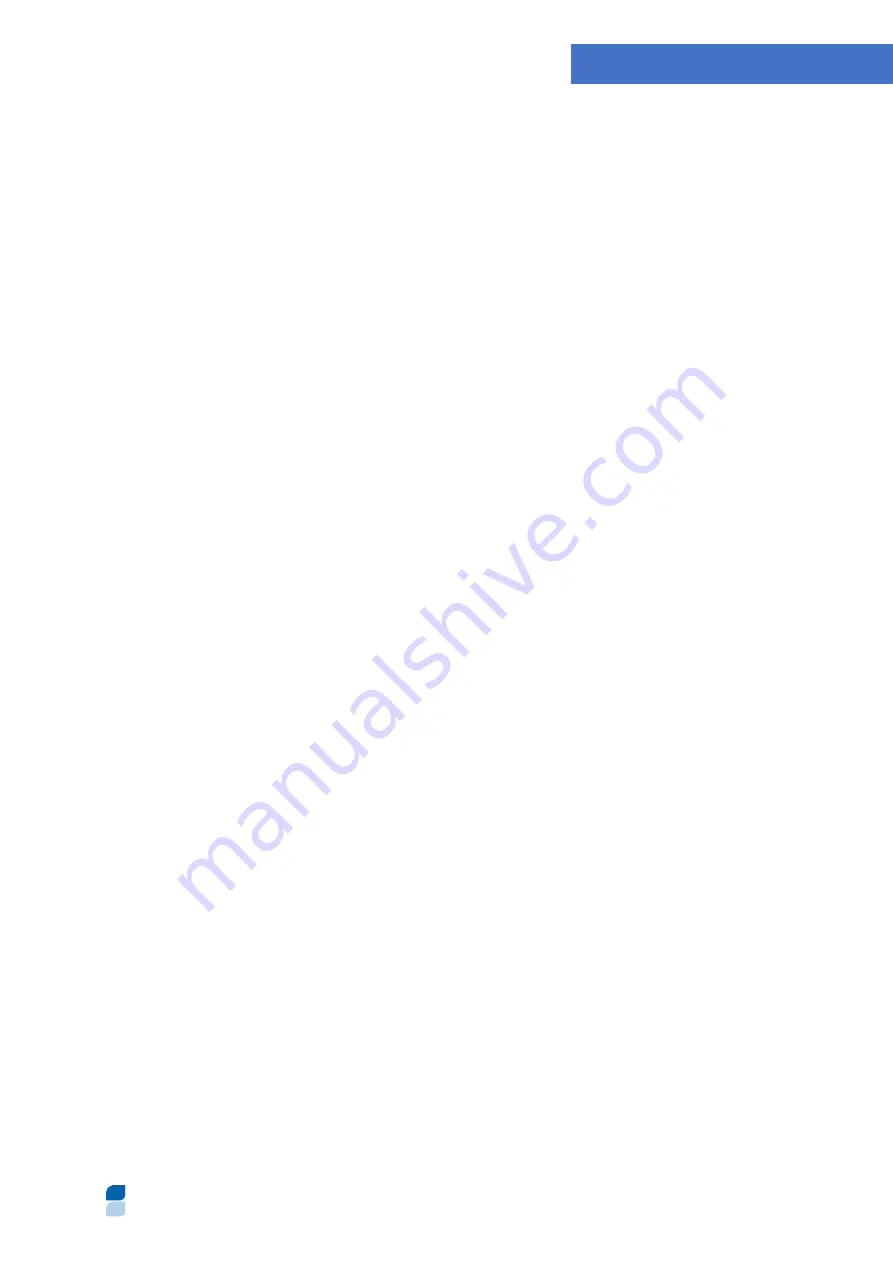
Page 81 of 106
TMS 5001
- Controlling the bulbs inside the oven:
The use of infrared bulbs to heat the preforms allows a uniform distribution of the temperature throughout the
preform in order to optimise the vertical distribution of the material. In general, heating an area reduces the
thickness of the wall in the corresponding part of the container, while cooling an area makes the thickness of
the wall increase. It must be possible to regulate, connect, switch off, bring near and separate each bulb
individually.
