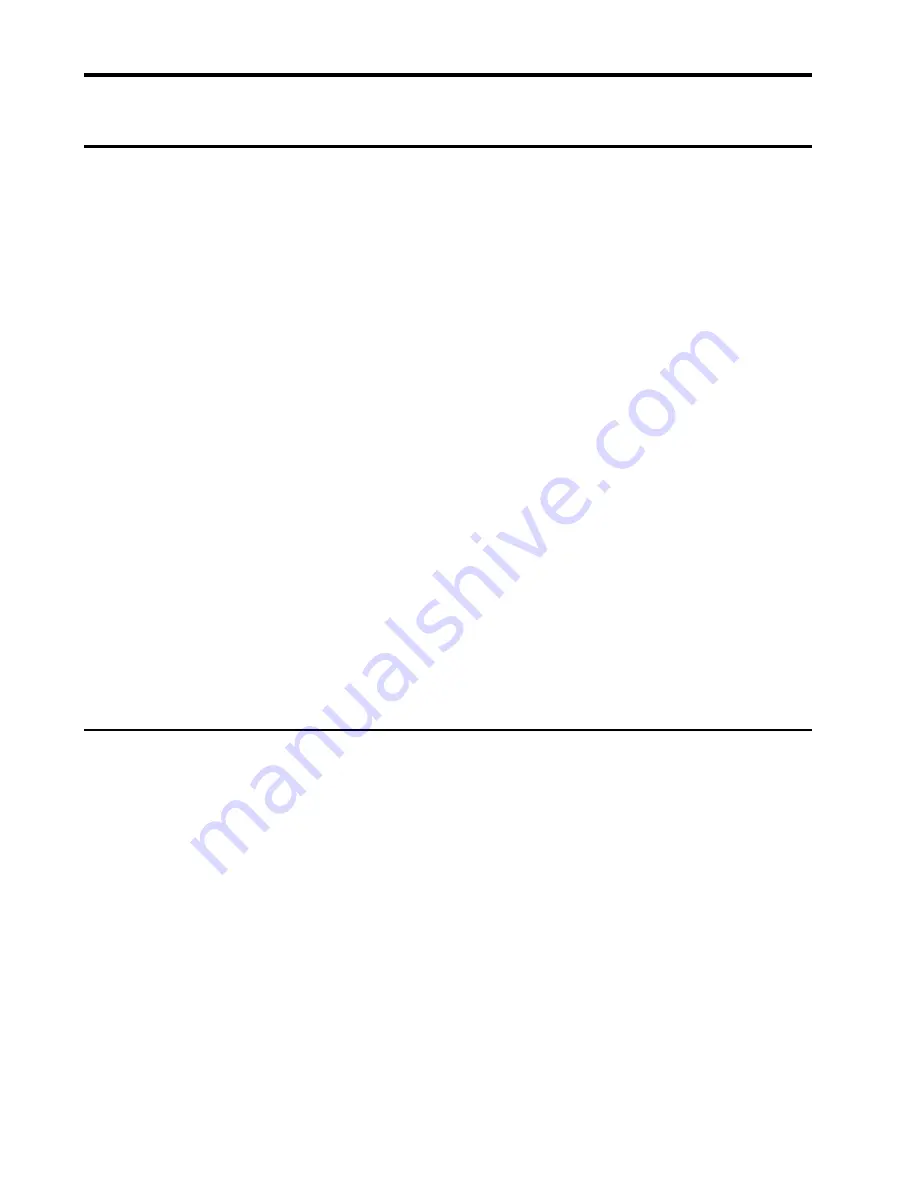
10
Viper 200 LTO Product Manual
Environmental requirements
The following table lists the environmental specifications for the Viper drive mechanism.
Specification
Operational
Non-operational
Temperature
+50
°
to +104
°
F
(+ 10
°
to + 40
°
C)
–40
°
to +149
°
F
(–40
°
to + 66
°
C)
Airflow requirements
Internal: 9 CFM (front to back)
Thermal gradient
11
°
C per hour (10-40
°
C)
11
°
C per hour (10-40
°
C)
Relative humidity
20% to 80% non-condensing
10% to 95% non-condensing
Humidity gradient
10% per hour
10% per hour
Maximum wet bulb temp.
78.8
°
F (26
°
C)
No condensation
Altitude
max 10,000 feet MSL (at 25
°
C)
40,000 feet (power off)
Shock (1/2 sine wave)
2 Gs peak, 10 msec
10 Gs peak, 10 msec
Vibration (Sweep Test)
0.01 inches DA (5-22 Hz)
0.50 G peak (22–500 Hz)
sweep rate 5-500Hz (1 oct/min)
1.0 G (5-500Hz;
sweep rate 0.5 oct/min)
Acoustic level idling
(A-wt sum)
38 dBA maximum
5.0 LwA Bels
—
Acoustic level operational
(A-wt sum)
41 dBA maximum
5.5 LwA Bels
—
Injected noise
The internal drive will operate without degradation of error rates with 100 mV of noise
injected between the chassis and 0 V at the power connector at any frequency
between 45 Hz and 10 MHz.
Reliability
The Viper drive is designed for maximum reliability and data integrity. The following
table summarizes the reliability specifications.
Specification
Description
Non-recoverable error rate
< 1 in 10
17
bits
Error recovery and control
- Error-correction code techniques (C1 and C2 ECC)
- Read-after-write (RAW)
- Error monitoring and reporting (error log)
- Retry on read
Mean time between failures
(MTBF)
250,000 hours MTBF at 100% duty cycle: power
applied and tape moving continuously
(External drive; 50,000 hours at full load and 25
°
C)
Cartridge load/unload
300,000 cartridge load/unload cycles (no thread)
Mean time to repair (MTTR)
Less than 0.5 hour