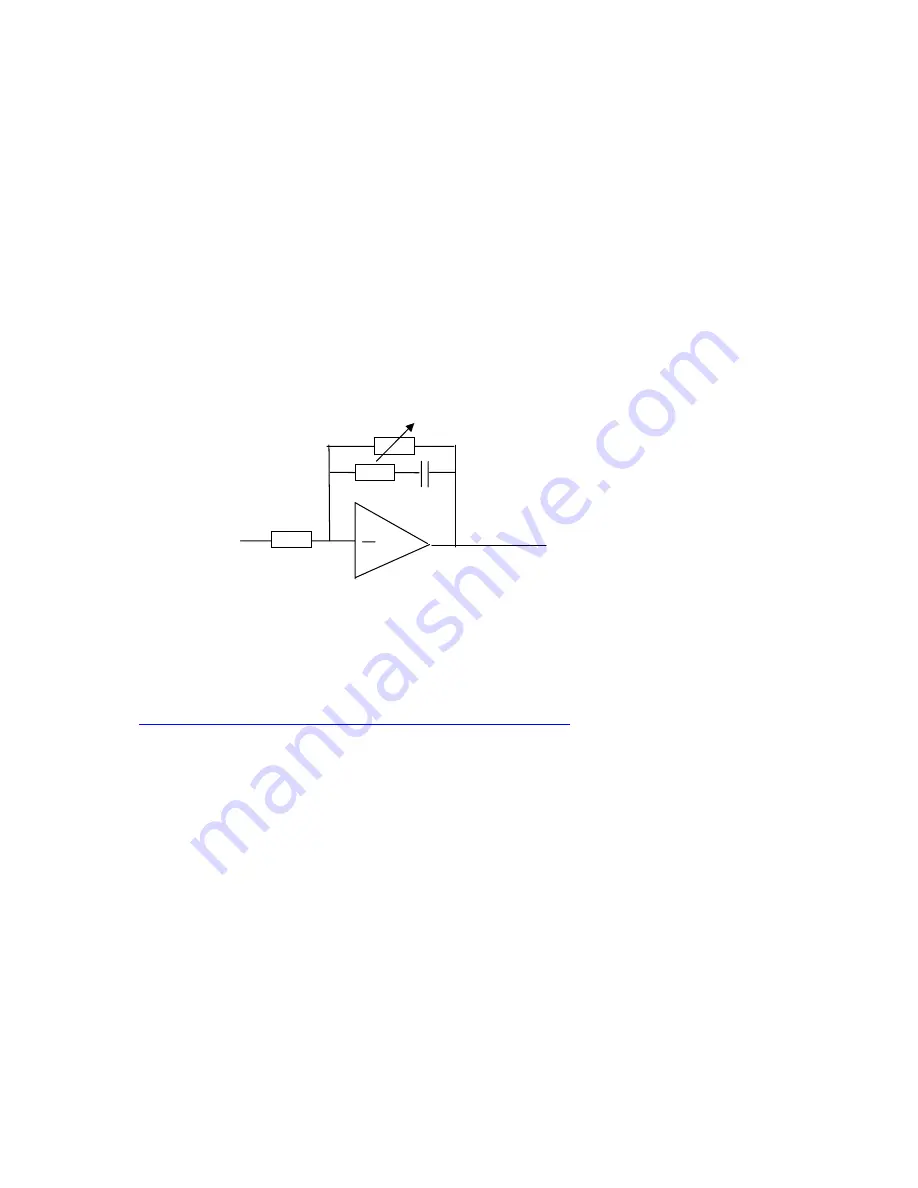
74
Load sharing via the droop function of the speed controller
A typical application example for this are roller conveyer drives for conveying material. The
speed controllers of the 6RA80 are given the same speed setpoint (master setpoint), so that
the motors turn at the same speed in principle. However, the speed controller has P-
feedback in addition to the PI characteristic. As the controller output variable (torque
setpoint) increases, this causes via this P-feedback a subtraction variable in the speed
setpoint channel, which in turn causes the speed actual value to collapse at a higher load
torque, which in turn automatically causes a reduction in the torque output. This results in an
even distribution of the load over multiple drives in which this droop function is parameterized
without any load sharing control. No further connections between the various devices are
required except for the common speed setpoint.
No Option is required for this droop function.
Analog circuit diagram of the droop function:
Axial winder
There are several ways of implementing an axial winder
in SINAMICS DCM
1) Implementation using the DCC on the CUD; Application available
http://support.automation.siemens.com/WW/view/de/47627620
2) Implementation by means of SIMOTION
In the majority of cases 1) Implementation using the DCC on the CUD is sufficient as well as
being the lowest-cost solution.
An axial winder characterized that fact that the diameter of the wound material varies as
winding progresses.
There are various methods of implementating the winding function, such as indirect tension
control, direct tension control, dancer roll control and v-constant control. One of these
methods is used both for taking up and paying out the material.
The drive is given the web velocity v as the setpoint. The diameter D is calculated by the
formula n * D = v. This diameter is used to convert the web velocity setpoint to a speed
setpoint to obtain the motor speed n as a function of D. The speed controller then receives a
correction setpoint via the tension controller (for dancer control or v-constant control) or it is
overdriven to control the tension via the torque limitation (for direct and indirect tension
control). In addition, the compensation of the inertia and the friction is taken into account and
the reeling hardness is open-loop-controlled.
Tension control with constant roll diameter
For this tension control with constant roll diameter, the software for the axial winder above
can be used in principle. The only difference is that the diameter is not variable but a
constant value. This is taken into account as a constant in the web-velocity-to-speed
conversion.
Settable droop
PI controller