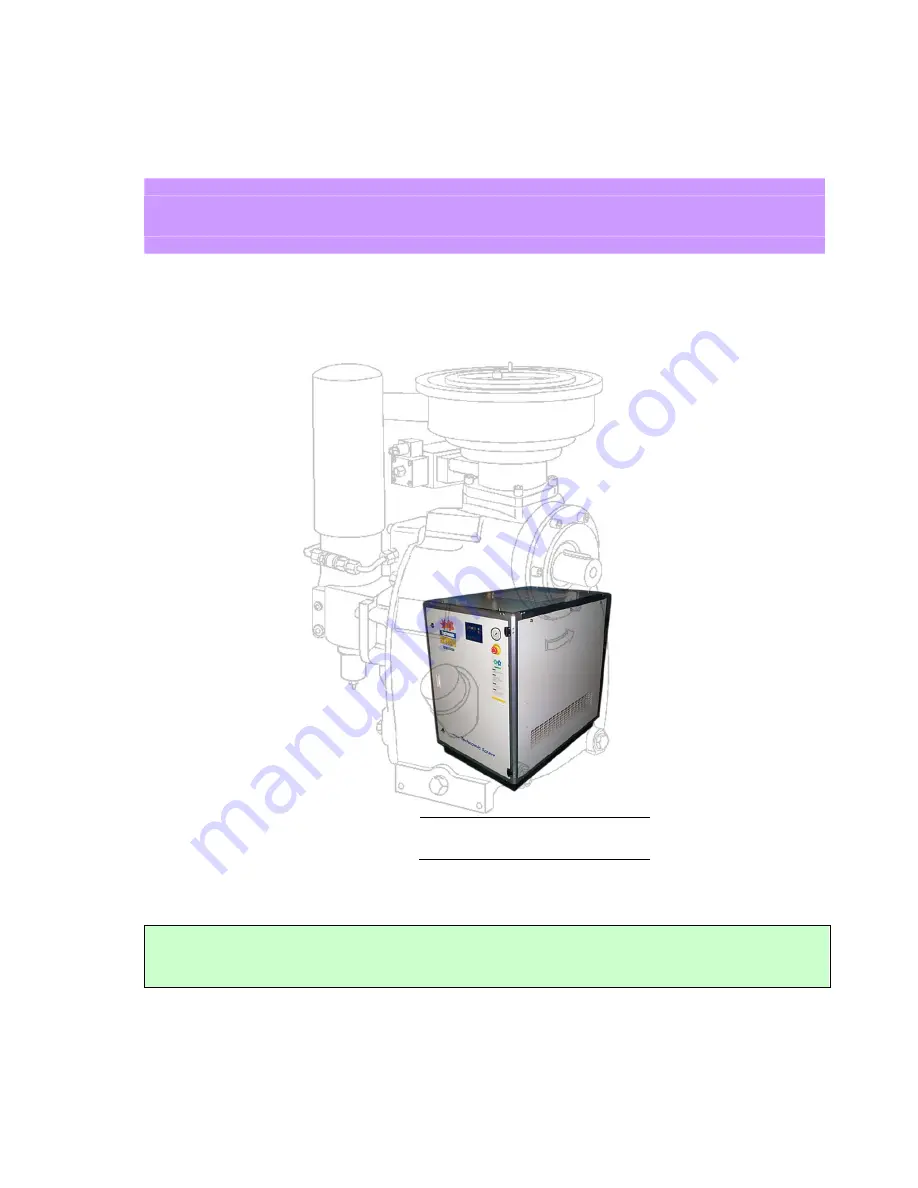
COAIRE M-Series
EXTROLLER Control System
MAINTENANCE MANUAL AND PARTS LIST
MODEL
CHSA-7.5M CHSA-10M
CHSA-15M CHSA-20M
SERIAL NO. :
MODEL NO. :
MODEL CHSA-15CHSA-20M
COAIRE TECHNOLOGIES, CORPORATION
All rights reserved Printed in USA
ROTARY SCREW AIR COMPRESSORS
For proper and safe use of the compressor, please follow all instructions and safety precautions as identified in
this manual, along with general safety regulations and practices.
Summary of Contents for CHSA-10M
Page 31: ...27 AIR END NK40 ...
Page 33: ...29 AIR END NK60 ...
Page 34: ...30 Appendix B 1 PART LIST FOR MODEL CHSA 7 5M 1 2 ...
Page 35: ...31 1 PART LIST FOR MODEL CHSA 7 5M 2 2 ...
Page 36: ...32 2 PART LIST FOR MODEL CHSA 10M 1 2 ...
Page 37: ...33 2 PART LIST FOR MODEL CHSA 10M 2 2 3 PART LIST FOR MODEL CHSA 15M 1 2 ...
Page 38: ...34 3 PART LIST FOR MODEL CHSA 15M 2 2 ...
Page 39: ...35 4 PART LIST FOR MODEL CHSA 20M 1 2 ...
Page 40: ...36 ...
Page 41: ...37 4 PART LIST FOR MODEL CHSA 20M 2 2 ...
Page 42: ...38 C Wiring Diagram for Model CHSA 7 5 10 15 20M ...
Page 43: ...39 Appendix D 1 Outline Drawing for Model CHSA 7 5 10M ...