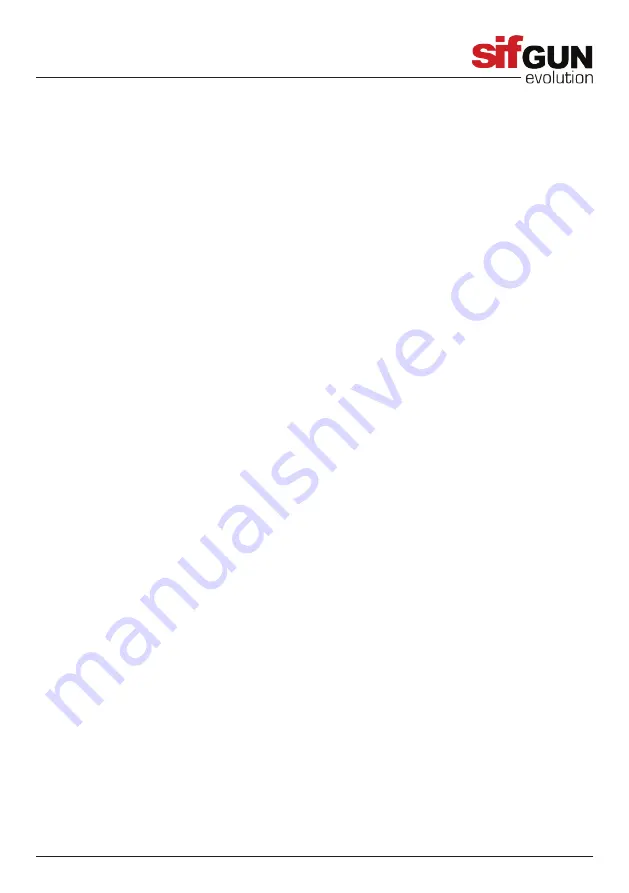
www.sifweld.com
9
5.2 Insertion of the liner
From the EURO-connector, insert the liner into the torch assembly until it sticks out of the torch
head. Close the wire feeder protection and turn on the power supply. Press the ‘inch’ button of the
wire feeder until the wire electrode emerges from the contact tip of the torch head.
Attention!
The wire electrode feed out can cause bodily injuries! When activating the trigger,
electric tension may occur. If the torch head touches conducting materials, welding may be
activated unintentionally
Wire feed rate may be adjusted by using the potentiometer of the power supply. When changing
the wire electrode diameter, make sure to change the contact tip as well.
5.3 Connection of the torch assembly (water-cooled torches)
Make sure that the minimum quantity of cooling liquid for the cooler is adhered to.
Attach the blue hose of the Euro-Connector to the output of the cooling system and the red hose
to the cooling system return.
Make sure to follow the instructions regarding cooling liquid as indicated by the manufacturer of
the power source.
Bleed the cooling circuit before the first use of the torch assembly.
Содержание EXTEVOMT1504
Страница 16: ...www sifweld com 16 ...