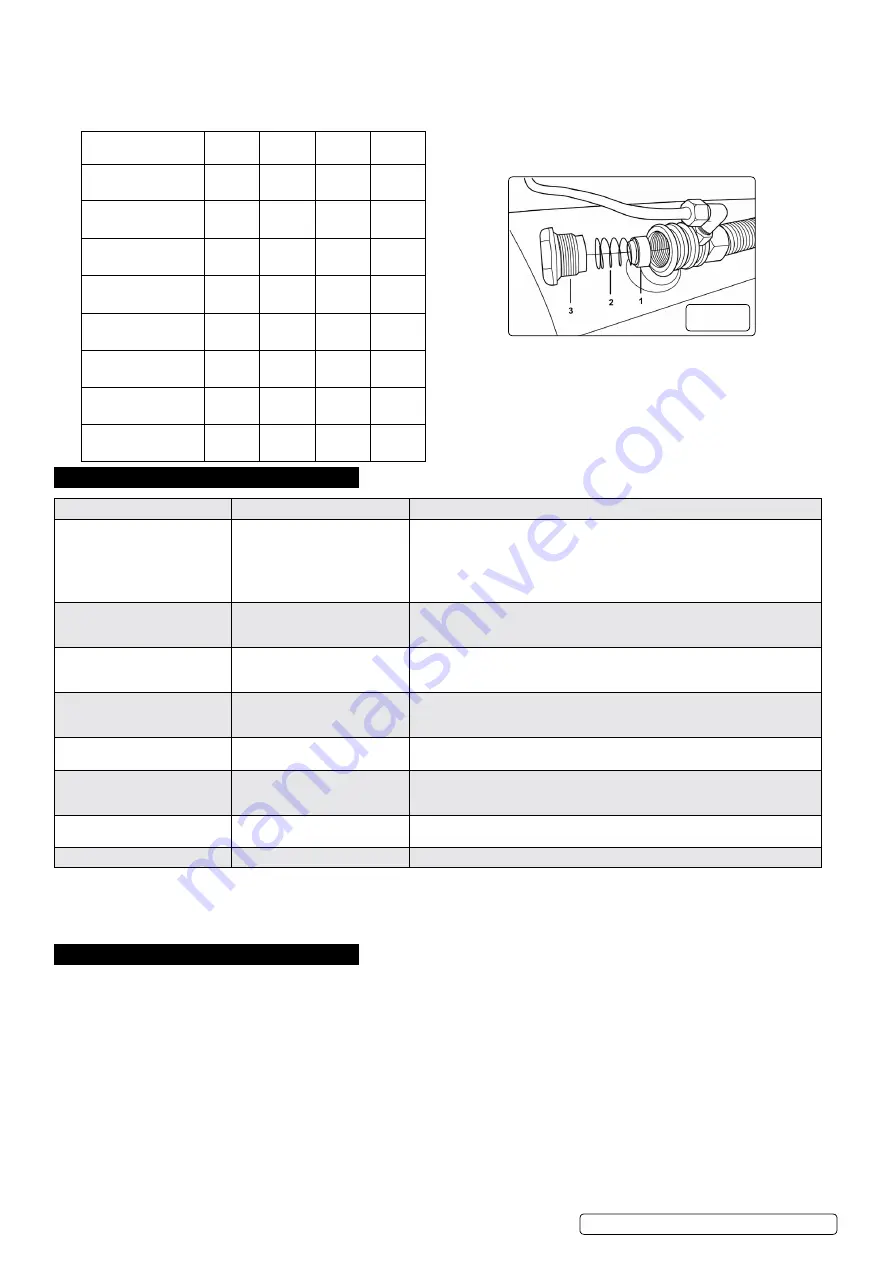
6.7.
iNspeCtioN of pressure tANK both iNsiDe AND out
6.7.1.
Under the PRESSURE SYSTEMS SAFETY REGULATIONS 2000 it is the responsibility of the owner of the compressor to initiate a
system of inspection that both defines the frequency of the inspection and appoints a person who has specific responsibility for carrying
out the inspection
.
6.8.
sCheDuleD mAiNteNANCe tAble
maintenance
Daily
100
hours
200
hours
500
hours
drain condensation
•
Check
oil level
•
Clean
I
ntake filter
•
Check for
oil leaks
•
Check
Cut-out
•
Replace
oil
•
R
eplace air filter
•
C
heck tube fittings and
electrical connections
•
7. troubleshootiNG
fAult
CAuse
remeDY
Pressure drop in the tank.
1.
Air leaks at connections.
2.
Air leaks from safety valve.
3.
Air leaks from cylinder head gasket.
1.
Run compressor to maximum pressure, switch off. Brush soap solution over
connections and look for bubbles. Tighten connections showing leaks. If problem
persists, contact Authorised Service Agent.
2.
operate the safety valve manually by pulling on the ring. If valve continues to
leak when in the closed position it should be replaced.
3.
Check tightness of head bolts, if leak continues contact Authorised Service Agent.
Pressure switch valve leaks when
compressor is idle.
non-return valve seal defective.
e
mpty the air tank. Referring to (fig.7), remove the non-return valve cap (fig.7.3),
spring (fig.7.2) and seal (fig.7.1). Clean the seal and its seat, or if necessary replace
the seal and refit.
Air leaks from tank body or tank
welds.
Internal corrosion caused by
infrequent tank draining or non
permitted modifications to tank.
Tank could rupture or explode. Cannot be repaired.
DisCoNtiNue use immeDiAtelY
Motor stops and will not restart.
1.
Thermal cut out has operated.
2.
Supply fuse has tripped.
1.
Allow unit to cool for 30 minutes then press reset button.
2.
Reset fuse and restart unit. If repeated tripping occurs, replace the check valve
or contact Authorised Service Agent.
Compressor stops and will not
restart.
Motor failure.
Contact Authorised Service Agent.
Compressor does not stop at
maximum pressure
1.
Pressure switch fault.
2.
Filter clogged
3.
Head gasket or valve fault
1.
Contact Authorised Service Agent.
2.
Replace filter element.
3.
Contact Authorised Service Agent.
Compressor noisy with metallic
knock
Bearing or piston damage
Contact Authorised Service Agent.
excessive moisture in discharged air High humidity environment
drain tank after each use
4 pC Air ACCessorY Kit
SUPPLIED WITH MODEL NO:
sAC5020ApK
8. sprAY GuN sAfetY
WArNiNG!
disconnect the spray gun from the air supply before changing accessories, servicing or performing any maintenance.
9
Familiarise yourself with this products application and limitations, as well as the specific potential hazards peculiar to the spray gun.
Paint cup remains pressurised after gun is disconnected from air line.
8
Do Not
pull the trigger, but release the pressure by gently opening cup.
9
Maintain the spray gun in good condition (use an authorised service agent).
9
Replace or repair damaged parts. Use recommended parts only. Non authorised parts may be dangerous and will invalidate the
warranty.
9
locate the spray gun in an adequate working area for its function, keep area clean and tidy and free from unrelated materials, and
ensure there is adequate ventilation and lighting.
9
Keep the spray gun clean for best and safest performance.
9
Wear approved respiratory protection and safety eye goggles.
9
Remove ill fitting clothing. Remove ties, watches, rings, and other loose jewellery, and tie back long hair.
9
Keep children and unauthorised persons away from the working area.
9
Avoid unintentional operation.
8
Do Not
point spray gun at yourself, at other persons or animals.
fig.7
Original Language Version
© Jack Sealey limited
S
AC5020A, SAC5020APK Issue 1 13/06/19