- Area localisation:
Preform planning is a usual technique to determine which areas affect directly certain parts of the blown
container. An adequate use of this processing tool allows processors shape the blown container thermally in
an efficient way. Using the nozzle of an altimeter, shape several preforms horizontally each 15mm or 19 mm
(depending on the oven configuration) following the central horizontal line of each oven bulb. The first mark
should match the central line of the first bulb and it should be approximately 6mm above the clamp. The shaped
preforms are identified by marking the end and loading them in the oven. Then the containers are blown and
they are recovered when the bottle is delivered. Marks are written down in the blown container, the first line of
the container matches the first line of the oven bulbs, the second one matches the second line of the oven
bulbs and so on.
8.1.3
PREFORM TEMPERATURE
- Meaning:
Preform temperature is a critical process parameter and it must be controlled. As preform temperature rises,
the orientation of the container established during the stretching stage decreases, which makes the
viscoelastic memory decrease too. As the viscoelastic memory decreases the shrinking potential decreases.
Yet, as preform temperature decreases, the shrinking potential at high temperatures increases.
8.1.4
PRE-BLOWING STAGES
- Purpose of pre-blowing:
Pre-blowing air is used to inflate partially the heated preform to slow down the stretching speed and prevent
the preform from touching the stretching rod during the stretching process, cooling the material down. The pre-
blowing is a primary process parameter that makes it possible to control material distribution.
- Electric stretching encoder position:
Each function of the blowing cycle starts by using encoder points that blow the valves. The position o f each
encoder point can be separately moved from the screen, using times.
In general, the pre-blowing encoder point is placed in such a way that pre-blowing air is activated with the
stretching rod comes into contact with the base of the preform: this is called ZERO POINT. To determine the
zero point we will show how to adjust it further on, in the practical example section.
- Pre-blowing pressure:
The speed and the volume of the pre-blowing flow are reduced by means of a fixed-diameter hole placed in
the pre-blowing supply line. The pre-blowing pressure is controlled by means of a regulator controlling the
magnitude of the variable flow. The parameterizations of the pre-blowing pressure range between 7 and 15
bars. Pre-blowing pressure affects the distribution of the material in a similar way as the situation of the pre-
blowing encoder point. Usually, when the pressure is lower the amount of material stretched down to the base
of the container increases. Yet, when the pressure is higher, the amount of material remaining in the upper
part of the container is higher too. Parameterizations of too high pressure may make the preform injection point
stick out from the end of the rod, causing misaligned openings. Parameterizations of too low pressure may
make the preform touch the stretching rod, cooling the material down and creating folds in the base or causing
problems with material distribution.
- Pre-blowing checking:
In order to assess the size and texture of the preform aneurysm, a pre-blowing test can be made. The control
screen makes it possible to carry out this test as the pre-blowing function remains active while the high
pressure blowing function is switched off. The removal of pre-blown containers will make it possible to assess
the efficiency and texture of the pre-blowing process. When placed side by side, the pre-blown containers
should have a similar shape and size. Important variations show differences between the blowing units which
might include leaks, uneven hole restrictors or poorly adjusted flow valves.
Содержание TMS 5001
Страница 1: ...TMS 5001 INSTRUCTIONS MANUAL OPERATION MANUAL ...
Страница 18: ...Page 17 of 106 TMS 5001 MACHINE ...
Страница 19: ...Page 18 of 106 TMS 5001 TOOL FOR MOULD COLOCATION Block mould ...
Страница 21: ...Page 20 of 106 TMS 5001 1 A B ...
Страница 23: ...Page 22 of 106 TMS 5001 2 3 UP UP DOWN and LEVEL DOWN and CONTACT DOWN and CONTACT ...
Страница 106: ...Page 105 of 106 TMS 5001 H 10 30 ...
Страница 107: ...Page 106 of 106 TMS 5001 if A B then A B A B A B ...