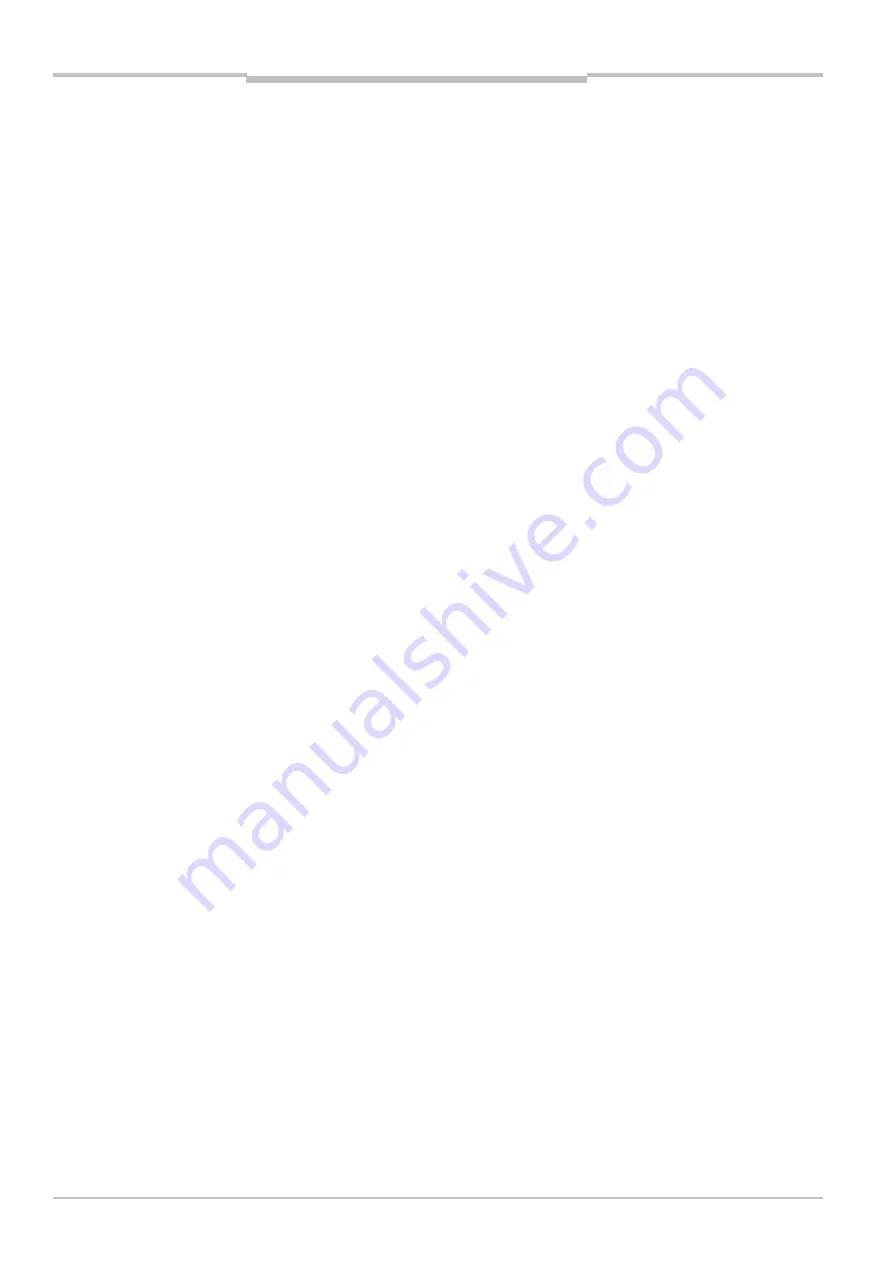
Chapter
10
MSC800
128
Operating instructions | SICK
8011540/14B8/2019-06-06
Subject to change without notice
Annex
Output time of the reading result in relation to the start of the read cycle and the
assessment conditions that are met.
Specially developed
decoder for reading 1D codes with an extremely small code height
(aspect ratio > 1:3) as well as a poor or contaminated print image.
PC configuration software, can be run under Windows 2000
TM
, XP
TM
, Vista
TM
, Windows 7
TM
,
and Windows 8
TM
.
Is used for online communication with the MSC800 in the dialog box (configuration,
display of reading results, diagnosis) and the prepared offline configuration of stand-alone
devices or the combination of the same or different SOPAS-ET-enabled SICK devices in one
project. Via
upload and
download, the
parameter values are exchanged with the MSC800 / the devices in a device-specific
manner.
Online help which supports the use of the SOPAS-ET configuration software. The functions
of the MSC800 parameters are explained in the help. Runs in an HTML browser, e.g.,
InternetExplorerTM, and can be called up from the SOPAS-ET configuration software.
In this operating mode (separate read cycle), there is only one object in the reading field
per read cycle. The start and end of the read cycle of the master/slave combination of
ID sensors (e.g., two side reading) and MSC800 are controlled by external sensors or
corresponding command strings.
When using just one ID sensor (stand-alone device, one side reading) together with the
MSC800, the free running of the ID sensor can control the reading. The sensor(s)
receive(s) the clocks via the MSC800.
In this case, the reading field length is determined by the distance of the two external
sensors for starting (start of reading field) and stopping (end of reading field) the read
cycle. The minimum reading distance between two objects must always be larger than the
reading field length.
The networking between the ID sensors and the MSC800 is carried out via the CAN
interface (CAN SENSOR network). The output of the reading result from the master is
carried out via the RS-232 / RS-422/485 interfaces and/or the Ethernet interface.
Data block in the read result of the
host interface of the MSC800. Used as the end
of the previous data contents of the code. Consists of read diagnostics data and/or
constants (control characters, letters, numbers).
In this operating mode (continuous read cycle), there are several objects in the reading
field at the same time, one behind the other. For clear assignment of the read codes to
the objects, a minimum gap must be maintained between two objects and band increment
signals must be available. The reading field length is determined by the distance of the
external sensor for the object start/end at the start of the reading field and the object
release point (data output) in the conveying direction of the MSC800 at the end of the
reading field.
The networking between the ID sensors and the MSC800 is carried out via the CAN
interface (CAN SENSOR network). The ID sensors manage reported objects in an internal
object tracking list.
Send time
SMART decoder
SOPAS ET
SOPAS-ET help
Start/stop operation
Terminator
Tracking operation
Содержание MSC800
Страница 1: ...O P E R AT I N G I N S T R U C T I O N S EN Modular system controller MSC800 ...
Страница 134: ...Chapter 10 MSC800 134 Operating instructions SICK 8011540 14B8 2019 06 06 Subject to change without notice Annex ...
Страница 135: ...Chapter 10 MSC800 8011540 14B8 2019 06 06 Operating instructions SICK 135 Subject to change without notice Annex ...