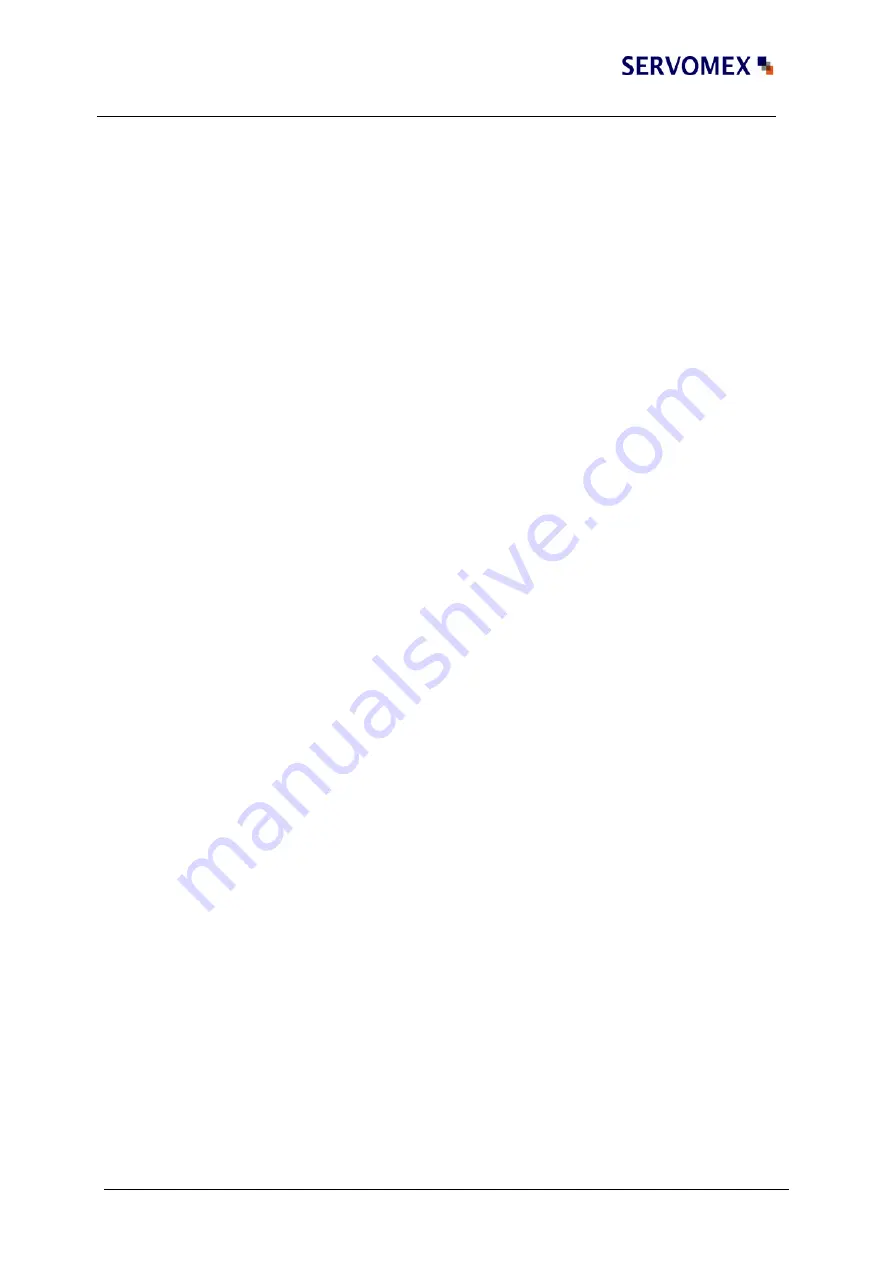
SERVOTOUGH LaserExact Monitor, Operator Manual 02950001A_1
14
C
HAPTER
3
To install the instrument follow the steps below (see also Figure 3-1).
1.
Install the instrument in an upright position. Use the mounting tabs provided
with the analyser.
2.
Connect the sample gas tubes as follows:
Gas INLET 6mm OD (front of unit)
Gas OUTLET 8mm OD (rear of unit)
Metric Swagelok fitting are supplied loose for use, however other
connectors may be used provided they are compatible with the inlet and
outlet pipes provided. Therefore gas inlet and outlet must not be
confused. We recommend stainless steel tubes.
3.
If applicable connect a purge INLET to the alignment chamber (connection
between the inlet and outlet pipes)
4.
Connect optional output signals (4-20 mA, warning relays, etc.) to the
“Auxiliary” terminals inside the cabinet (use the auxiliary cable gland, Figure
6-1). Refer to Section 6.3.
5.
Connect external 4-20 mA temperature and pressure probes (ref. Section 6.2
and 6.5). This is optional as some instruments operate without probes. Input
signals are connected to the terminals inside the cabinet.
6.
Open the gas lines. Check all connections for gas leaks before operating the
monitor.
The SERVOTOUGH LaserExact Monitor can now be switched on. This procedure is
described in Section 3.3.
3.2.2
Purging of laser beam alignment chamber
Note that some instruments may require purging with Nitrogen or clean dry air for
measurement purpose i.e. the target gas must be removed from the internal
measurement path to achieve sufficient measurement accuracy, or to ensure toxic or
flammable gases do not build up within the chamber. Examples are low level O
2
or
CO
2
instruments for measurement or H
2
S or HCl for toxic/flammable.
In this case the laser beam alignment chamber (one Swagelok connection) must be
purged (see Figure 3-2). Since there are optical surfaces inside this chamber, the
cleanness of the gas must be ensured and additional filtering may be necessary.
The purge flow must not be high to avoid overpressure inside. It is recommended
setting the flow to around 0.5 l/min. The purge flow will be vented to atmosphere
through the purge outlet port at the base of the cabinet (see Figure 3-2).
Содержание SERVOTOUGH LaserExact 2950
Страница 2: ...This page intentionally blank...
Страница 6: ...SERVOTOUGH LaserExact Monitor Operator Manual 02950001A_1 IV This page intentionally blank...
Страница 69: ...SERVOTOUGH LaserExact Monitor Operator Manual 02950001A_1 APPENDIX 63...
Страница 70: ...SERVOTOUGH LaserExact Monitor Operator Manual 02950001A_1 64 APPENDIX...
Страница 71: ...SERVOTOUGH LaserExact Monitor Operator Manual 02950001A_1 APPENDIX 65...