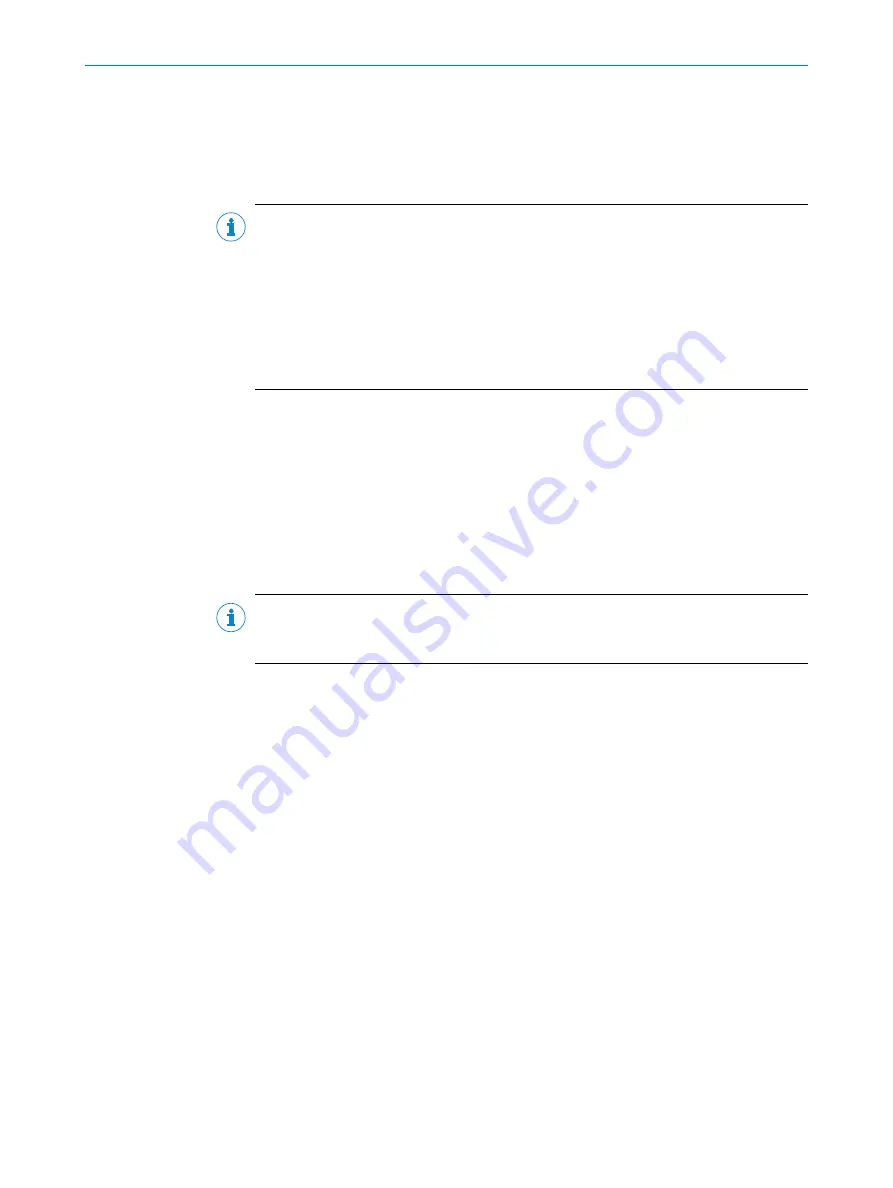
4
Transport and storage
4.1
Transport
For your own safety, please read and observe the following notes:
NOTE
Damage to the sensor due to improper transport.
■
The device must be packaged for transport with protection against shock and
damp.
■
Transport should be performed by specialist staff only.
■
The utmost care and attention is required at all times during unloading and trans‐
portation on company premises.
■
Note the symbols on the packaging.
■
Do not remove packaging until immediately before you start mounting.
4.2
Transport inspection
Immediately upon receipt at the receiving work station, check the delivery for complete‐
ness and for any damage that may have occurred in transit. In the case of transit dam‐
age that is visible externally, proceed as follows:
■
Do not accept the delivery or only do so conditionally.
■
Note the scope of damage on the transport documents or on the transport com‐
pany’s delivery note.
■
File a complaint.
NOTE
Complaints regarding defects should be filed as soon as these are detected. Damage
claims are only valid before the applicable complaint deadlines.
4.3
Storage
Store the device under the following conditions:
■
Recommendation: Use the original packaging.
■
Do not store outdoors.
■
Store in a dry area that is protected from dust.
■
To allow any residual dampness to evaporate, do not package in airtight contain‐
ers.
■
Do not expose to any aggressive substances.
■
Protect from sunlight.
■
Avoid mechanical shocks.
■
Storage temperature:
.
■
Relative humidity:
TRANSPORT AND STORAGE
4
8025941/2020-07-16 | SICK
O P E R A T I N G I N S T R U C T I O N S | MPS-G with analog output
13
Subject to change without notice