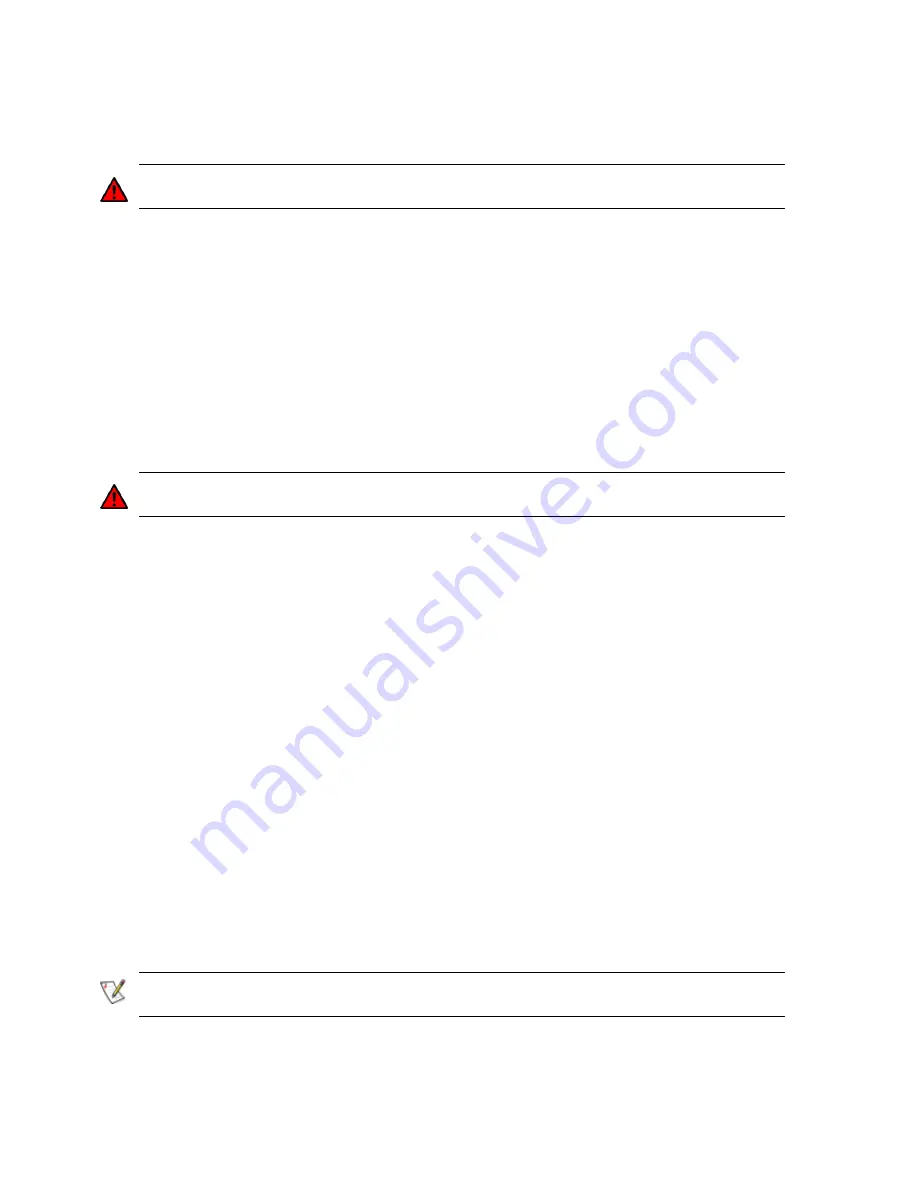
Configuration
Doc. # 177/52701
Rev. 3.3
6-31
Belly Switch
WARNING: Ensure the belly switch is only mapped to a digital input when required.
Activation of this input can cause a drive condition to occur.
The belly switch is normally connected to the end of the tiller arm on class 3 vehicles. When
activated it forces a drive condition in forward at a user specified throttle value and maximum
speed for a specified time.
To configure belly:
Ensure the belly switch is mapped to a digital input.
Specify the maximum belly speed at 290C
h
sub-index 2.
Specify a belly throttle at 290C
h
sub-index 1. This will determine the torque demand in
torque mode or speed demand in speed mode.
Specify a belly time out at 290C
h
sub-index 3. The belly function will cease after this time
has expired.
Drivability select switches
WARNING: Ensure the driveability switches are only mapped to digital inputs when
required. Activation of these inputs can cause driving parameters to change.
There are two drivability select switches (2126
h
and 2127
h
).
To enable either of these they must be mapped to digital inputs. When they are active, the
corresponding drivability profiles (2921
h
and 2922
h
) are applied.
See Driveability profiles (page 6-26) for more information.
Economy
The economy input is an analogue input which can be used to increase vehicle efficiency and
extend battery life. It is normally controlled using a potentiometer mounted on the vehicle’s
dashboard. The economy voltage (2222
h
) must be mapped to an analogue input.
Efficiency is improved by reducing the acceleration rate or the maximum torque.
Configure the economy input at object 2912
h
as follows:
Economy function: select acceleration or torque.
Economy voltage input: These settings are similar to those for the throttle
(see page 6-20).
The economy value calculated from the voltage can be read at 2622
h
.
Pump configuration
The controller can use a mixture of switch and analogue voltages as the pump input. In addition,
the power steer function can be used as an extra input to the pump if the pump motor is required
to supply pump and power steering.
NOTE: Pump motors always run in speed mode. Ensure the motor slave is also configured for
speed mode in 6060
h
.
Содержание Gen4
Страница 1: ...Gen4 Applications Reference Manual Document no 177 52701 Rev 3 3 ...
Страница 9: ...Chapter 1 Introduction ...
Страница 13: ...Chapter 2 About the Gen4 ...
Страница 25: ...Chapter 3 Installation ...
Страница 45: ...Chapter 4 Specification ...
Страница 47: ...Specification Doc 177 52701 Rev 3 3 4 3 CAUTION Repetitive short circuits may damage the controller ...
Страница 50: ...4 6 Isolation Any terminal to the case Meets EN1175 1 1998 and ISO3691 Complies with IEC 60664 ...
Страница 53: ...Specification Doc 177 52701 Rev 3 3 4 9 Dimensions Size 2 models Size 4 models ...
Страница 54: ...4 10 Size 6 models ...
Страница 55: ...Chapter 5 System design ...
Страница 60: ...5 6 Single traction wiring diagram Figure 13 Single traction wiring diagram ...
Страница 61: ...System design Doc 177 52701 Rev 3 3 5 7 Single pump wiring diagram Figure 14 Stand alone pump wiring diagram ...
Страница 63: ...System design Doc 177 52701 Rev 3 3 5 9 On board fuse See On board fuse mounting on page 3 11 ...
Страница 64: ...5 10 Figure 15 Dual traction wiring diagram ...
Страница 70: ......
Страница 71: ...Chapter 6 Configuration ...
Страница 110: ......
Страница 111: ...Chapter 7 Monitoring Gen4 ...
Страница 122: ......
Страница 123: ...Monitoring Doc 177 52701 Rev 3 3 A 1 ...