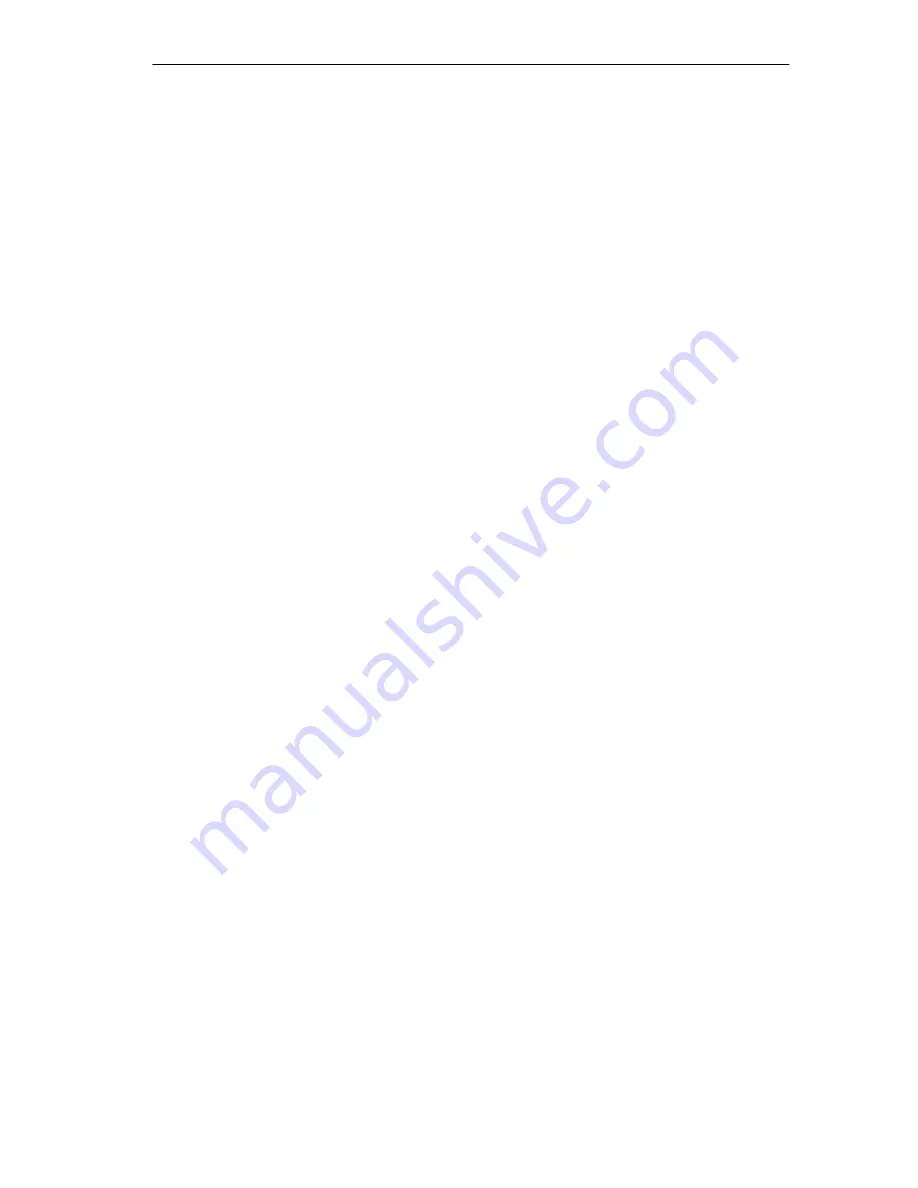
Programming the FM 452
6-3
FM 452 Electronic Cam Controller
C79000-G7076-C452-04
•
Create data blocks using the UDTs in the block folder of your S7 program. If
you use several modules, you require a separate set of data blocks for each
module.
•
Enter the module address in the channel DB and, if used in the diagnostic DB,
also at the address MOD_ADDR. You can also have the address entered
automatically by selecting the module in HW Config and then selecting a data
block in the “Properties” dialog with the “Mod Addr” button.
•
If your programming device/PC is connected to a CPU, you can now download
the FCs and DBs to the CPU.
Содержание SIMATIC FM 452
Страница 8: ...Contents viii FM 452 Electronic Cam Controller C79000 G7076 C452 04 ...
Страница 14: ...Product Overview 1 6 FM 452 Electronic Cam Controller C79000 G7076 C452 04 ...
Страница 28: ...Installing and Removing the FM 452 3 2 FM 452 Electronic Cam Controller C79000 G7076 C452 04 ...
Страница 36: ...Wiring the FM 452 Electronic Cam Controller 4 8 FM 452 Electronic Cam Controller C79000 G7076 C452 04 ...
Страница 38: ...Installing the Software 5 2 FM 452 Electronic Cam Controller C79000 G7076 C452 04 ...
Страница 62: ...Programming the FM 452 6 24 FM 452 Electronic Cam Controller C79000 G7076 C452 04 ...
Страница 68: ...Putting the FM 452 into Operation 7 6 FM 452 Electronic Cam Controller C79000 G7076 C452 04 ...
Страница 130: ...Settings 9 32 FM 452 Electronic Cam Controller C79000 G7076 C452 04 ...
Страница 140: ...Encoders 10 10 FM 452 Electronic Cam Controller C79000 G7076 C452 04 ...
Страница 146: ...Diagnostics 11 6 FM 452 Electronic Cam Controller C79000 G7076 C452 04 ...
Страница 162: ...Samples 12 16 FM 452 Electronic Cam Controller C79000 G7076 C452 04 ...
Страница 168: ...Technical Specifications A 6 FM 452 Electronic Cam Controller C79000 G7076 C452 04 ...
Страница 174: ...Connection Diagrams B 6 FM 452 Electronic Cam Controller C79000 G7076 C452 04 ...
Страница 200: ...Data Blocks Error Lists C 26 FM 452 Electronic Cam Controller C79000 G7076 C452 04 ...