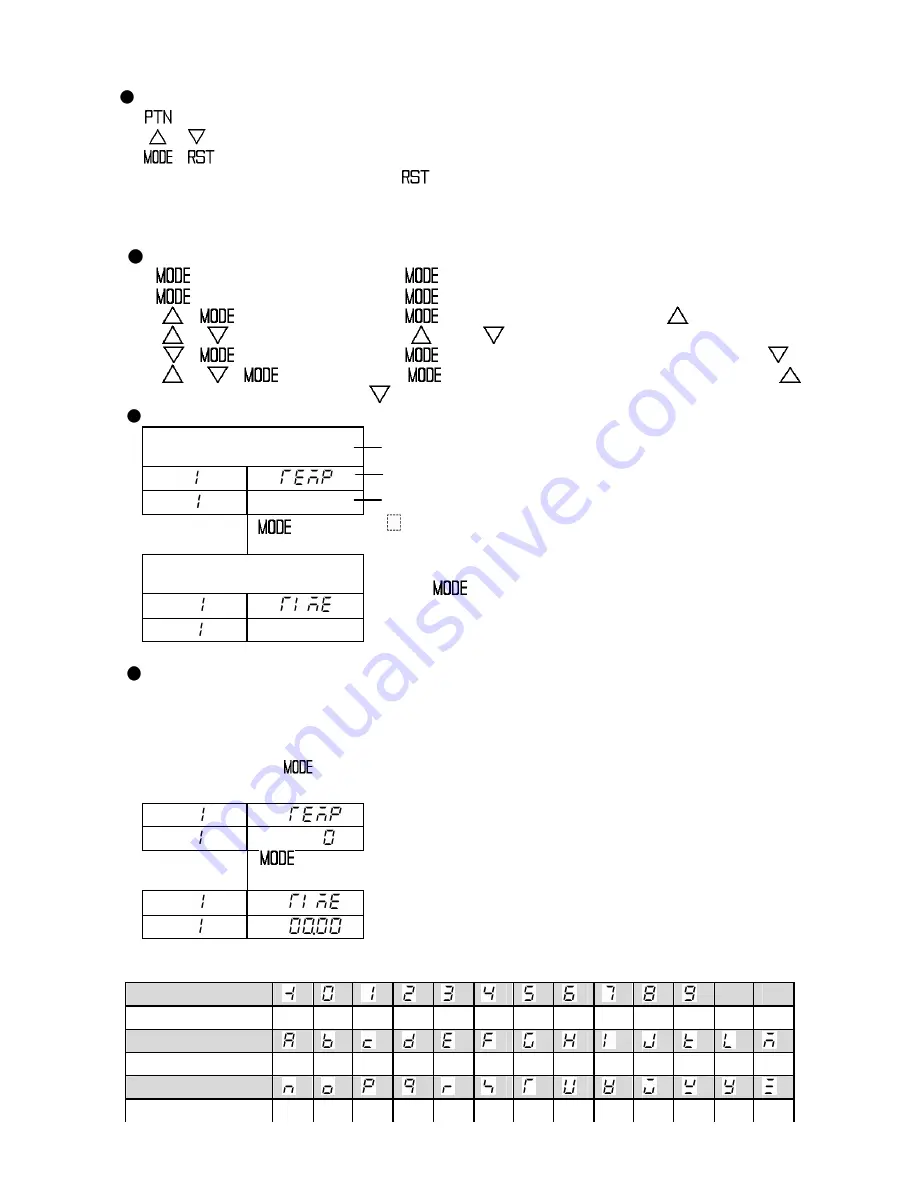
21
6. Operations
Key operations for setup
key
: Selects a program pattern number.
,
key
: Increases or decreases the numeric number or switches the selecting item.
,
key : Registers the settig value (numeric value) or selected item.
By pressing the
key, the controller reverts to the program standby
mode or program control run mode. This key is very convenient to
revert to the Program standby mode or Program control run mode
from any setting mode.
Key operations on the Operation flow chart
: Press the
key.
(3s)
: Press the
key for 3 seconds.
+
: Press the
key while holding down the
key.
+
(3s)
: Press the
and
keys for 3 seconds.
+
(3s)
: Press the
key for 3 seconds while holding down the
key.
+
+
(3s): Press the
key for 3 seconds while holding down the
and
keys.
Explanation of Operation flow chart
Step 1
Step SV setting
PTN
PV
STEP
SV
Set value
on the display means the vacancy which is not
indicated.
Step 1
Step time setting
PTN
PV
STEP
SV
Set value
Explanation of Operations
For the explanation of each setting item (pp. 24 to 33), current status of each display is
indicated with diagrams on the left side and its item name and operation method are
described on the right side.
By pressing the
key, the set value is saved and the setting item proceeds to the
next one.
PTN
PV
STEP
SV
PTN
PV
STEP
SV
Characters
Indication
Numeric number -1
0
1
2
3
4
5
6
7
8
9
Indication
Alphabet
A
B
C
D
E
F
G
H
I
J
K
L
M
Indication
Alphabet
N
O
P
Q
R
S
T
U
V
W
X
Y
Z
(e.g. Pattern 1 is set here.)
If the
key is pressed at Step 1 Step SV setting, the
set value is saved and the setting item proceeds to
the next one [Step 1 Step time setting].
Setting item
PTN and PV display
STEP and SV display
Step 1 step SV setting
Step 1 step time setting
Содержание PCD-33A
Страница 1: ...INSTRUCTION MANUAL FOR PROGRAMMABLE CONTROLLER PCD 33A ...
Страница 62: ...62 5 7 6 8 9 ...