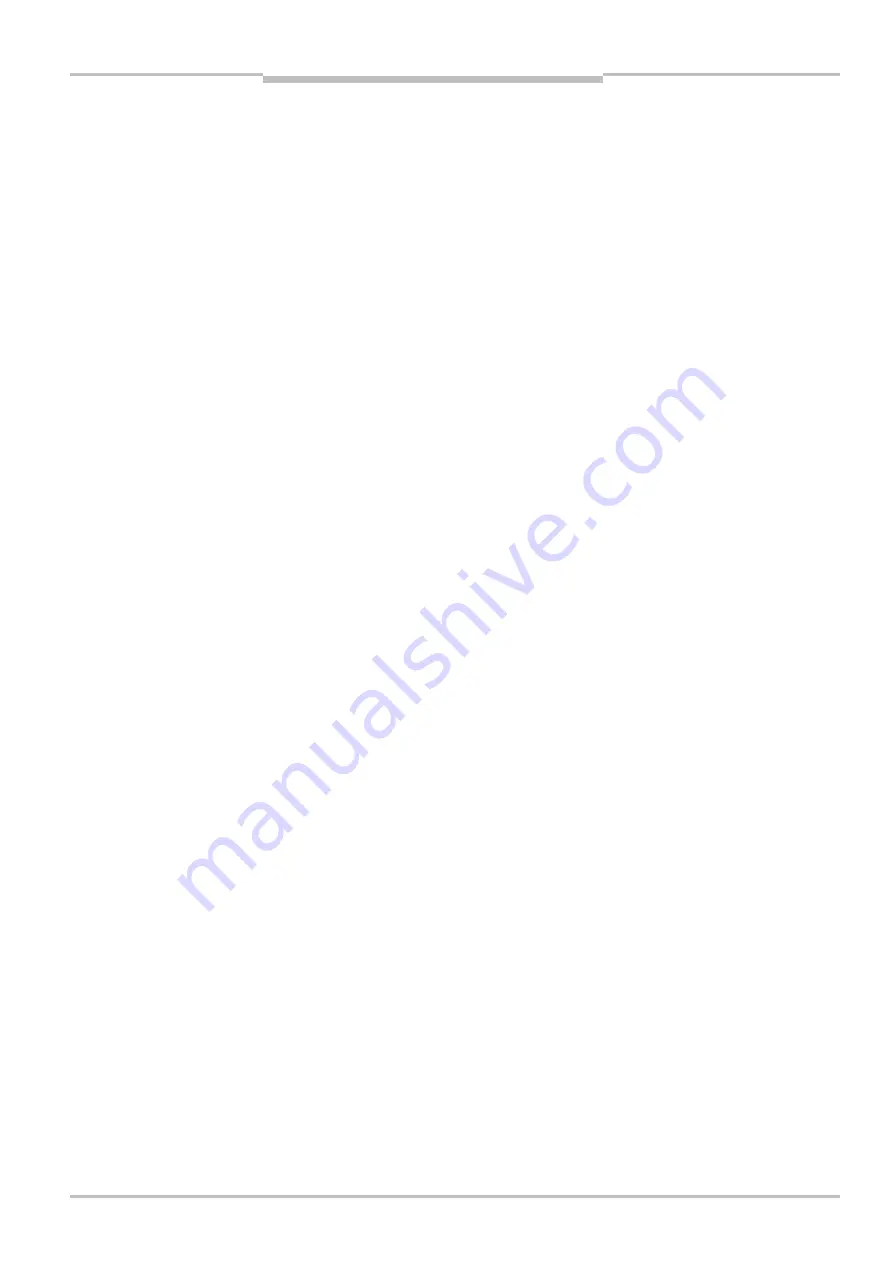
Operating Instructions
Chapter
7
UE4155
8010178/TF82/2010-03-05
© SICK AG • Industrial Safety Systems • Germany • All rights reserved
37
Subject to change without notice
Commissioning
7.2
Programming and configuration
After the planning phase is concluded and you have the necessary devices available, you
can undertake the two next steps:
configuration of the application (see chapter 8 “Configuration” on page 39)
programming the FPLC
The FPLC program accesses the inputs and outputs of the bus node via the process
images (see Appendix 12.2 on page 67). Please note: If you directly control individual bits
of an SDL connection with the aid of a function package (accessories) via “cross-routing”,
the FPLC does not have write access to these bits of the SDL connection.
You also obtain more information about possible programming errors by evaluating the
diagnostics data of the bus node (see section 9.7 “PROFIBUS diagnostics” on page 54) as
well as with the aid of the CDS (see section 9.8 “Extended diagnostics” on page 54).
If you connect the CDS to the bus node via the PROFIBUS, it is possible, for example, for
Siemens Step 7 and SICK CDS to be active simultaneously. This facilitates current testing
and correction during the programming phase.
7.3
Technical commissioning
7.3.1
Sequence for commissioning subsystems
When commissioning the entire system, you must exclude errors occurring in the sub-
systems by means of an appropriate sequence during commissioning.
First commission the devices on the SDL connections and test their system
performance.
Then commission the devices on the individual field-signal connections and test the
routing of information to the required outputs.
Do not commission the bus node until the subsystem performance is safe and as
required.
7.3.2
Offline commissioning
There are also limited options for commissioning the bus nodes without operational
PROFIBUS communication to the FPLC. In this “offline commissioning” you can use the
following functions and/or configure the following connections:
routing from the SDL connections to the field-signal connections and vice versa
monitoring the status of the SDL connections
generating the process image
diagnosis of all data up to the PROFIBUS interface with the aid of the CDS
It is, however, not possible to simulate dataflows from the FPLC to the field-signal connec-
tions and the SDL connections. Here, the bus node always transmits failsafe values during
offline commissioning.
Note