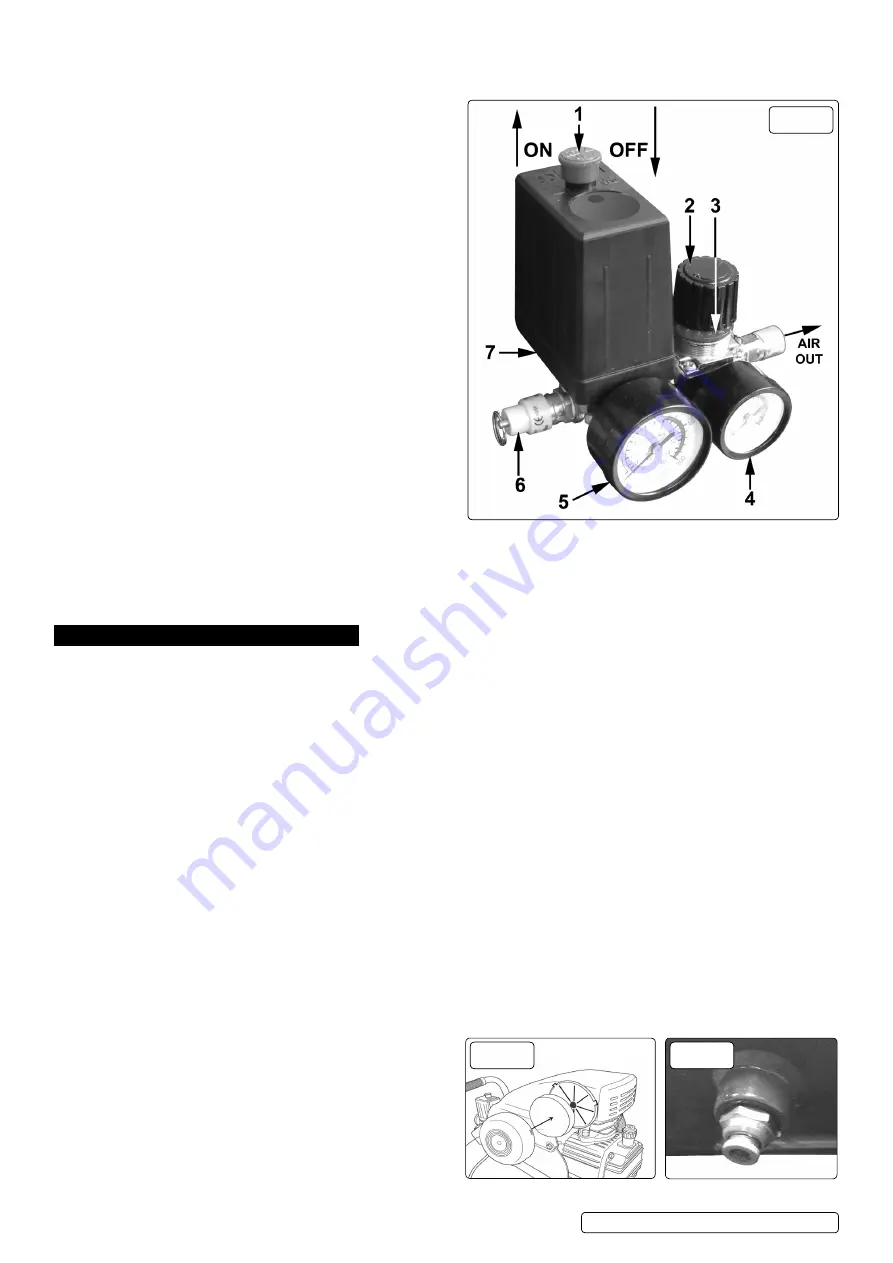
5.9.
You can now begin to use the tool. The compressor will operate automatically cutting in and out as required to restore the air pressure
in the tank. The pressure switch (fig.4.7) stops the motor when the maximum tank pressure is reached and restarts it when pressure
falls below the minimum threshold - approximately 2bar (29psi) less than the maximum pressure.
note: a) If the motor does not cut in and out, but runs continuously when
using an air appliance, the capacity of the compressor may be too
small for the appliance.
b) The main gauge (fig.4.5) indicates the pressure inside the main
tank,
Not
the pressure supplied to the air equipment, which is
shown on the smaller gauge (fig.4.4). Should the pressure in the
main tank exceed the pre-set switch (fig.4.7) maximum, the safety
valve (fig.4.6) will activate.
