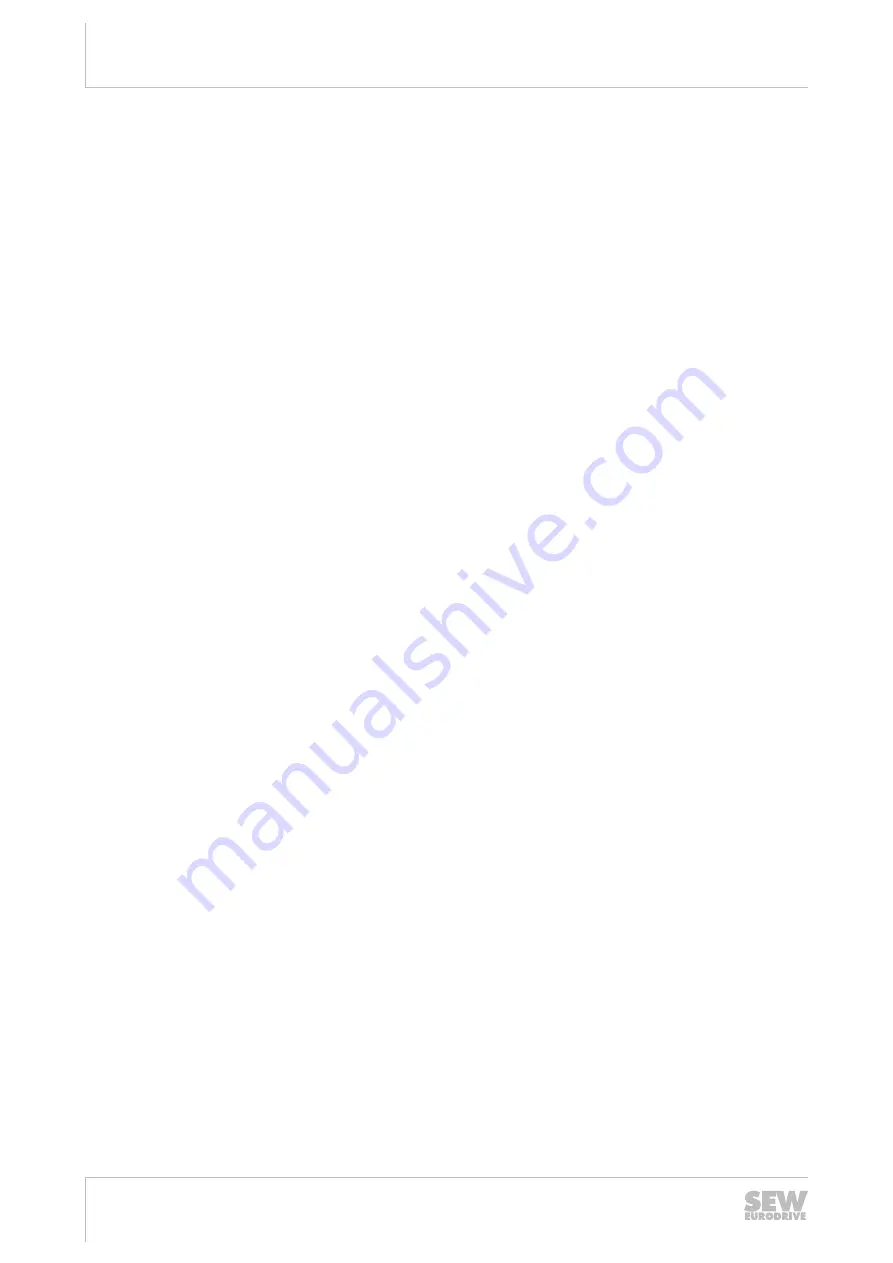
5
Electrical installation
Options
Operating Instructions – AC Motors
112
5.14.10 Installation notes for encoders
When connecting the encoder to the inverter, observe the provided wiring diagrams
and the information in these operating instructions as well as the operating instruc-
tions/wiring diagrams of the inverter and the operating instructions/wiring diagrams
provided with the third-party encoder.
Proceed as described in chapter "Motor and brake maintenance – preliminary
work" (→
123) to mount the encoders. Observe the following information:
•
Maximum line length (inverter to encoder):
– 100 m with a capacitance per unit length core – shield ≤ 110 nF/km
– 100 m with a capacitance per unit length core – core ≤ 85 nF/km
•
Core cross-section: 0.20 – 0.5 mm
2
; recommendation ≥ 0.25 mm
2
•
Use shielded cable with twisted pair cores and apply shield over large area on
both ends:
– In the cable gland of the encoder connection cover or in the encoder connector
– To the inverter on the electronics shield clamp and to the housing of the D-sub
connector
•
Install the encoder cables separately from the power cables, maintaining a dis-
tance of at least 200 mm.
•
Compare the operating voltage with the permitted operating voltage range on the
encoder nameplate. Deviations in the operating voltage may overheat and damage
the encoder.
•
SEW-EURODRIVE recommends the use of stabilized voltage sources and separ-
ate supply systems for encoder or other sensor components and active compon-
ents such as switches and light barriers.
•
Supplies with voltage transients and interferences higher than the supply voltage
U
B
are not permitted.
•
Observe the clamping area of 5 to 10 mm of the cable gland of the connection
cover. If you use cables with a different cross section, you have to replace the
provided cable gland with another suitable EMC-compliant cable gland.
•
The cable glands for the cable entry must meet the following conditions:
– Cramping area is suitable for the used cable(s)
– The IP degree of protection of the encoder connection is at least as high as the
IP degree of protection of the actual encoder
– The operating temperature range matches the designated ambient temperature
range.
•
Check the flawless state and the proper seat of the connection cover gasket.
•
Tighten the screws of the connection cover with a tightening torque of 2.25 Nm.
25851535/EN – 02/2019
Содержание DR 315 Series
Страница 2: ...SEW EURODRIVE Driving the world...
Страница 264: ......
Страница 265: ......
Страница 266: ......
Страница 267: ......