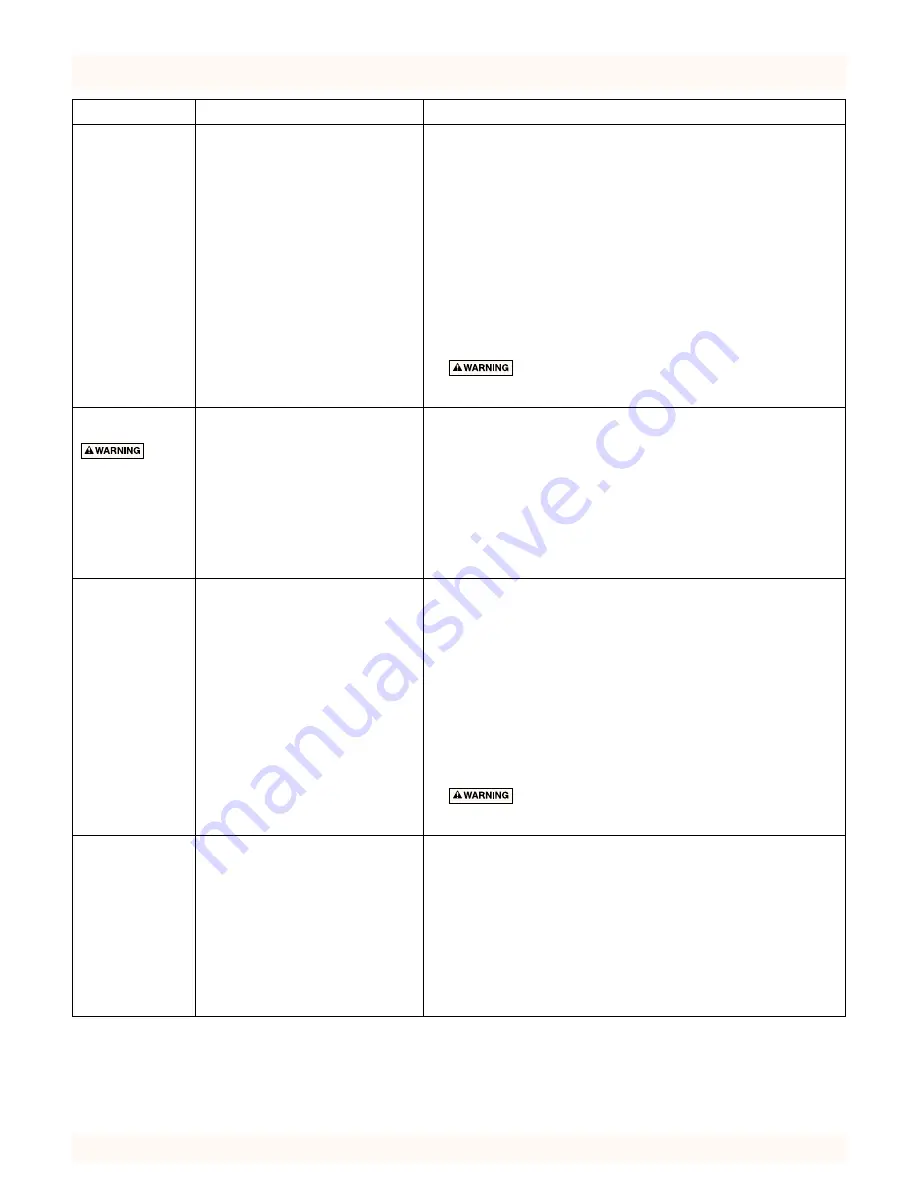
HELPFUL HINTS – TROUBLES, CAUSES & REMEDIES
12
Trouble
Causes
Remedies
Fuses blow or
A. Fuses or wires too small.
A. Replace with correct sizes (see Table II, Page 3).
overload protector
B. Low or high voltage.
B. While motor is running, voltage should not exceed plus 10% or minus 5%
trips when motor
of rated voltage shown on motor nameplate. Call electric power company
starts.
to adjust line voltage if it is not within these limits.
C. Motor stuck or binding (abrasive
C. Pull pump and clean it. Before reinstalling pump, clean well carefully (see Page 10)
material, such as sand, may lock
for well development procedure). If necessary, clean well carefully with sand
pump).
pump or by bailing.
NOTICE: If well is sandy or dirty and cannot be cleaned or a suitable sand
screen installed, do not reinstall pump.
