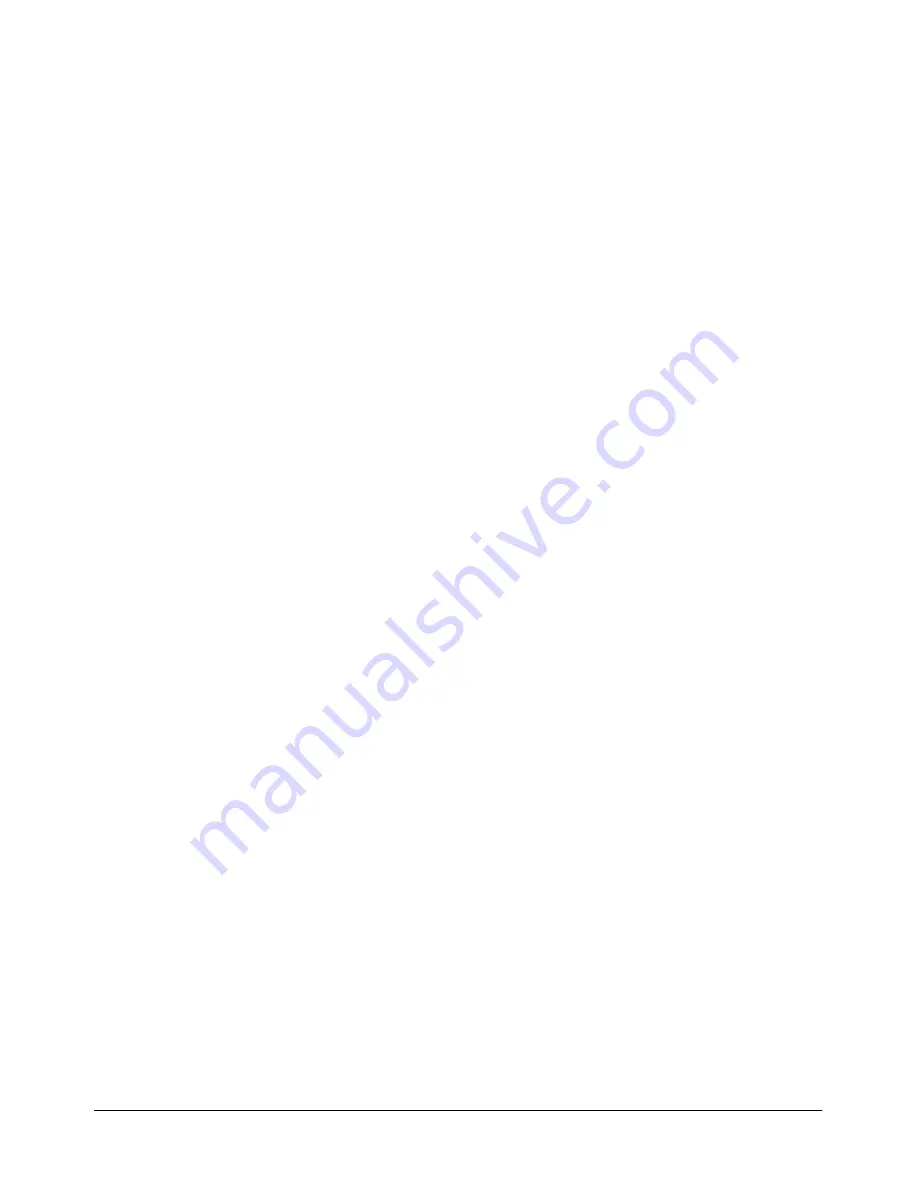
DEUTSCH / ENGLISH / FRANÇAIS / ESPA
Ň
OL / ITALIANO / SVENSKA /
Č
ESKY /
ПО
РУССКИ
/ NEDERLANDS
Fitting new bearings, grease lifetime, type of
grease
Under normal operating conditions, with horizontally mounted
motors and coolant temperatures up to 40 °C, the grease
lifetime should be:
- approx. 40,000 operating hours for speeds of 1500 rpm
- approx. 20,000 operating hours for speeds of 3000 rpm
Irrespective of the number of operating hours, the grease
should be renewed every 3 years because of ageing. In this
case the bearings should be dismounted, washed and newly
greased. The modifications with additional greasing are to be
maintained according to instructions on the lubricating data
plate.
In the case of motors operating under special conditions, such
as vertical motor position, frequent operation at maximum
speed n
max
, heavy vibration, sudden load changes and
frequent reversing operation, the bearing should be changed
at considerably more frequent intervals than at the operating
hours stated above.
The motors are standardly equipped with radial ball bearings
of 62 … series or with option K36 - radial ball bearings of 63
… series which are provided with a cover plate (ZC3 version).
The cover plate is arranged on that side of the bearing facing
the frame (stator).
NOTE:
Notice the cover plate arrangement and the bearing
clearance when changing the bearings because standard
modifications can differ from special motors!
The cover plate material should withstand temperatures from -
20 °C to +150 °C, e.g. polyacryl-rubber (ACM).
Type of grease for standard machines:
(Fa. ESSO /
UNIREX N3); grease lifetime and lubrication intervals are valid
for this type of grease only.
Compensatory greases must conform to DIN 51825-K3P-20 at
least.
Special greases are introduced on the lubricating data plate.
Avoid mixing different types of grease!
Dismantle the motor to the extent necessary. Pull off the
bearing with a suitable device (see Fig. 6). Clean the journal!
Clean the bearing, or obtain a new one, and pack it with fresh
grease.
Pack the bearing cavities flush with grease! The cover plate or
endshield is kept free of grease to prevent overgreasing.
Heat bearings evenly to about 80-100 °C and press on. Heavy
blows (such as with a hammer, ...) should be avoided.
Any worn sealing elements (such as shaft sealing ring, etc.)
should also be renewed.
If springless radial shaft sealing rings are used, the
replacement sealing rings must also be of the springless type.
Regreasing device
In the case of motors with regreasing device, take note of the
information given on the lubricating data plate!
Joint sealing
When reassembling machines with degree of protection IP55
or higher (see rating plate), the bright surfaces of the joint
between the motor frame and the endshields should be
coated with a suitable non-hardening sealing compound (such
as Hylomar, Curil).
Plastic fan (frame sizes 180M ... 315L)
Plastic fans have two cast-on tabs that snap into the ring
groove on the shaft to prevent axial movement. Before the fan
is pulled off the shaft, these two tabs must be disengaged
(screwdriver) and held temporarily in that position, e.g. by
inserting packing. In the disc at the root of the blades, there
are two openings for the claws of an extractor whose central
screw should press against the hub. On delivery, these
openings may be covered by a film of plastic and later on they
should be punched.
A suitable device should be used for pulling the fan off and
pressing it back on. Hammer blows must be avoided to protect
the bearings.
Edition N14-0903
Bestell-Nr. / Order No. 35037000000057
© Siemens AG 2000 All Rights Reserved
DEUTSCH/ENGLISH/FRANCAIS/ESPANNOL/ITALIANO/SVENSKA/
Č
ESKY/
ПО
РУССКИ
/NEDERLANDS
Siemens AG
7