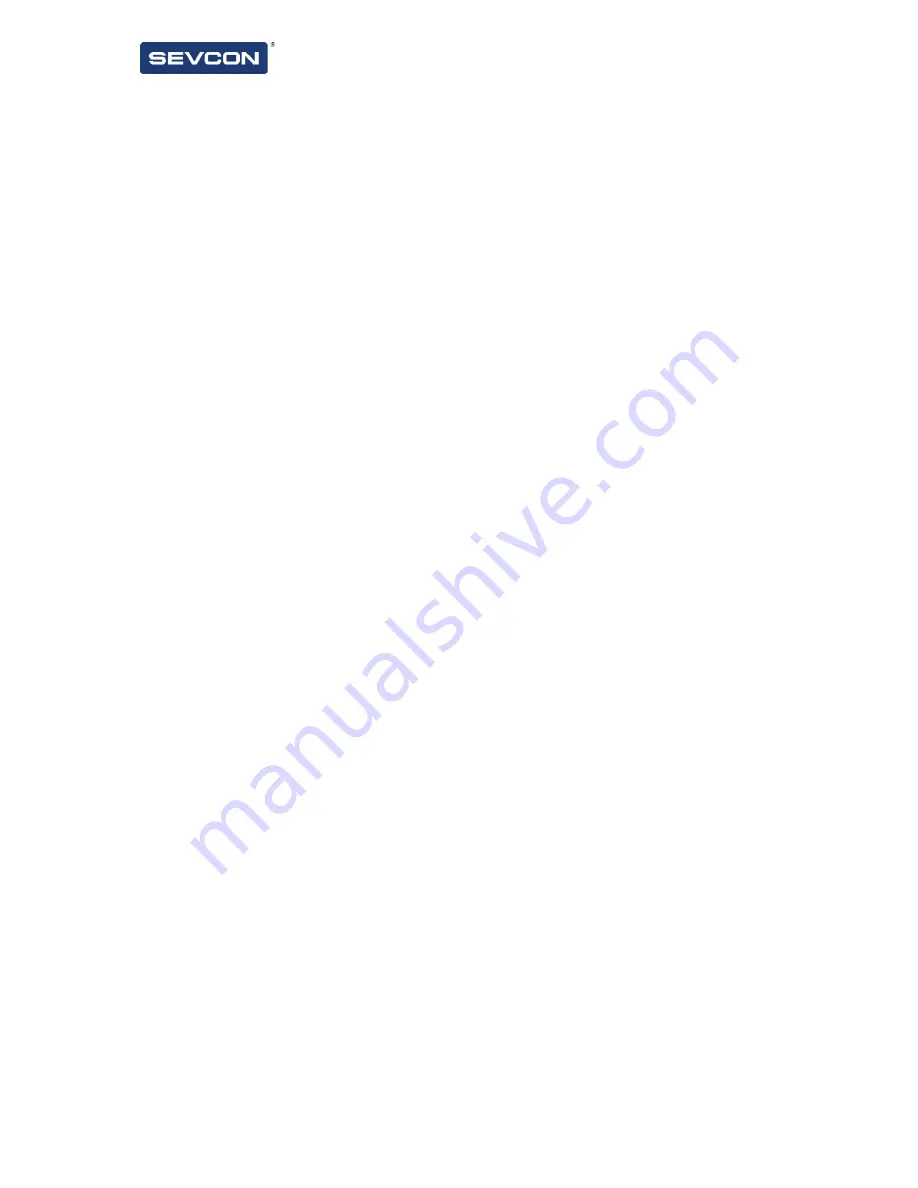
Doc. # 177/52701
Rev3
2-6
Dual traction motor
In the case of dual traction motors, there is additional processing of the associated steering
signal (from a potentiometer or switches) in order to generate separate torque demands for the
left and right motors of the vehicle. This allows the two motors to be operated at different speeds,
which greatly assists in turning the vehicle and prevents wheel scrub. After the torque demands
have been generated, the operation of each motor control system is as described in the case of
a single traction motor.
Pump motors
Pump motor control is similar to traction motor control, although motion is requested using a
different combination of switches.
Interfaces
In addition to its motor control functions, Gen4 offers many other functions designed to interface
with electric vehicles. A variety of digital and analogue input sources are supported, as listed in
‘Signal connections’ on page 3-14.
Voltage and current control of up to three contactors or proportional valves is provided by Gen4,
and includes built-in freewheeling diodes for spike suppression. All I/O on the Gen4 controller is
protected against short-circuit to the battery positive and negative terminals.
Connectivity and interoperability with other system devices (for example another Gen4 controller)
using a CANbus and the CANopen protocol is provided. In addition to in-service operation, the
CANopen protocol allows the controller to be commissioned using the Calibrator handset or
Sevcon’s DVT tool. In addition Sevcon’s SCWiz PC based tool provides the function to self-
characterize most induction motors and hence simplify the process of putting a new motor into
service.
For simple visual diagnosis of system faults and to monitor system status, a green LED is
provided on the body of the controller. It is continuously lit when there is no fault but flashes a
different number of times, in a repeated pattern, when there is a fault. The number of flashes
indicates the type of fault (see ‘’ on page 1).
Master-slave operation
The Gen4 controller contains both master and slave functions as shown in Figure 4. They
operate as follows:
Slave function:
implements the CANopen Generic I/O Profile (DS401) and the Drives and
Motion Control Profile (DSP402).
Master function:
implements vehicle functionality (traction and pump control) and CANopen
network management.
Содержание Gen4
Страница 1: ...Gen4 Applications Reference Manual Document no 177 52701 Rev 3 3 ...
Страница 9: ...Chapter 1 Introduction ...
Страница 13: ...Chapter 2 About the Gen4 ...
Страница 25: ...Chapter 3 Installation ...
Страница 45: ...Chapter 4 Specification ...
Страница 47: ...Specification Doc 177 52701 Rev 3 3 4 3 CAUTION Repetitive short circuits may damage the controller ...
Страница 50: ...4 6 Isolation Any terminal to the case Meets EN1175 1 1998 and ISO3691 Complies with IEC 60664 ...
Страница 53: ...Specification Doc 177 52701 Rev 3 3 4 9 Dimensions Size 2 models Size 4 models ...
Страница 54: ...4 10 Size 6 models ...
Страница 55: ...Chapter 5 System design ...
Страница 60: ...5 6 Single traction wiring diagram Figure 13 Single traction wiring diagram ...
Страница 61: ...System design Doc 177 52701 Rev 3 3 5 7 Single pump wiring diagram Figure 14 Stand alone pump wiring diagram ...
Страница 63: ...System design Doc 177 52701 Rev 3 3 5 9 On board fuse See On board fuse mounting on page 3 11 ...
Страница 64: ...5 10 Figure 15 Dual traction wiring diagram ...
Страница 70: ......
Страница 71: ...Chapter 6 Configuration ...
Страница 110: ......
Страница 111: ...Chapter 7 Monitoring Gen4 ...
Страница 122: ......
Страница 123: ...Monitoring Doc 177 52701 Rev 3 3 A 1 ...