Carry out any regular
maintenance in accordance with the manufacturer’s instructions.
Safety against fumes and welding gases
Locate the equipment in a well-ventilated position. Keep your head out of the fumes. Do not breathe
the fumes. Ensure the welding zone is in a well-ventilated area. If this is not possible, provision should
be made for suitable fume extraction. If ventilation is poor, wear an approved respirator. Read and
understand the Material Safety Data Sheets (MSDS’s) and the manufacturer’s instructions for metals,
consumable, coatings, cleaners, and de-greasers. Do not weld in locations near any de-greasing,
cleaning, or spraying operations. Be aware that heat and rays of the arc can react with vapours to form
highly toxic and irritating gases. Do not weld on coated metals, unless the coating is removed from the
weld area, the area is well ventilated, and while wearing an air-supplied respirator. The coatings on many
metals can give off toxic fumes if welded.
Prevention against burns and radiation
Arc rays from the welding process produce intense, visible and invisible (ultraviolet and infrared) rays
that can burn eyes and skin. Wear an approved welding helmet fitted with a proper shade of filter lens
to protect your face and eyes when welding or watching. Wear approved safety glasses with side shields
under your helmet. Never use broken or faulty welding helmets. Always ensure there are adequate
protective screens or barriers to protect others from flash, glare and sparks from the welding area. Ensure
that there are adequate warnings that welding or cutting is taking place.
3
TXP1P40