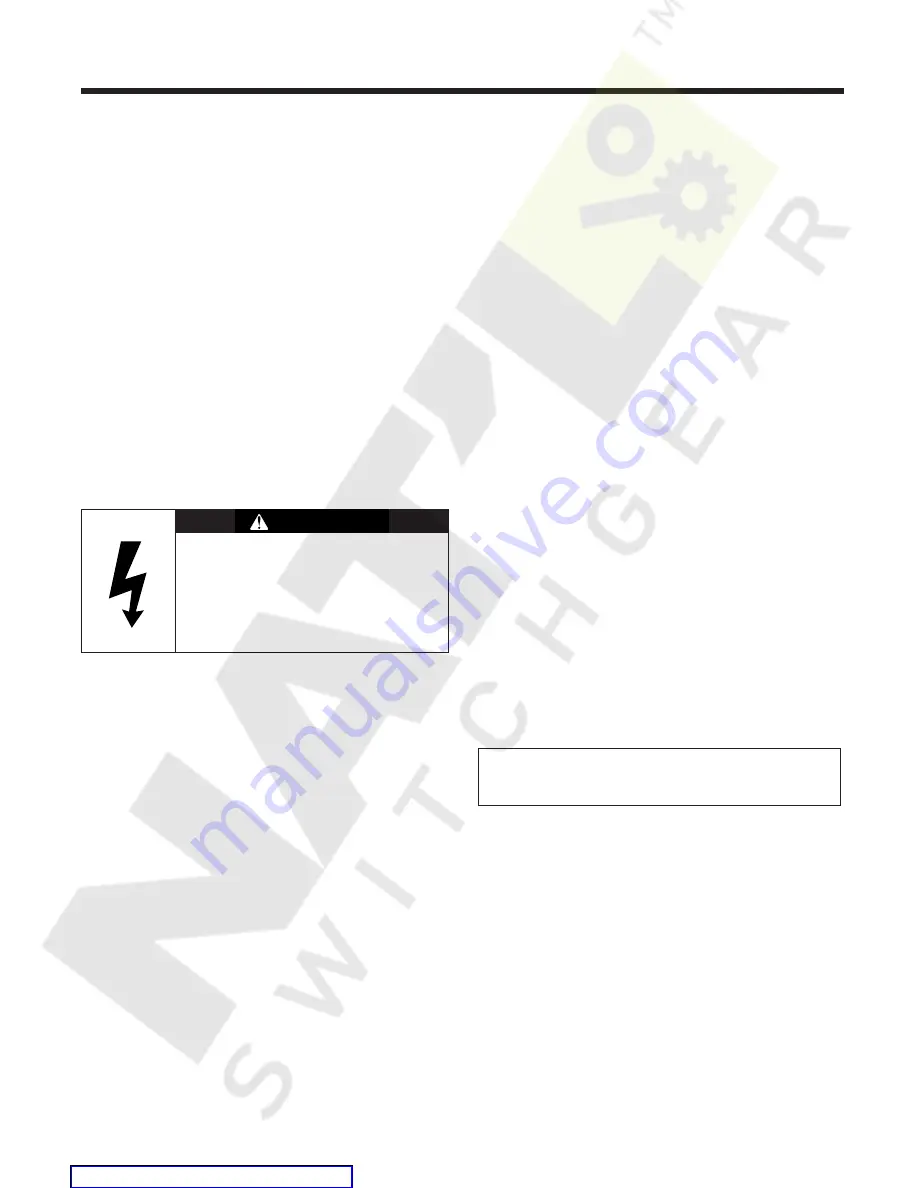
23
Bus Bar
Bus bar is furnished for connection between many of the high
voltage items within the switchgear enclosure, such as main
bus, circuit breakers, and pads for cable terminations. Cables
are provided for connection to primary disconnect assemblies
for voltage and control power transformers, and for connection
to surge arrestors or surge limiters.
Standard bus bar material is copper with silver-plated joints for
electrical connections. Aluminum bus, with tin plated joint sur-
faces, is also available. Bus bars are insulated with an epoxy
insulation applied by the fluidized bed method. Bus bar joints
are insulated with molded insulation boots (where a boot is
available) or are taped.
