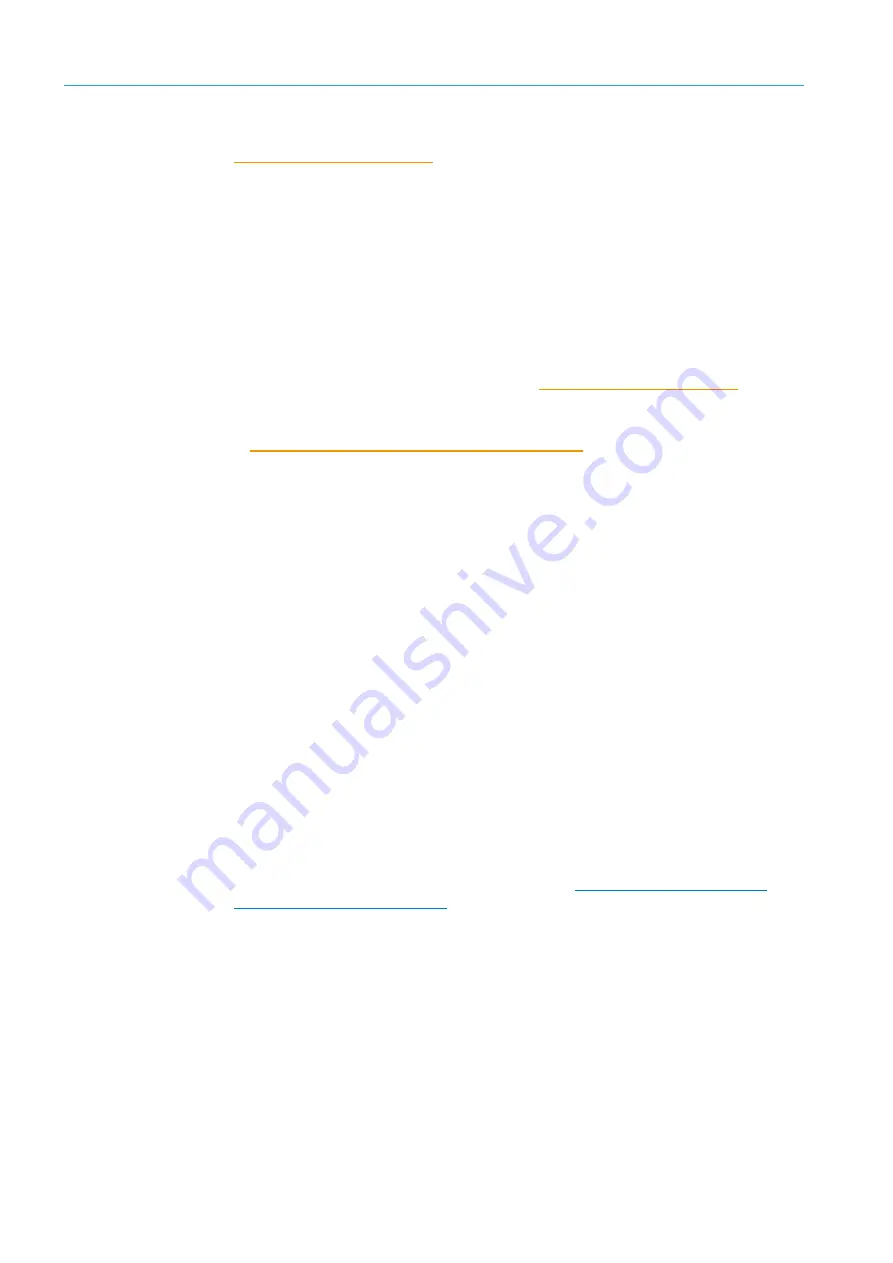
5
COMMISSIONING AND OPERATION
30
Operating Instructions | InspectorP Rack Fine Positioning
8024534 / 16UW / 2020-02-26
Subject to change without notice
Use the GSD file of the InspectorP63x. The GSD file can be downloaded at
Downloads
tab in the
Software
area.
The following SICK function blocks are recommended for receiving the measurement
results and transmitting the command:
•
S7 function block S7-1200/1500 TIA (hand-held / non-SOPAS devices, PROFIBUS,
PROFINET)
•
S7 function block S7-300/400 step 7 V5.5 (hand-held, non-SOPAS devices,
PROFIBUS, PROFINET)
•
S7 function block S7-300/400 TIA (hand-held, non-SOPAS devices, PROFIBUS,
PROFINET)
The SICK function blocks can be downloaded at
Downloads
tab in the
Software
area.
An integration example for S7 PROFINET can be found as a download in the Internet
www.sick.com/InspectorP_Rack_Fine_Positioning
Downloads
tab in the
Software
area. The integration example, among other things, contains a recommended
SICK function block and information on connecting to the device.
TCP/IP (PLC is the client)
For the
TCP/IP (PLC is client)
communication protocol (TCP/IP (PLC is client)), the
device is the server. The connected host acts as the client. The measurement results
and commands must be transmitted in binary format.
TCP/IP (PLC is the server)
For the
TCP/IP (PLC is server)
communication protocol (TCP/IP (PLC is server)), the
device is the client. The connected host acts as the server. The measurement results
and commands must be transmitted in binary format.
UDP
For the
UDP
communication protocol, the data is transmitted via UDP. More
information upon request.
Digital inputs and digital outputs
In addition to the Ethernet interface, the device can also be controlled via the digital
inputs and digital outputs.
Image recording is started via a trigger on the “Sensor1” digital input. The “Sensor2”
digital input is used to switch between the Single and Double deep modes. The
measurement results are output via 4 digital outputs,
see 5.4.6 Control via digital in-
puts and digital outputs, page 35.
The device only delivers information on the direction (up, down, left, right) via the
digital outputs. The automated storage and retrieval system can approach the target
position step-by-step based on this direction information. A quantitative statement
about the deviation between the actual and the target position of the automated
storage and retrieval system is not transmitted.
With the Ethernet interface, on the other hand, the device precisely forwards the
deviation between the actual position and the target position to the controller using X-
and Y-values. This is how the automated storage and retrieval system is controlled
directly to the target position.