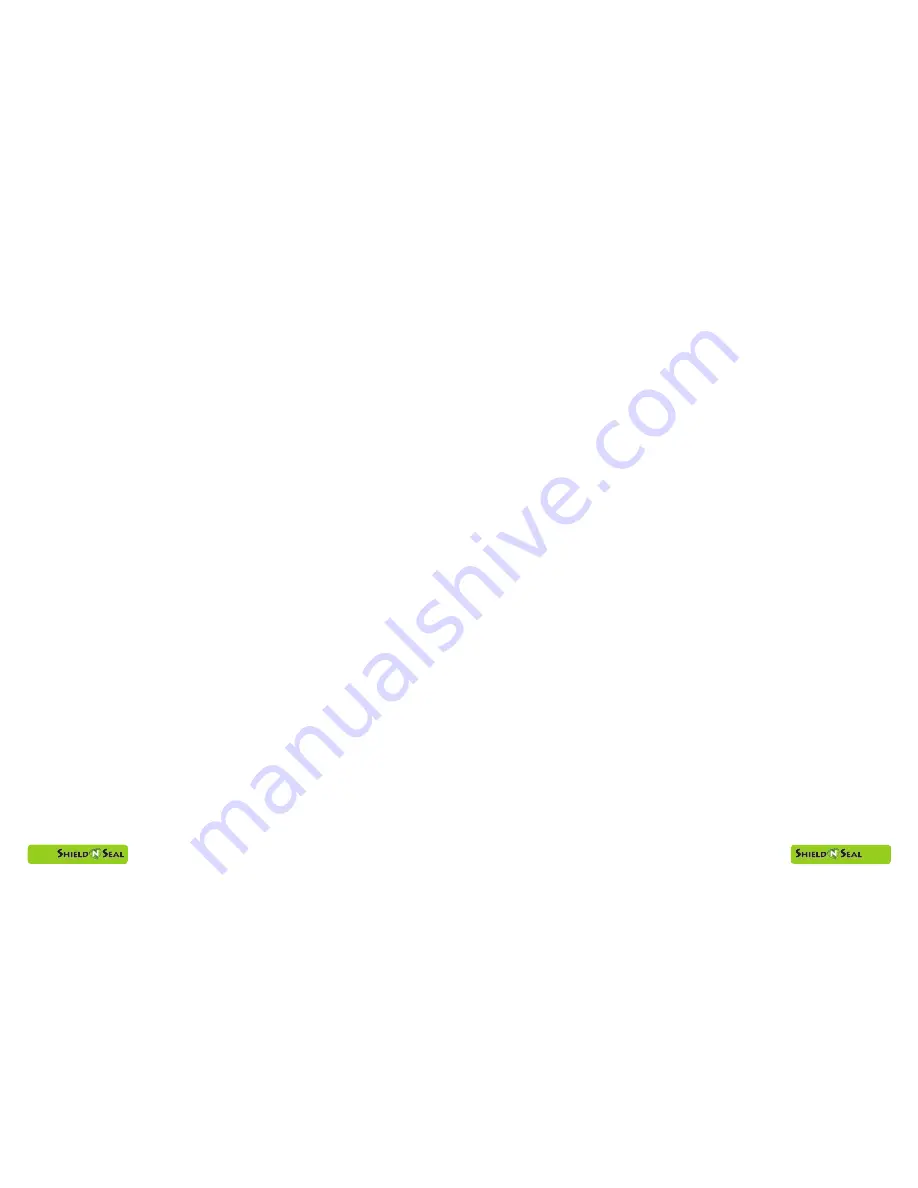
Troubleshooting Guide
10
Troubleshooting
Under the proper circumstances, your Shield N Seal
®
Shield Sealer
TM
Vacuum Sealer will
give you years of professional performance. In some instances, problems may arise. Please
consult the trouble shooting guide below before calling customer support.
Note: In order to maintain a longer lifetime, we strongly recommend that you let the machine rest least
20 seconds between each seal.
When the machine has been working continuously for a long period of time, and is
overheated, the thermal overload will start to protect the machine. “
“E1” will appear on the digital display. In this case, please shut down the machine and dis-
connect the electricity, and allow the machine to rest for about 20 minutes. Then re-con-
nect, re-start, and continue the sealing process.
To avoid burning hands, when you open the machine lid, press “Seal”
button, “E2” will blink on the digital display, the machine does not heat. Just simply close
the machine lid to use the machine again.
A protective device will protect the machine from overheated. When the display shows “E3”,
shut down the machine and disconnect the power. Let the machine rest for 20 minutes.
Then re-connect, re-start, and continue the sealing process.
THE VACUUM SEALER WON’T TURN ON
- Ensure that the machine is properly plugged into a grounded outlet and
that the outlet works properly.
- Check the power cord for tears and frays. Do not use machine if power cord
is damaged.
THE VACUUM SEALER DOESN’T COMPLETELY VACUUM OR REMOVE AIR FROM BAG
- To vacuum and seal properly, edge of bag must be across the seal bar. Make sure
the bag is inside the chamber seal gasket and that there are no wrinkles in the bag
along the seal bar.
- Check for a secure seal on sides of bag.
- The Vacuum Sealer and vacuum bag need to be clean, dry and free of debris for
the vacuum process to be successful. Wipe surface of seal bar and clean inside of
bag and try again.
- Check to make sure the bags / rolls you are using are compatible with the
Shield N Seal
®
Shield Sealer
TM
. Shield N Seal
®
Sealers are currently compatible with all
FoodSaver,
®
Seal-A-Meal,
®
and most vacuum sealers, including vacuum canisters.*
* FoodSaver
®
and Seal-A-Meal
®
are registered trademarks of Jarden Corporation
VACUUM BAG LOSES VACUUM AFTER BEING SEALED
- Sharp items can puncture small holes in bags. To prevent this, cover sharp edges
with paper towel and vacuum in a new bag.
- Some fruits and vegetables can release gases (out-gassing) if not properly
blanched or frozen before packaging. Open bag. If you think food spoilage has
begun, discard food. If food spoilage has not yet begun, consume immediately. If in
doubt, discard food.
Note: signs of spoilage include mold, foul odor, slimy texture, rotten or black in color, etc.
THE VACUUM SEALER IS NOT VACUUMING CANISTERS PROPERLY
- The accessory hose may not be properly attached. Ensure the hose is completely
inserted into the lid of the canister and the accessory port and try again.
- Make sure the canister lid is turned to the “Vacuum” setting (In Marinate Mode to
“Open” setting).
- Leave adequate head space at the top of the canister.
- Make sure there isn’t any damage to the canister and lid. Sometimes hairline
cracks can develop in canisters. When this happens the canister is no longer
air tight and should be discarded.
- Twist knob on lid of canister to make sure it is attached securely.
A very seldom occurrence; the electronics and/or programming may be in error mode.
Disconnect the cord / electricity, then re-connect it.
Customer Support
If, after reviewing the troubleshooting guide above, and you still need support, please
contact the Shield N Seal
®
Team for support:
Call: 855.770.7325
Monday- Friday from 9am to 5pm
Pacific Standard Time
Email: [email protected]
_____________________________________________________________________________________
Thank you for purchasing the Shield N Seal
®
Shield Sealer
TM
. Happy Vacuuming!
Troubleshooting Guide
11
12