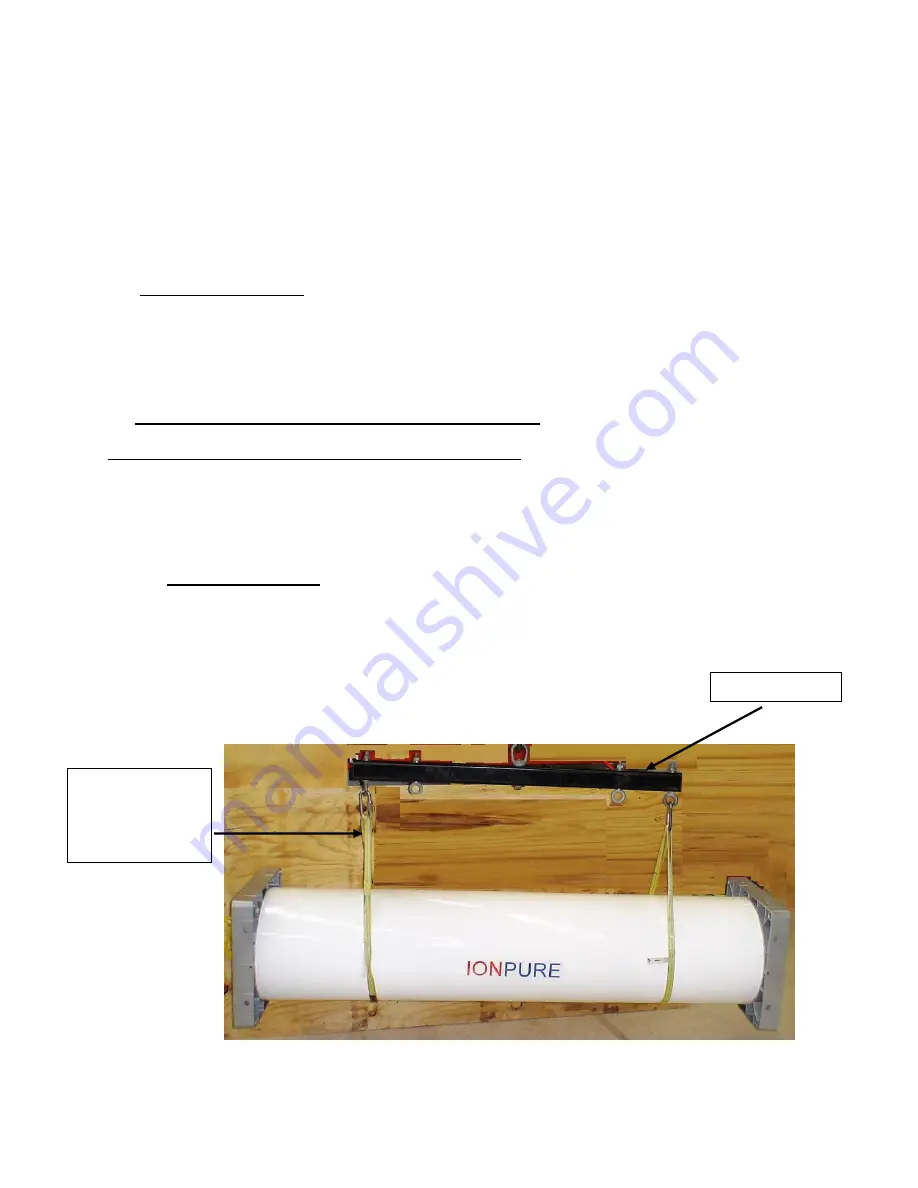
IONPURE
®
VNX50HH-2 CEDI Modules
Page 7
IP-MAN-VNX50HH2
•
Do not operate the module under conditions other than those stated in the module manual. The
prescribed feed water and electrical requirements, and flow configurations, must be followed at all
times. If the feed water quality or the product water requirements change, contact the
IONPURE
Technical Support department for assistance.
Once every six months:
•
Make sure all wiring connections are tight
•
Test safety interlocks such as flow switches or connections to upstream equipment
1.5. Shutdown Precautions
•
Confirm that the pressure in the unit is relieved until all pressures inside the unit are atmospheric.
(i.e., all pressure gauges should read zero).
•
Drain standing water and plug all inlets and outlets.
2. PRE-INSTALLATION: PREPARATION & REQUIREMENTS
This section contains the following pre-installation information:
•
Tools and equipment
- Tools and equipment needed to install the module
•
Module Inspection
-
Inspecting the VNX module for damage
•
Operating conditions
-
Temperature range, space requirements, electrical connections, feed water
specifications, plumbing and drain requirements
2.1. Tools and Equipment
The following items are required to unpack, position, and install the VNX module:
•
Spreader bar mechanism to move the module into place
•
Slip joint pliers
•
Wire
cutters/strippers
•
Phillips head screwdriver
Spreader bar
Strapping rated
for at least
1000 lbs (454
kg)
Содержание IONPURE VNX50HH-2
Страница 40: ...IONPURE VNX50HH 2 CEDI Modules Page 40 IP MAN VNX50HH2 APPENDIX B VNX50HH LAYOUT ELEVATION DRAWING B 1 ...
Страница 41: ...IONPURE VNX50HH 2 CEDI Modules Page 41 IP MAN VNX50HH2 APPENDIX B VNX50 HH PID DRAWING B 2 ...
Страница 42: ...IONPURE VNX50HH 2 CEDI Modules Page 42 IP MAN VNX50HH2 APPENDIX B VNX50 HH ELECTRICAL CONNECTIONS DRAWING B 3 ...
Страница 46: ...IONPURE VNX50HH 2 CEDI Modules Page 46 IP MAN VNX50HH2 APPENDIX C VNX50 HH PP PLUG DRAWING C 4 ...