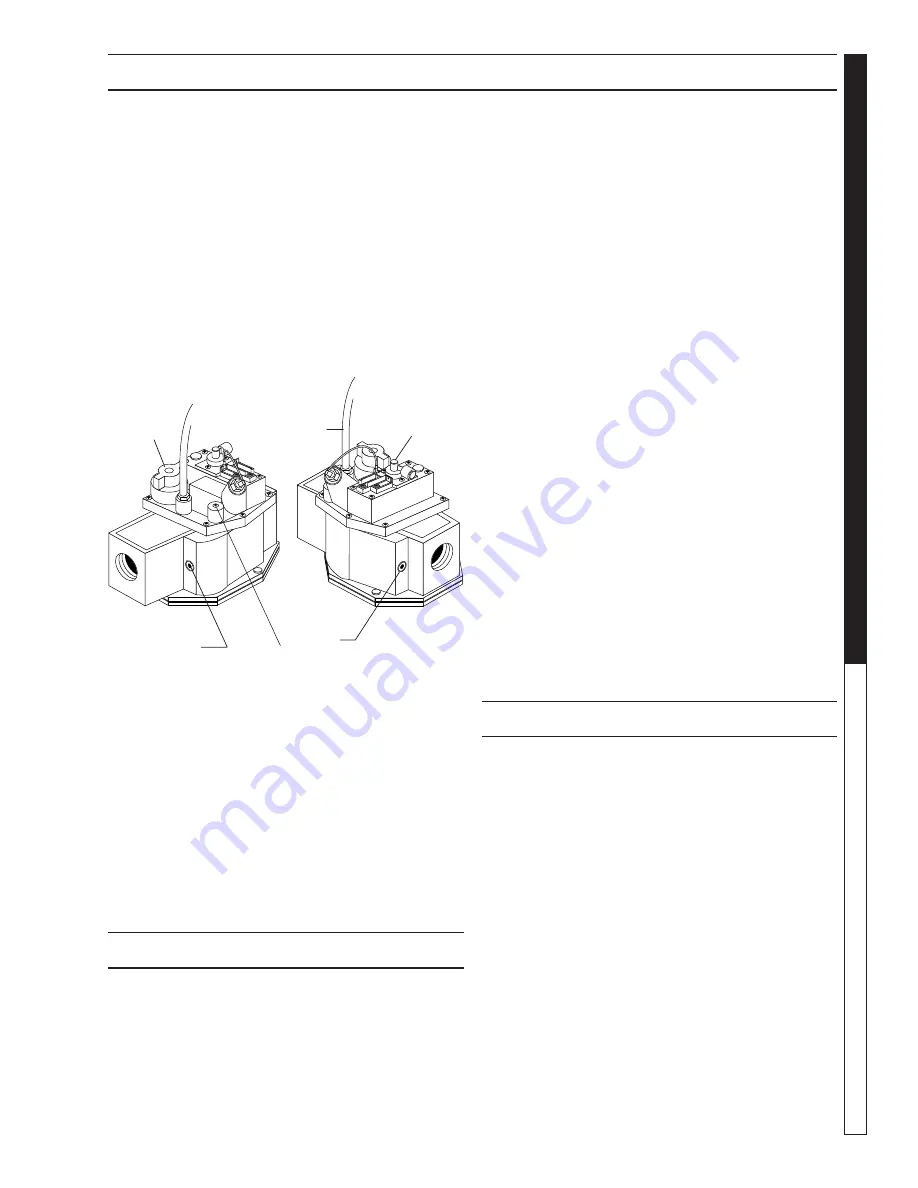
97-610, 97-6152 • REV. 7/04
21
PRESSURE
W
ASHER
T
ro
u
b
leshooting Guide
MAINTENANCE & SERVICE
Gas Valve Regulator Adjustment:
(See Fig. 5)
Adjustment of the built-in regulator isn’t normally nec-
essary, since it is preset at the factory. However, field
adjustment may be accomplished as follows:
1. Attach manometer at both inlet and outlet pressure
ports.
2. Remove manifold pressure adjustment screw cap.
3. With small screwdriver, rotate manifold pressure ad-
justment screw clockwise to increase or counter-
clockwise to decrease gas pressure.
4. Replace manifold pressure adjustment screw cap.
Figure 5
Pilot Burner Adjustment:
1. Remove pilot adjustment cap.
2. Adjust pilot key to provide properly sized flame.
3. Replace pilot adjustment cap.
Rupture Disk:
If pressure from pump or if thermal expansion should
exceed safe limits, the rupture disk will burst, allowing
high pressure to be discharged through hose to ground.
When the disk ruptures, it will need to be replaced.
Torque to 35 ft. lbs.
PROPANE GAS
(Vapor Fuel Only)
General Safety Precautions:
Have a qualified gas service person assist in any gas
burner installation or service. Few maintenance people
or mechanics are knowledgeable in gas controls or re-
lated safety practices. Since propane gas is heavier than
air, unburned propane gas will gravitate to the floor rather
Gas Valve Adjustment
than rise out of the stack. Hence, adequate floor space
and good ventilation are especially important with pro-
pane systems.
Gas Pressure Requirements:
All propane fired machines operate on gas phase only.
They are designed to operate at a pressure of 11 w.c.i.
(between 1/3 and 1/2 of one PSI), and are often oper-
ated at even higher pressures when extra heat is
needed.
Exterior regulators are needed to control the system.
Propane bottles are not included with the machine. A
high pressure regulator should be installed on the pro-
pane bottle and a low pressure regulator attached to
the pressure washer.
Propane Cylinder Capacity:
An important consideration with propane systems is the
capacity of the supply cylinder relative to the needs of
the burner. The burner operates on propane as a gas.
As gas is used from the propane cylinder, the liquid in
the cylinder boils to maintain gas pressure. This boiling
process cools the liquid, and in a heavy, continuous-
demand situation, the liquid temperature can fall to the
point at which it cannot provide gas as rapidly as is
needed. In this case, it may be necessary to warm the
propane cylinder by directing a warm spray, not over
120°, on the cold cylinder, or by manifolding two pro-
pane bottles together to increase total vaporization ca-
pacity. It is recommended that a minimum 100 lb. pro-
pane bottle be used on the machine, depending on the
length of running time desired.
BURNER FEATURES
Operated Automatic Valve:
This machine is equipped with a thermopile self-pow-
ered combination gas control. This system is designed
as a constant burning pilot. Lighting of the pilot is ac-
complished by manually lighting the pilot. A thermostat
and flow switch control the main solenoid valve.
Care of Main Burner:
Because of condensation from the heater coils dripping
down on the burners, scale buildup may occur in the
burner jet orifices.
1. TO REMOVE BURNER MANIFOLD FROM
WATER HEATER COIL:
Turn off the gas at the main burner by turning the
knob to the “OFF” position on the gas valve and
main gas supply.
Outlet
View
Manifold Pressure
Adjustment Screw
Under Cap
Line to
Pilot Light
Control
Knob
Outlet
Pressure
Port
Inlet
Pressure
Port
Inlet
View
Pilot Key
Adjustment