D. Cable splices or motor windings
D. Consult competent electrician or service technician.
grounded, shortened, or open.
E.
3-Wire only: Cable leads may be improp-
E. Check wiring diagram on control center panel (also see Figures 4 and 5,
erly connected in control center.
Page 6, in this manual) and color coding of drop cable.
F.
3-Wire only: There may be a
F. Have a competent electrician examine all connections and wiring
broken wire in the control center.
in control panel. If necessary, repair them.
G.
3-Wire only: Starting or running
G. Inspect capacitors (see Figures 4 and 5, Page 6). Have competent
capacitor in control center may be
electrician check capacitors. Replace if necessary.
defective or vented (blown out).
Hazardous voltage. Can shock, burn, or cause death.
Capacitors may still carry voltage charges even after being disconnected
from wiring. Have them checked by a competent electrician.
A. No voltage to motor.
A. With voltmeter check 1) fuse box to make sure full voltage is available; 2) pressure
switch terminals, to make sure pressure switch is passing voltage correctly;
and 3) terminal strips in control center or disconnect switch box to make sure
voltage is available there. 1-1/2 through 3 HP: Push red overload reset button(s)
on bottom of control center.
B. Cable splices or motor windings may be
B. Consult competent electrician or service technician.
grounded, shorted, or open-circuited.
Do not attempt to disassemble pump or motor.
C. Open circuit in control center (3-wire
C. Examine all connections and wires; examine terminal strips in
only); faulty connections; faulty wires.
control center (3-wire only); repair if necessary.
D. Faulty pressure switch.
D. Check pressure switch; replace if necessary.
E.
3-Wire only: Cable leads improperly
E. Check wiring diagram on control center panel (also see Figures 4 and 5,
connected in control center.
Page 6, in this manual) and color coding of drop cable.
Pressure switch fails
A. Voltage too low; motor will run slowly,
A. Have a competent electrician verify voltage at electrical disconnect box (2-wire) or
to shut off pump.
causing low discharge pressure (head)
control center (3-wire) while pump is operating. If voltage is low, power company may
and high operating current draw.
need to raise it or installation may require larger wire. Discuss with power company
or licensed electrician. Check voltage with a recording meter if trouble reoccurs.
B. Faulty pressure switch.
B. Replace switch.
C. Impellers or diffusers worn (due to
C. Adjust switch to allow for reduced pressure coming from pump. If
sand or abrasives in water or running
adjustment does not solve problem, it may be necessary to replace
pump while it is air- or gas-locked) to
pump. If well water contains enough sand to cause undue wear on
the point that pump does not develop
the pump, clean out well or install a suitable sand screen before
sufficient pressure to activate switch.
reinstalling pump. See “Well Development”, Page 10.
D. Drop pipe leaking.
D. Raise one length of pipe at a time until leak is found. When water
stands in pipe, there is no leak below that point.
E. Water level in well may become too
E. Lower pump further into well, but make sure it is at least five feet above well bottom.
low when pump is running.
Install a valve in discharge pipe between pump and pressure tank. Use valve to
restrict flow until discharge rate does not exceed well recovery rate.
To prevent possibility of dangerous high pressure, install a
relief valve in discharge pipe between pump and flow restriction valve.
Relief valve must be capable of passing full pump flow at 75 PSI.
Fuses blow or
A. Low or high voltage.
A. While motor is running, voltage should not exceed plus 10% or minus 5% of rated
overload protector
voltage shown on motor nameplate. Call Power company to adjust line voltage
trips when motor
if it is not within these limits.
is running.
B.
3-Wire only: High ambient
B. Make sure control center is installed out of direct sunlight.
(atmospheric) temperature.
C.
3-Wire only: Control Center wrong
C. Compare horsepower and voltage rating of motor (from motor nameplate) with those
horsepower or voltage for installation.
of control center (from control center nameplate). These numbers must match.
D. Wire size too small. improperly
D. See Table II, Page 3, and make sure wire size matches
connected in control center.
specifications in table.
E. Cable splices or motor windings
E. Consult competent electrician or service technician to determine
may be grounded, shorted or
if this is the cause of the problem or not.
open-circuited.
Do not attempt to disassemble pump or motor.
Motor will not start but
does not blow fuses.
Hazardous voltage.
Can shock, burn,
or cause death.
Only competent electri-
cians should work on
electrical service.