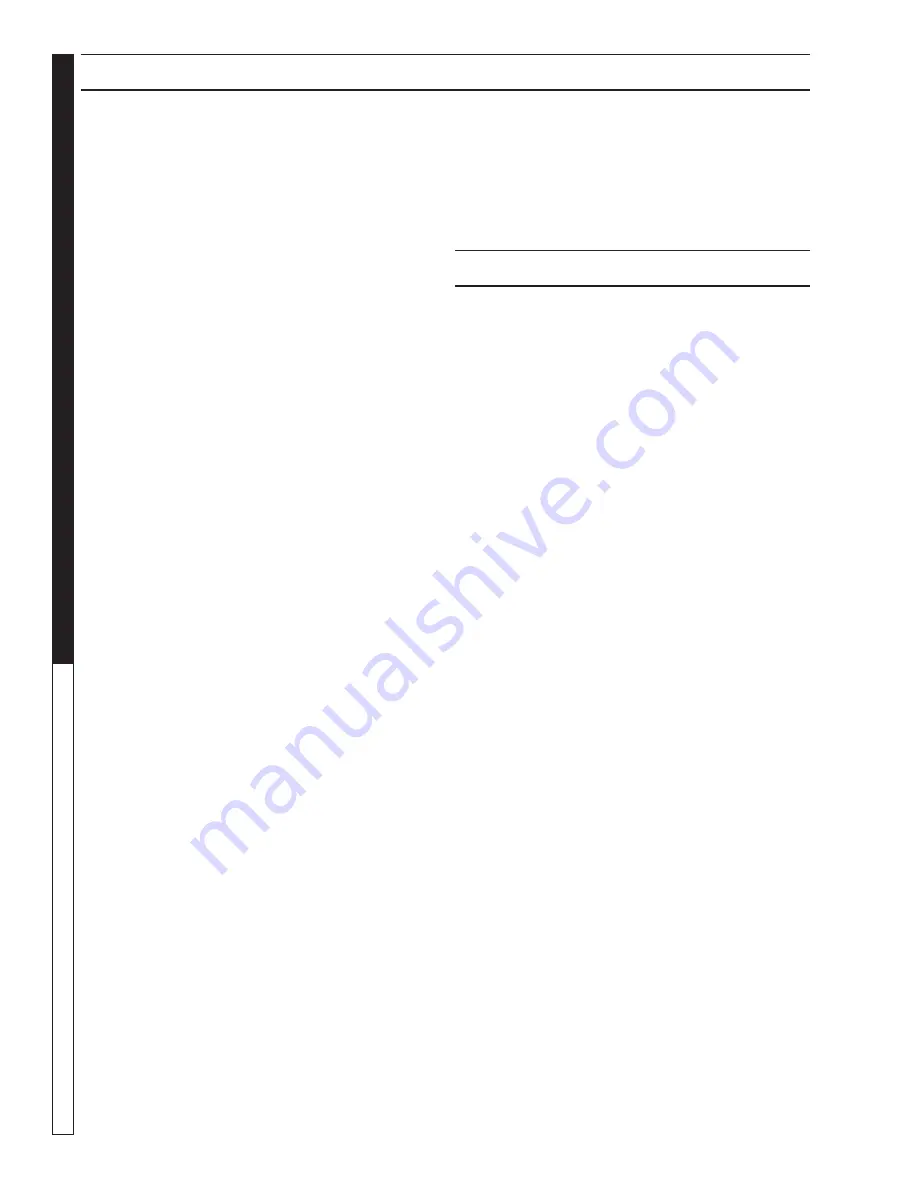
97-610, 97-6152 • REV. 7/04
PRESSURE
W
ASHER
T
ro
u
b
leshooting Guide
20
Spray Nozzles:
Each machine is equipped with one or more spray
nozzles, depending on the model. Different spray
nozzles are calibrated for each machine, depending on
the flow and pressure of that particular model. Spray
nozzles vary in bore size and angle of spray. Popular
spray angles are 0°, 15°, 25°, 40°. When ordering, please
specify size and angle of nozzle. Nozzle size for each
machine is located on the serial plate.
