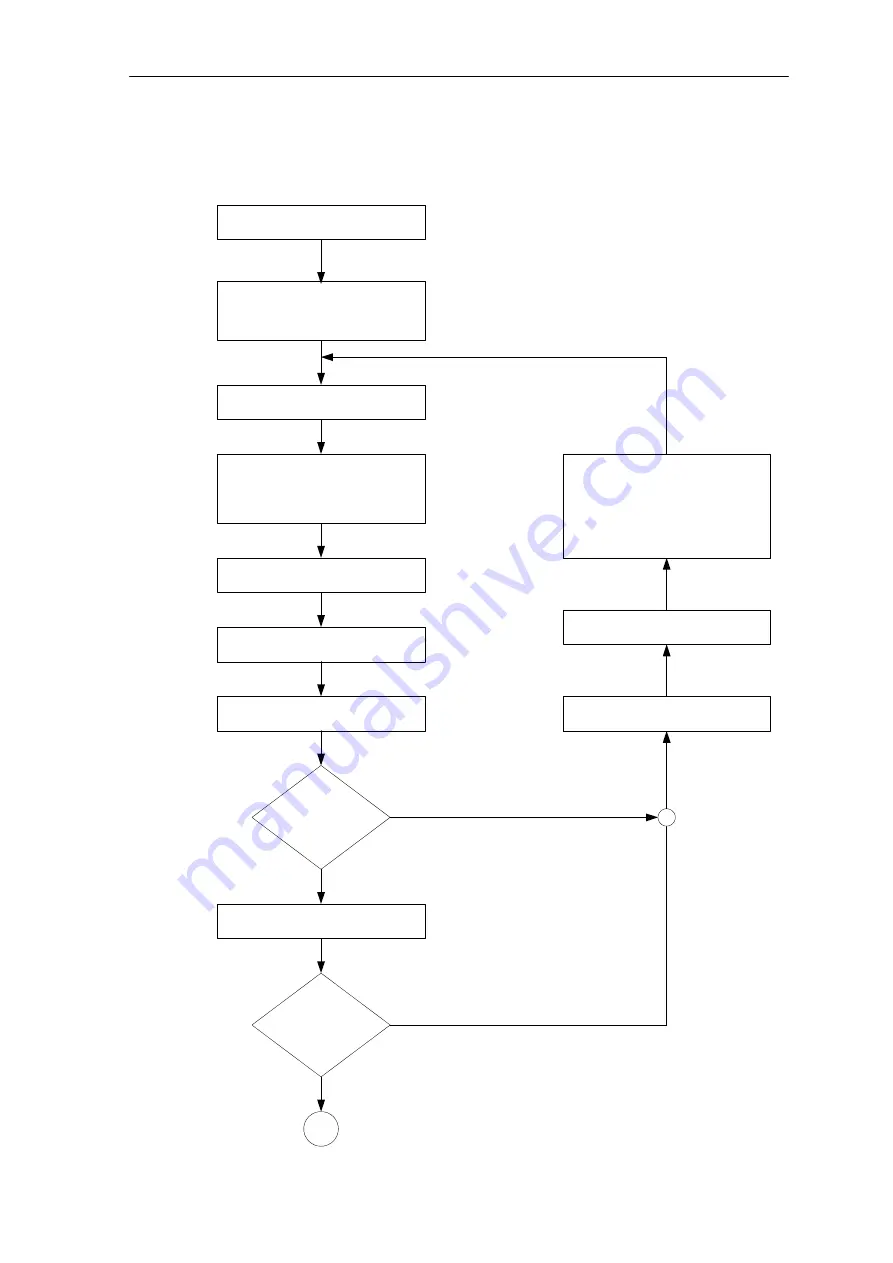
Installation
SIMODRIVE base line A Start-Up
2-5
2.3. Commissioning of SIMODRIVE base line A
General
In order to optimize the dynamic performance of the servo drive, the
commissioning is to be carried out as follows:
Main switch: Open
Start-up with the battery box
- Connect term. 63,64 to 9;
- Switch (open) between term.65
and 9;
- Term. 56/14
Main switch: close
Set the setpoint to 0V at the battery
box
Briefly energize term.65 (jog)
Does the motor
acelerate?
- Enter a low setpoint(e.g.0.1V)
- Briefly energize term.65
Does the drive
run
continuously?
1
no->fault
yes->fault
Open connectin between terminal
63 and terminal 9
Main switch: Open
Check the motor/PWM inverter
connection:
- Power connection cable
- Encoder cable
- Settings of the pole pair numbers
for motor and resolver
Adapt DIL switch S1/S2 to the motor
by setting the switch to the standard
position
yes
no