WArNiNG! for this reason Do Not tamper with, or adjust, the
switch or the safety valve.
When the compressor is not being used set the regulated pressure
to zero so as to avoid damaging the pressure regulator.
5.10.
To stop the compressor press down the main switch (fig.4.1).
When the compressor stops there will be a whistling sound as
compressed air is vented from the compressor head.
8
Do Not
, other than in an emergency, stop the compressor by
switching off the mains power, or by pulling the plug out, as the
pressure relief will not then occur and motor damage may result
upon restart.
5.11.
When you have finished using the compressor unplug the unit from
the mains power supply.
5.12.
Set the outlet pressure on the regulator to zero.
5.13.
Remove the air line and air tool.
5.14.
The tank must now be drained. This will release the air left in the
tank and drain away condensation that may have formed within
the tank. Choose a suitable location for this operation and/or
make provision to collect the condensation.
Wear ear and eye
protection.
Open the tank drain valve (See fig.6) slowly allowing
air and moisture to bleed from the tank. After bleeding close the drain valve to prevent debris building up in the valve.
WArNiNG! Water that is allowed to remain in the tank during storage will corrode and weaken the air tank which could cause
the tank to rupture. to avoid serious injury drain the tank after each use or daily.
5.15.
sAfetY feAtures
thermal cut out:
If the unit overheats the thermal cut out will operate and shut the unit down. Allow the unit to cool down then press the
reset button, located just inside the pump cover.
6. mAiNteNANCe
WArNiNG!
Before performing any maintenance operation, switch off the compressor, disconnect from electricity supply and release
all air from the tank. In order to keep the compressor in good working condition, periodical maintenance is essential.
6.1.
After the first 50 working hours replace the lubricating oil - see item 6.3.
6.2.
operAtioNs to be CArrieD out DAilY:
6.2.1.
Drain condensation, place a container under the valve and open the valve by turning anti-clockwise (fig.6). Retighten the valve.
6.2.2.
Check that all nuts and bolts are tight, particularly those retaining the crankcase and cylinder head.
6.3.
operAtioNs to be CArrieD out everY 100 hours:
(or more frequently, if the compressor operates in a very dusty atmosphere).
6.3.1.
Check oil level and, if necessary, top it up.
6.3.2.
Remove the air filter element by unscrewing the filter holder (fig.5) and prising open the holder. Clean it by blowing through with an
air line at low pressure, from the clean side. Alternatively, wash it in soapy water, rinse and dry.
Do Not
operate the compressor
without the filter as foreign bodies or dust could seriously damage the pump.
6.3.3.
Check for oil leaks.
6.4.
operAtioNs to be CArrieD out everY 200 hours:
6.4.1. Replace the lubricating oil. Remove the oil filler/breather (fig.5) and unscrew the drain bolt (fig.5), drain the oil into a suitable
container. drain when the compressor is hot so that the oil drains rapidly and completely. Incline the compressor to ensure complete
drainage. Replace the drain bolt and refill with fresh oil through the filler aperture.
Do Not
overfill.
6.4.2.
Replace oil filler/breather (fig.5).
6.5.
reCommeNDeD oil:
6.5.1.
Suitable for room temperatures ranging from +5ºC to +25ºC: SeAleY CPo or equivalent SAe 40 compressor oil.
6.5.2.
Room temperature below +5ºC: SAe 20 compressor oil.
WArNiNG! Never mix different oils and Do Not use non-detergent/low quality oils as the compressor may be damaged.
6.5.3.
dispose of waste oil only in accordance with local authority requirements.
6.5.4.
Check the automatic cut-out at maximum pressure and the automatic cut-in at 2 bar below that.
6.6.
operAtioNs to be CArrieD out everY 500 hours:
6.6.1.
Replace air filter.
6.6.2.
Check all tube fittings and electrical connections.
importANt! failure to carry out maintenance tasks may
invalidate the warranty on your compressor.
WArNiNG
- Air contaminants taken into the compressor will
affect optimum performance. Example: Body filler dust or paint
overspray will clog the pump intake filter and may cause
internal damage to pump/motor components.
Note:
Any parts damaged by any type of contamination will not
be covered by warranty.
fig.4
fig.5
fig.6
Original Language Version
© Jack Sealey limited
S
AC5020A, SAC5020APK Issue 1 13/06/19