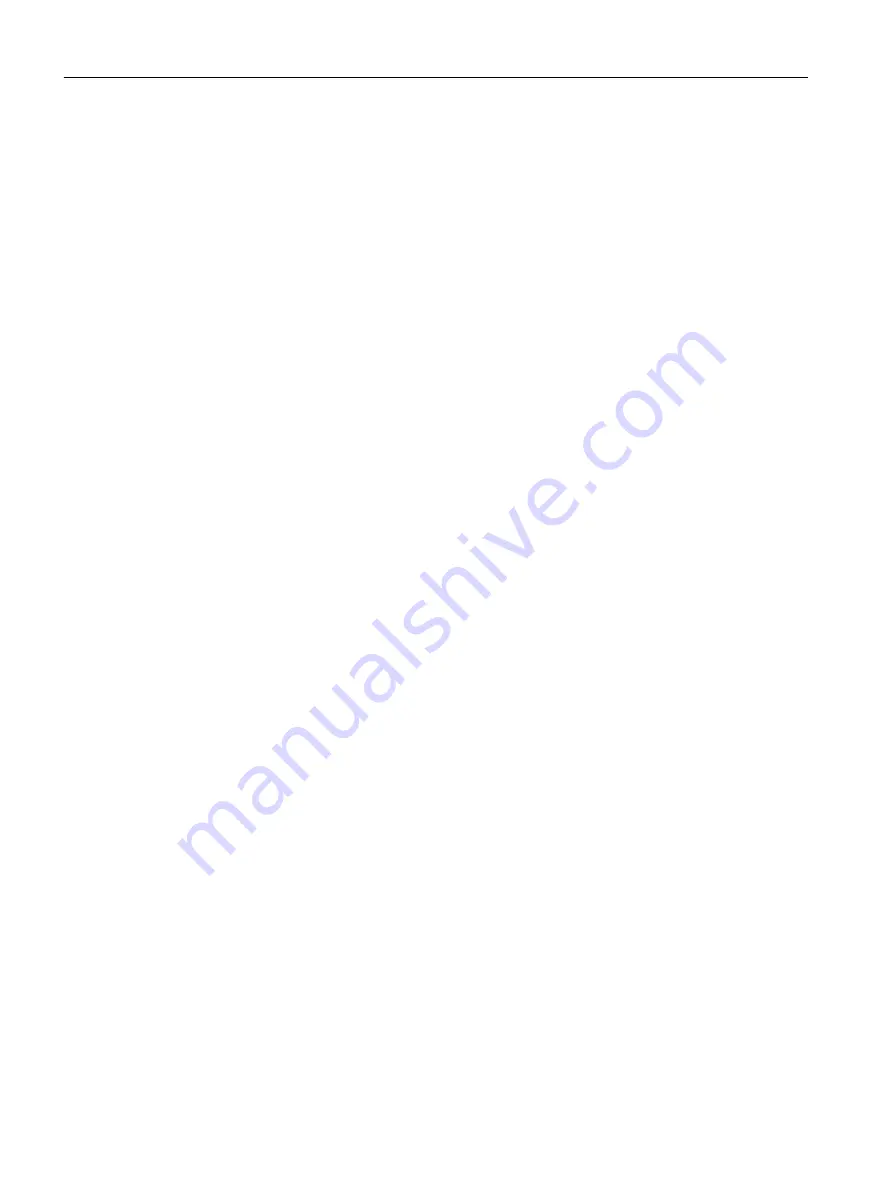
Self-ventilation (standard): Cooling method IC 411 according to EN / IEC 60034-6
Located at the ND end of the stator housing is an air intake cowl that guides the external air on
its way to the motor. The external air is drawn in through openings in the air intake cowl and
flows axially across the outer cooling ribs of the motor frame. The fan wheel for the external flow
of cooling air is attached to the machine shaft.
The fan wheels are bidirectional.
Check the cooling effect below rated speed in the case of frequent switching or braking – or if
the speed is controlled continually below the rated speed.
For two pole motors, the fan impellers are unidirectional.
Surface cooling by relative movement of cooling air (option): Cooling method IC 418 according to
EN / IEC 60034-6
Enclosed machine, no fan, enclosure surface is cooled using an external cooling air flow. The
required air flow is available on request.
Forced ventilation (optional): Type of cooling IC 416 in accordance with EN / IEC 60034-6
Cooling that does not depend on the speed is achieved by means of a unit that is independent
of the motor operating state (forced ventilation). This unit is closed to the outside by a fan cover.
It has its own main drive with fan impeller which creates the cooling air flow required for cooling
the motor.
3.3.2
Rolling bearings
Rolling bearings are used to support the machine shaft and maintain its position in the fixed part
of the machine. One rolling bearing performs the function of a location bearing that transfers
axial and radial forces from the rotating machine shaft to the non-moving part of the machine.
The second rolling bearing is implemented as floating and support bearing in order to allow
thermal expansion inside the machine and transfer radial forces.
Lubrication
The rolling bearings can be relubricated.
Bearing lifetime
The nominal (theoretical) service life of the bearings according to ISO 281 is at least 20,000
hours when the permissible radial/axial forces are utilized. The achievable bearing service life
can be significantly longer in the case of lower forces - e.g. when operated with self-aligning
couplings.
Description
3.3 Structure
1MB5 SH 400/450
24
Operating Instructions, 05/2019, A5E45959221A
Содержание SIMOTICS XP 1MB5 SH400
Страница 2: ......
Страница 10: ...Table of contents 1MB5 SH 400 450 8 Operating Instructions 05 2019 A5E45959221A ...
Страница 64: ...Assembly 5 4 Aligning and fixing the machine 1MB5 SH 400 450 62 Operating Instructions 05 2019 A5E45959221A ...
Страница 106: ...Operation 8 8 Non operational periods 1MB5 SH 400 450 104 Operating Instructions 05 2019 A5E45959221A ...
Страница 154: ...Disposal 11 5 Disposal of components 1MB5 SH 400 450 152 Operating Instructions 05 2019 A5E45959221A ...
Страница 156: ...Service support 1MB5 SH 400 450 154 Operating Instructions 05 2019 A5E45959221A ...
Страница 160: ...Quality documents 1MB5 SH 400 450 158 Operating Instructions 05 2019 A5E45959221A ...
Страница 165: ......
Страница 166: ...Germany More information www siemens com drives Siemens AG Digital Industries Postfach 48 48 90026 NÜRNBERG ...