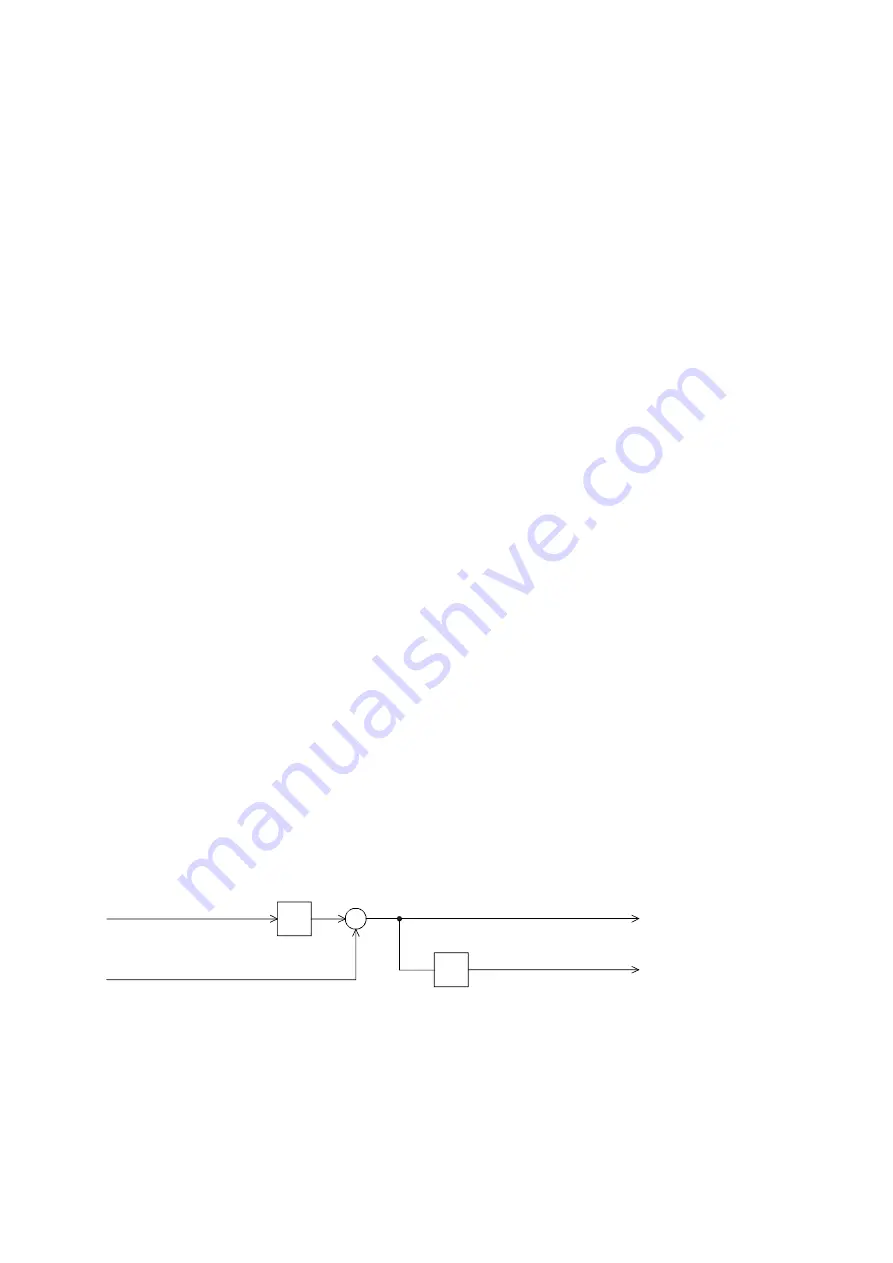
Start-Up
09.02
4-64
Siemens AG 6SE7087-6AK85-1AA0
Rectifier/Regenerating Unit Operating Instructions
The following functions are also available, each allowing a maximum of 16 process data to be transferred:
PZD Receive Broadcast
This function is used to send setpoints and control words from the master
to all slaves
on the bus
simultaneously. With this option, an identical identifier must be set on all slaves utilizing the function. This
common identifier is set in CB parameter 6 (P701). The first 4 PZDs are transferred with the value set in
P701 and the second 4 PZDs with the value in P701+1, etc.
PZD Receive Multicast
This function is used to send setpoints and control words from the master to a
group of slaves
on the
bus simultaneously. With this option, all slaves within the group using the function must be set to an
identical identifier. This group identifier is set in CB parameter 7 (P702). The first 4 PZDs are transferred
with the value set in 702 and the second 4 PZDs with the value in 702+1, etc.
PZD Receive Internode
This function is used to
receive
setpoints and control words
from another slave
, allowing PZDs to be
exchanged between drives without intervention by a CAN master. For this purpose, the identifier of PZD
Receive Internode on the receiving slave must be set to the identifier of PZD Send on the transmitting
slave. This identifier is set in CB parameter 8 (P703). The first 4 PZDs are transferred with the value set
in P703 and the second 4 PZDs with the value in P703+1, etc.
Notes regarding PZD transmission:
Control word 1 must always be transferred as the first PZD word for setpoints. If control word 2 is
needed, then it must be transferred as the fourth PZD word.
Bit 10 (control by PLC) must always be set in control word 1 or else the drives will not accept setpoints
and control words.
The consistency of process data can only be guaranteed within a COB. If more than 4 data words are
needed, these must be divided among several COBs. Since drives accept the data asynchronously, the
data transferred in several COBs may not always be accepted and processed in the same processing
cycle.
For this reason, interrelated data should be transferred within the same COB. If this is not possible, data
consistency can be assured by means of control word bit 10 (control by PLC), i.e. by setting the bit to "off"
in the first COB to temporarily prevent the drive from accepting the data from the communications board.
The remaining data are then transmitted. Finally, a COB containing a control word bit 10 set to "on" is
transmitted. Since a drive can accept up to 16 PZDs simultaneously from the communication board, data
consistency is assured.
Since a variety of different functions can be used to transfer PZDs simultaneously, data are overlayed in
the drive. For example, the first PZD from PZD Receive and PZD Receive Broadcast are always
interpreted as the same control word 1. For this reason, care should be taken to ensure that data are
transferred in meaningful combinations.
Two CAN identifiers are required for the purpose of processing parameters, i.e. one CAN identifier for PKW
Request (parameter request job to drive) and one CAN identifier for PKW Response (parameter response by
drive). These assignments are made in CB parameters as shown in the following diagram:
x2
+
+1
Node address
of drive (P918)
Basic identifier for
parameterizing (U711)
PKW Request
PKW Response
Example of PKW data exchange:
P918 = 1
This setting assigns identifier 300 to the parameter job (request)
P696 = 298
and identifier 301 to the parameter response.
https://www.aotewell.com
AoteWell Automation Sales Team
AoteWell LTD
Buy Siemens PLC HMI Drives at AoteWell.com
https://www.aotewell.com