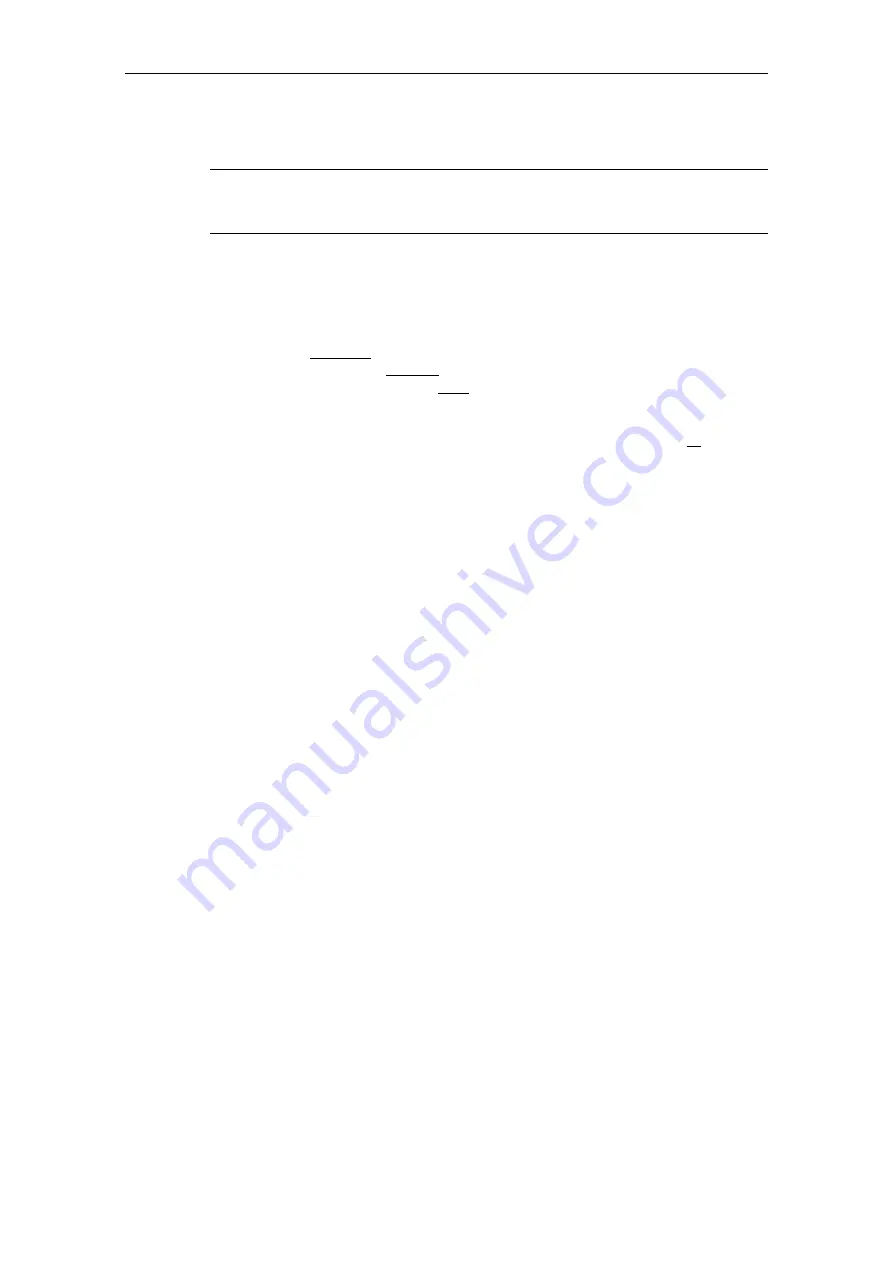
Issue 03/01
10 Engineering Information
MICROMASTER 411 & COMBIMASTER 411 Operating Instructions
6SE6400-5CA00-0BP0
121
10.2.2
Proportional and Integral Control (PI)
NOTE
MICROMASTER 411/COMBIMASTER 411 have a built-in PI controller.
References to “PID” control within parameter descriptions relates to “PI” control.
10.2.2.1 What is Closed Loop control?
Closed loop control is widely used in industrial applications to control a wide variety
of processes. Control engineering is a complex subject, but a simple closed loop
control uses a feedback signal from the process (such as temperature, pressure,
speed) a desired value or setpoint (often set manually) and a control system that
compares the two and derives an error signal. The error signal is then processed
and used to control the inverter and motor (in this case) to try to reduce the error.
The error signal processing can be very complex because of delays in the system.
The error signal is usually processed using a Proportional and Integral (PI)
controller whose parameters can be adjusted to optimize the performance and
stability of the system. Once a system is set up and stable, very efficient and
accurate control can be achieved. See Figure 10-10 on page 128.
10.2.2.2 Implementation on MICROMASTER 411/COMBIMASTER 411
MICROMASTER 411/COMBIMASTER 411 have a built in PI controller that can be
enabled by the user to allow for closed loop control. Once the PI controller is
enabled (using P2200), the PI controller internally generates the motor frequency
necessary to minimize the error between the PI setpoint and the PI feedback. It
does this by continuously comparing the feedback signal with the setpoint and
uses the PI controller to determine the necessary motor frequency. The normal
frequency setpoint (P1000 setting) and ramp times (P1120 & P1121) are
automatically disabled but the minimum and maximum output frequency settings
(P1080 and P1082) remain active.
Содержание COMBIMASTER 411
Страница 40: ...2 Installation Issue 03 01 MICROMASTER 411 COMBIMASTER 411 Operating Instructions 40 6SE6400 5CA00 0BP0 ...
Страница 60: ...3 Commissioning Issue 03 01 MICROMASTER 411 COMBIMASTER 411 Operating Instructions 60 6SE6400 5CA00 0BP0 ...
Страница 92: ...6 Troubleshooting Issue 03 01 MICROMASTER 411 COMBIMASTER 411 Operating Instructions 92 6SE6400 5CA00 0BP0 ...
Страница 98: ...7 Specifications Issue 03 01 MICROMASTER 411 COMBIMASTER 411 Operating Instructions 98 6SE6400 5CA00 0BP0 ...
Страница 102: ...8 Options Issue 03 01 MICROMASTER 411 COMBIMASTER 411 Operating Instructions 102 6SE6400 5CA00 0BP0 8 4 PROFIBUS Module ...
Страница 103: ...Issue 03 01 8 Options MICROMASTER 411 COMBIMASTER 411 Operating Instructions 6SE6400 5CA00 0BP0 103 8 5 EM Brake Module ...
Страница 154: ......
Страница 162: ...MICROMASTER 411 COMBIMASTER 411 Operating Instructions 162 6SE6400 5CA00 0BP0 ...
Страница 163: ...Issue 03 01 Geräteansicht MICROMASTER 411 COMBIMASTER 411 Operating Instructions 6SE6400 5CA00 0BP0 163 ...