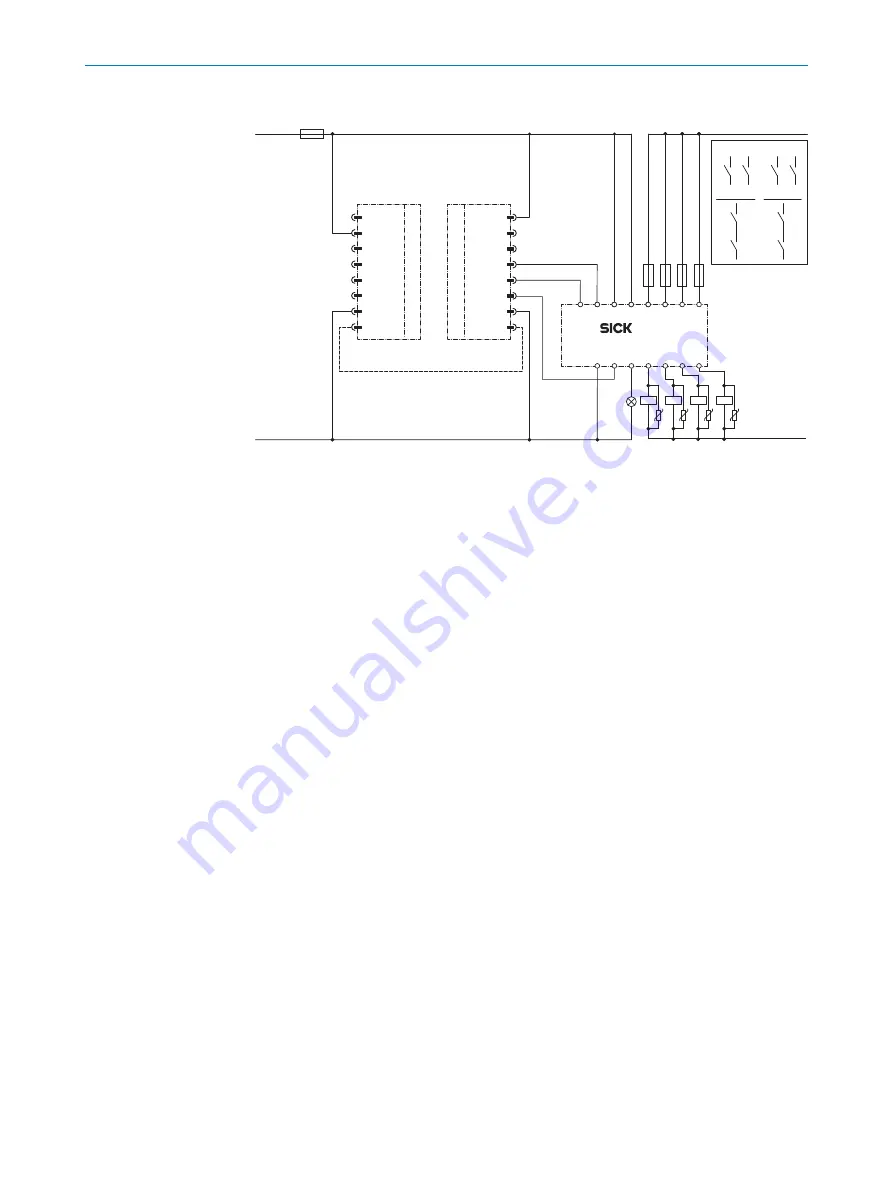
5.4.3
Connection diagrams
3) PELV
F2
F1
F4
F3
+24 V DC
0 V DC
E243849/01/2019-10-11
S
ys
te
m conne
c
ti
on
S
ys
tem connec
tion
+24 V DC
deTec4 SP1
2
1
3
5
6
4
7
8
r
RES
ADO
OSSD1
OSSD2
EDM
0 V DC
Com1
s
+24 V DC
n.c
In2
In1
n.c.
0 V DC
Com1
n.c.
2
3
4
5
6
1
7
8
2)
F0
L+
L–
1)
k2
k1
x1
x1
y1
y1
k4
k3
x2
x2
y2
y2
k4
k3
z2
z2
k2
k1
z1
z1
H1 K4
K3
K2
K1
34
44
52
62
A2
24
61
33
43
51
I1
I2
23
14
13
RLY3-OSSD4
Figure 4: ReLy OSSD4 connection diagram
5.5
Testing plan
The safety relay must be thoroughly checked by appropriately qualified safety personnel
during commissioning, after modifications, and at regular intervals,
The regular thorough checks serve to assess the effectiveness of the safety relay and
to identify defects as a result of modifications or other influences (e.g., damage or
manipulation).
The manufacturer and user must define the type and frequency of the thorough checks
on the machine on the basis of the application conditions and the risk assessment.
Determination of the thorough checks must be documented in a traceable manner.
5.5.1
Minimum requirements for the regular thorough check
The following thorough checks must be carried out at regular intervals:
•
Thorough check of the housing for damage
•
Thorough check of the cables for damage
•
Thorough check of the safety relay for signs of misuse or manipulation
•
Thorough check of the safety function
The required interval for performing these thorough checks depends on the applicable
safety capability of the overall application,
.
5
PROJECT PLANNING
14
O P E R A T I N G I N S T R U C T I O N S | ReLy OSSD4
8026008/2020-07-28 | SICK
Subject to change without notice