Additional insulation is provided by clearance thru air and bus
supports. In some locations, standoff insulators are used.
Glass polyester molded interunit bus supports are provided as
standard. Porcelain or epoxy insulator rings (inserts) mounted
in glass polyester supports, porcelain or epoxy standoff insu-
lators and/or porcelain primary disconnect bushings may be
furnished as options.
Bus Joints
When a switchgear lineup is split for shipping purposes, the prima-
ry bus and ground bus connections must be made when installing
the switchgear. These bolted connections are relatively simple to
make. Refer to
Figures 16
and
17
and these instructions.
The bus bars and connection hardware for joining the groups
together are normally shipped mounted on a bracket in one of the
units involved in the connection. When this is not possible, the
connection bars and hardware will be shipped in a separate
package, and will be listed on the “Accessories” drawing.
(This drawing is listed on the “Reference Drawing List”).
Access to the main bus from the cable termination area is
achieved by removing the main bus compartment barrier (R in
Figure 25
) which separates the main bus from the cable area.
If access to the main bus is impeded by installed equipment,
access to the main bus can usually be achieved by removal of
barrier F, shown in
Figure 25
. Barrier F is accessible from the
lower circuit breaker compartment.
For some arrangements it may be necessary to remove items
between the main bus barriers and the rear of the unit in order to
gain full access. After completion of the bus assembly and insu-
lation, these items should be reassembled in reverse sequence.
1.
Molded plastic insulation boots for bus bar joints are nor-
mally shipped factory installed at shipping splits. Note
their location and orientation, so they may be properly
reinstalled after the joint is bolted together. Carefully
remove and save the nylon hardware and the boot. In
some cases a snap closure is molded into the boot and
replaces some of the plastic hardware.
2.
All surfaces must be free of dust, dirt or other foreign
material.
Do not use any abrasive cleaner on plated contact surfaces.
Cleaning is normally not necessary and should not be
done unless parts are badly tarnished. If cleaning is nec-
essary, use a mild cleaner and thoroughly rinse the parts
to remove all residue. Keep cleaning agent off insulation.
3.
Before assembling any bus bar joint, check that the bar is
inserted through bus supports (when required) and
interunit bus supports, including neoprene grommets and
insulator rings (inserts) where that option is furnished.
Grommets (as shown in
Figure 16
) are used to support the
bus bars in the insulator rings (inserts). Observe the factory
positioning of these grommets when connecting at shipping
splits to insure that bus bars will line up properly. Normally,
the bus bar is oriented in the insert toward the front. Neo-
prene grommets are to be installed centered in the insert.
4.
Also observe the relationship of the bus bar to the breaker
riser (i.e., whether bus bar is in front of, or behind, the
riser). Maintain this relationship when connecting bus
bars. Spacers are required in some bus joint connections.
5.
Assemble all joints with the parts dry. Do not use any
grease or “no-oxide” product, even when aluminum bus
is used. Aluminum bus is tin plated, and can be applied
directly to other tin plated aluminum bar or to silver plated
copper without the use of a “no-oxide” product.
6.
Use proper hardware. For joints involving only copper bus,
heavy flat washers are used on both sides of the bus bar
joint—under the cap screw head as well as under the nut
and lockwasher. These washers insure an evenly distrib-
uted force around each bolt, producing a low resistance
joint. Proper torque value produces a joint of adequate
pressure without cold flow. Refer to
Figure 19
.
For joints involving aluminum bus, the flat washer and
lockwasher under the nut are replaced with a “Belleville”
spring washer.
7.
Assemble all joints as shown in
Figures 16
thru
19
. Install
all hardware the same way that factory bus connections
were installed. Hardware must be aligned properly or
molded insulation may not fit over the joints.
7.A. Place a flat washer on the cap screws (bolt) and insert the
cap screw through the bus joint towards rear of unit.
Note:
All main bus hardware furnished is plated high
strength steel. Cap screws are 1/2-13 SAE Grade 5. Do not
substitute with smaller or lower grade hardware than supplied.
Electrical Connections
DANGER
Hazardous voltages.
Will cause death, severe personal injury, and
property damage.
Do not contact energized conductors.
De-energize and properly ground high voltage con-
ductors before working on or near them.