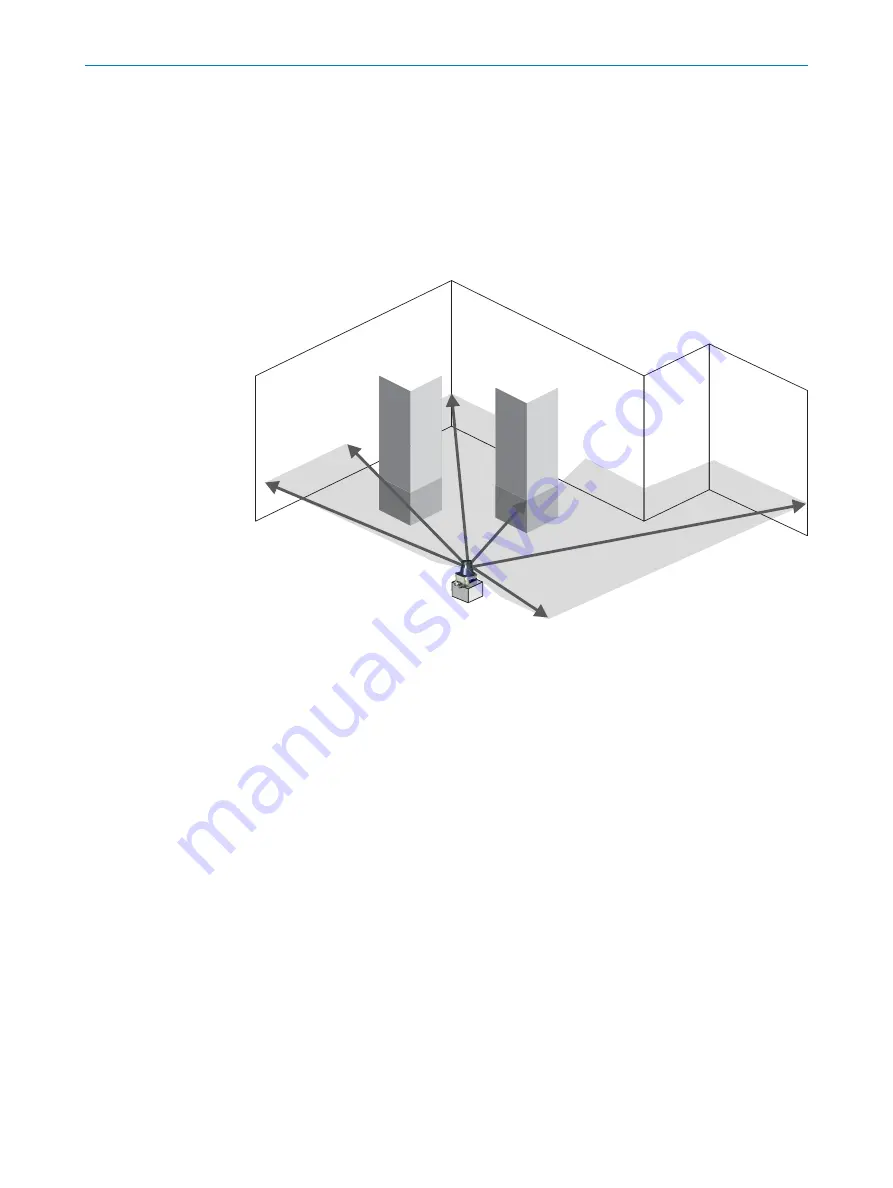
3.7
Principle of operation
3.7.1
Measurement principle
The device is an opto-electronic LiDAR sensor (laser scanner) that uses laser beams
for non-contact scanning of the outline of its surroundings on a plane. The device meas‐
ures its surroundings in two-dimensional polar coordinates, relative to its measurement
origin. Its measurement origin is marked by a circular indentation in the center of the
optics cover. If a laser beam strikes an object, the position of that object is determined
in terms of distance and direction.
Figure 4: The 2D LiDAR sensor measurement principle
3.7.2
Range finding
The device emits beams pulsed by a laser diode. If a laser pulse hits an object or
person, it is reflected on the surface of the object or person in question. The reflection
is registered by a photosensitive element in the device receiver. The device uses SICK’s
own HDDM+ (High Definition Distance Measurement) technology. With this measure‐
ment process, a measured value is formed by adding together multiple single pulses.
The device calculates the distance from the object based on the elapsed time that the
light requires between emitting the beam and receiving the reflection. Radar systems
apply this “pulse time-of-flight measurement” principle in a similar way.
3.7.3
Direction measurement
The device uses a rotating mirror to deflect the emitted laser beams, thereby scanning
its surroundings in a circular pattern. The measurements are triggered internally by an
encoder in regular angle increments.
The measuring procedure uses the averaging from multiple pulses to determine individ‐
ual measured values. A measuring point is the average value of several measurements
combined.
3
PRODUCT DESCRIPTION
14
O P E R A T I N G I N S T R U C T I O N S | TiM8xxP
8024355/1DRC/2021-12-15 | SICK
Subject to change without notice