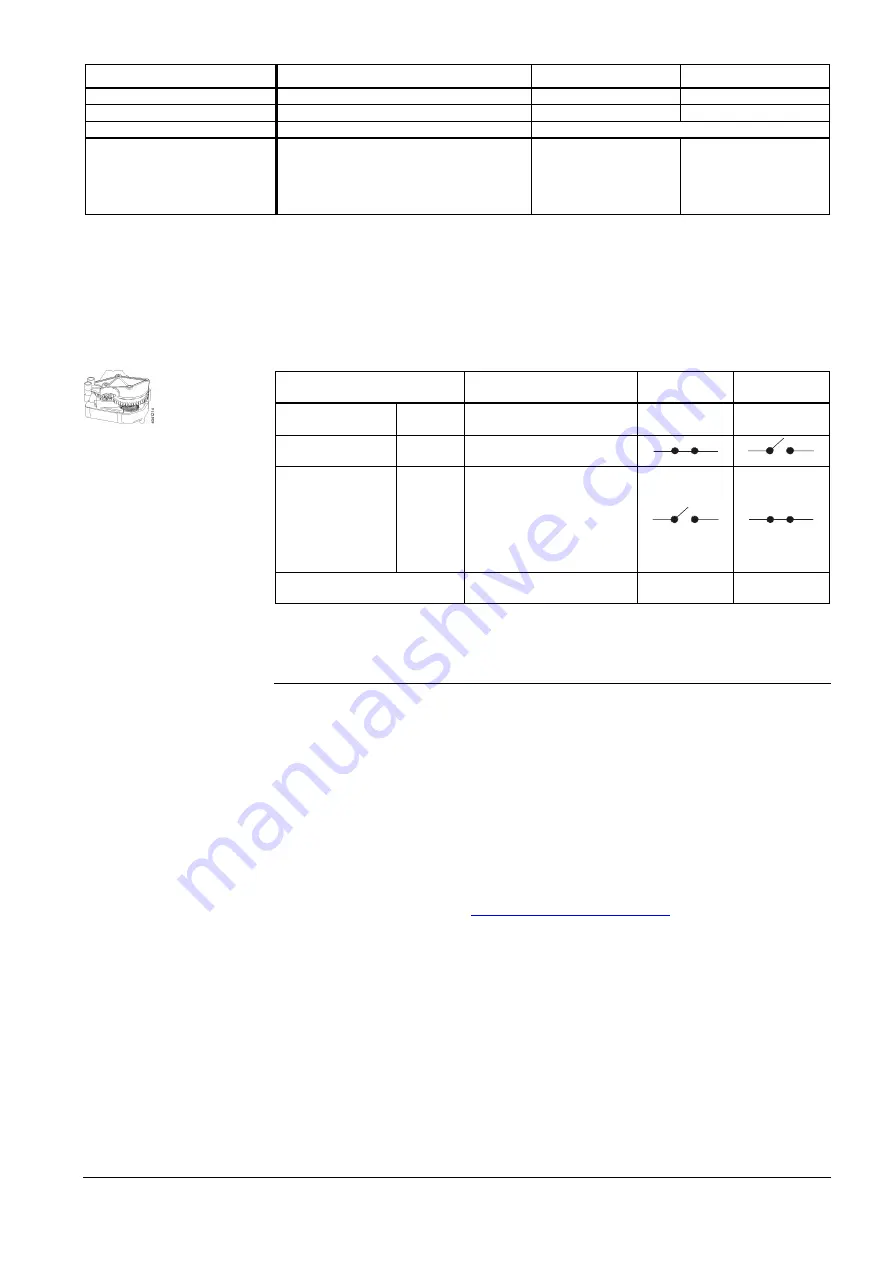
23 / 60
Siemens
Actuators SAS.., SAT.. for valves
CE1P4041en
Smart Infrastructure
Handling
2019-04-09
A
à
AB
B
à
AB
Voltage at Y1
Actuator’s stem extends
Opening
Closing
Voltage at Y2
Actuator’s stem retracts
Closing
Opening
No voltage at Y1 and Y2
Actuator’s stem maintains the position
Maintains the position
Only SAS31.50, SAS31.53,
SAS81.33, SAS81.33U,
SAT31.51
No voltage at G and G0
(fail safe function)
1)
Actuator’s stem retracts (until end position is
reached)
Closing
Opening
1)
Closing action is always completed first, also when power returns.
Observe information given in chapter 4.2.1 Positioning signal and flow
characteristic selection, page 31.
Make the function check of the mounted auxiliary switch with a point test according
to the following table – example switching point at 25% position:
Connection terminals
Stroke actuator
Terminal
S1 – S3
Terminal
S1 – S2
Voltage at Y2
Y = 0 V
Actuator’s stem retracts (until
end position is reached)
-
-
No voltage at Y1
und Y2
Y = 0 V
Actuator’s stem maintains
the position
Voltage at Y1 for
desired valve
position % + 2% x
positioning time
Example:
SAS31.00 = 27 % x
120 sec = 32.5 sec
Valve
position
% + 2%
Y = 2.7 V
Actuator’s stem extends to
desired position (27%)
Check switching point with
voltmeter
Actuator’s stem maintains
the position
-
-
3.2.2
The devices were developed specifically for use with Climatix push-button
configuration as described in document CE1A3975
1)
.
As an alternative, the bus can be configured via the local HMI; see Section
User
interface
, pg. 24.
Check the following during commissioning:
·
Bus configuration (address, baud rate, type of transmission and optional
termination). Standard address 255 allows for installation and
commissioning of several actuators simultaneously without mutual
interference.
·
The actuator parameters (direction for opening, position limits, position
adjustment etc.) can be read via the Modbus register.
1)
Documents can be downloaded at
http://www.siemens.com/bt/download
Full or partial configuration via bus
The actuators can be configured via bus connection if the settings prior to
commissioning allow for a connection to the Modbus master/programming tool (no
address conflicts and correct baud rates/transmission format settings).
·
Full configuration via bus: With a unique Modbus address, a connection can
be established from Modbus master/programming tool following startup by
means of the preset transmission format and baud rate (or auto-baud).
·
Partial configuration via bus: If the Modbus address is not unique, it must
first be set to a unique value, either by using the address input with push
button (cf. page 25) or by setting the address to 246 with push button press
Note
Auxiliary switch
ASC10.51