Unloader Valves:
Unloader valves relieve pressure in the line when a spray
gun is closed. Unloader valves are preset and tested at
the factory before shipping. Occasional adjustment of
the unloader may be necessary to maintain correct pres-
sure. For valve adjustment contact your nearest dealer
or call technical support.
Winterizing Procedure:
Damage due to freezing is not covered by warranty.
Adhere to the following cold weather procedures when-
ever the washer must be stored or operated outdoors
under freezing conditions.
It is necessary to protect your machine against freez-
ing when temperatures drop below 32° F. Siphoning a
small amount of antifreeze into the system is recom-
mended. This is done by pouring a 50-50 mix of anti-
freeze and water into the float tank and then siphoning
100% antifreeze through the detergent line with the
pump on. If compressed air is available, an air fitting
can be screwed into the float tank strainer fitting, and
by injecting compressed air, all water will be blown out
of the system. The use of a draft diverter will prevent
the wind chill factor from freezing the coil.
Low Pressure Diagnosis:
(Machines with spray gun)
Refer to Troubleshooting Chart for low pressure. If the
trouble is found to be either the unloader or the pump,
your next step is to determine which is the problem.
This can be done by eliminating the unloader from the
system and attaching the 50' discharge hose directly to
the pump. If high pressure is developed in this manner,
the pump is good and the unloader needs to be repaired
or replaced. If low pressure is still present, then the pump
needs repairing.
CAUTION: When using this procedure to test com-
ponents keep the spray gun open at all times.
High Limit Hot Water Thermostat:
For safety, each machine is equipped with an adjust-
able thermostat. In the event the temperature of the wa-
ter should exceed its operating temperature, the ther-
mostat will turn the burner off until the water cools.
Pumps:
Use only SAE30 weight non-detergent oil. Change oil
after first 50 hours of use. Thereafter, change oil every
three months or at 500 hour intervals. Oil level should
be checked through use of the dipstick found on the top
of the pump or by the red dot visible through the oil
gauge window. Oil should be maintained at that level.
HEATING COILS
To Check Water Heater Coil for Leaks:
With the main burners "OFF" start the pumping unit and
allow it to run for a few minutes. With a drop light or
flashlight, check the burner compartment. If no leaks
are visible and water is dripping from the coils, then it is
condensation from the flue gases when the burners are
on.
Condensation from Heating Coil:
When cold water is being pumped into the water heater
coils and the burners are on, condensation will form on
the coils and drip down into the burner compartment.
This will give the appearance of a leaking coil, particu-
larly on cold humid days.
Deliming Coils:
In alkaline water areas, lime deposits can accumulate
rapidly inside the coil pipes. This growth is increased by
the extreme heat build up in the coil. The best preven-
tion for liming conditions is to use high quality cleaning
detergents. In areas where alkaline water is an extreme
problem, periodic use of Manufacturers Deliming Pow-
der (part #9-028008) will remove lime and other depos-
its before coil becomes plugged. (See following Instruc-
tions for use of Deliming Powder.)
Periodic flushing of coils is recommended.
1. Fill a container with 4 gallons of water, then add 1
lb. of deliming powder. Mix thoroughly.
2. Remove nozzle from spray gun assembly and put
spray gun into container. Secure the trigger on the
spray gun into the open position.
3. Attach a short section (3-5 ft.) of garden hose to
machine to siphon solution from an elevated con-
tainer, or add mixture to the float tank. Turn pump
switch on allowing solution to be pumped through
coils and back into the container. Solution should
be allowed to circulate 2-4 hours.
4. After circulating solution, flush entire system with
fresh water. Reinstall wand assembly to spray gun.
MAINTENANCE & SERVICE