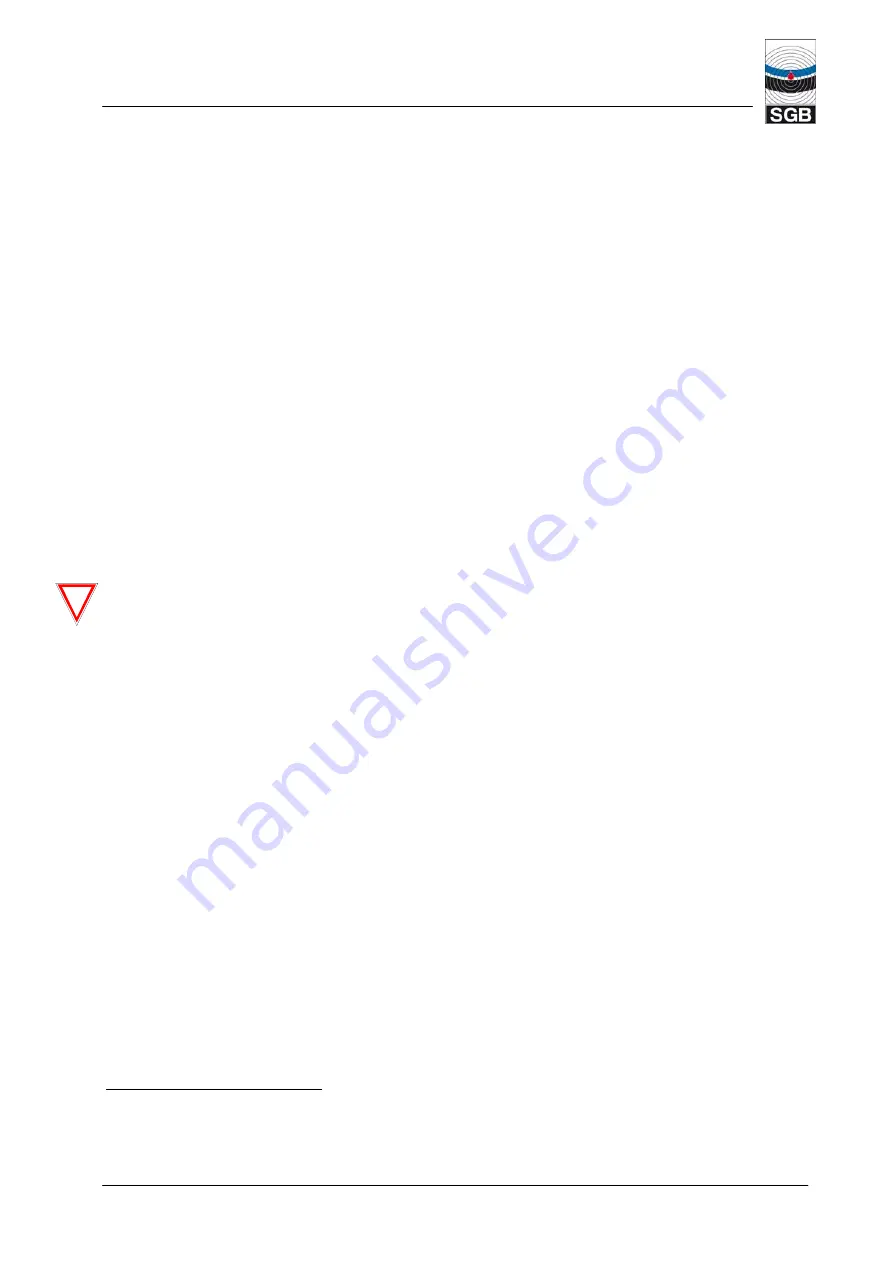
OVERPRESSURE LEAK DETECTOR DLR-GS ..
10/09/2014
- 6 -
4.4. Installation of the connecting lines (leak detector -> interstitial space)
(1) Metal (generally copper) or plastic pipes with a pressure resistance corresponding to at
least the test pressure of the interstitial space – also applies to fittings and unions.
(Observe the temperature range, particularly when using plastic materials.)
(2) Clear width at least 4 mm with inert gas as the leak detection medium
at least 6 mm with air as the leak detection medium
(3) Length should not significantly exceed 50 m, but if it does: use a pipe with a greater clear
width together with bridging pieces.
(4) The full cross-section must be retained. No pinching or kinking
4
.
(5) Metal or plastic pipes laid underground and plastic pipes laid overground should be laid
inside a protective pipe.
(6) The protective pipe should be sealed gas-tight and protected to prevent fluids from
penetrating inside.
(7) Avoid any build-up of electrostatic charge (e.g. when drawing in lines).
(8) For details of the connection technology to be used refer to Work Sheet AB-820 500
(see Information).
4.5. Selecting the pressure reducer
(1) The pressure reducer must have a built-in pressure relief value.
(2) The adjusting range of the selected pressure reducer must be suitable for the specific
application or pressure required. (See Appendix B.)
(3) The maximum pressure which can be set on the pressure reducer must not be greater than
the test pressure of the interstitial space (SGB recommendation).
4.6. Gas canister and pressure reducer (functional tests and commissioning)
(1) After setting up the gas canister securely, remove the protection cap.
(2) Install the pressure reducer on the canister.
(3) Close the shut-off valve on the pressure reducer.
(4) Connect the connecting pipe between the leak detector and the pressure reducer.
(5) Turn the pressure regulating valve all the way back.
(6) Open the canister shut-off valve. (leak test if necessary between pressure reducer and
canister)
(7) Set the pressure on the pressure reducer in accordance with Appendix B using the
pressure regulating valve on the pressure reducer (re-adjustment may be required during
pressure build-up).
4
With plastic pipes, standard commercially available moulded parts (with given bend radiuses) may need
to be used
Содержание DLR-GS PMN Series
Страница 17: ...88 88 57 57 13 04 2007 M1 075 000 45 71 69 01 09 06 2 14 05 77 25 19 bar 0 16 10 bar 0 100 200 300 02 99...
Страница 18: ...99 99 57 57 88 88 88 76 30 02 13 04 2007 M2 075 000 14 05 77 25 19 bar 0 16 10 bar 0 100 200 300 06 2...
Страница 19: ......
Страница 20: ......
Страница 24: ...28 06 2005 Drilling Dimensions 200 300 260 220 T 140 8...